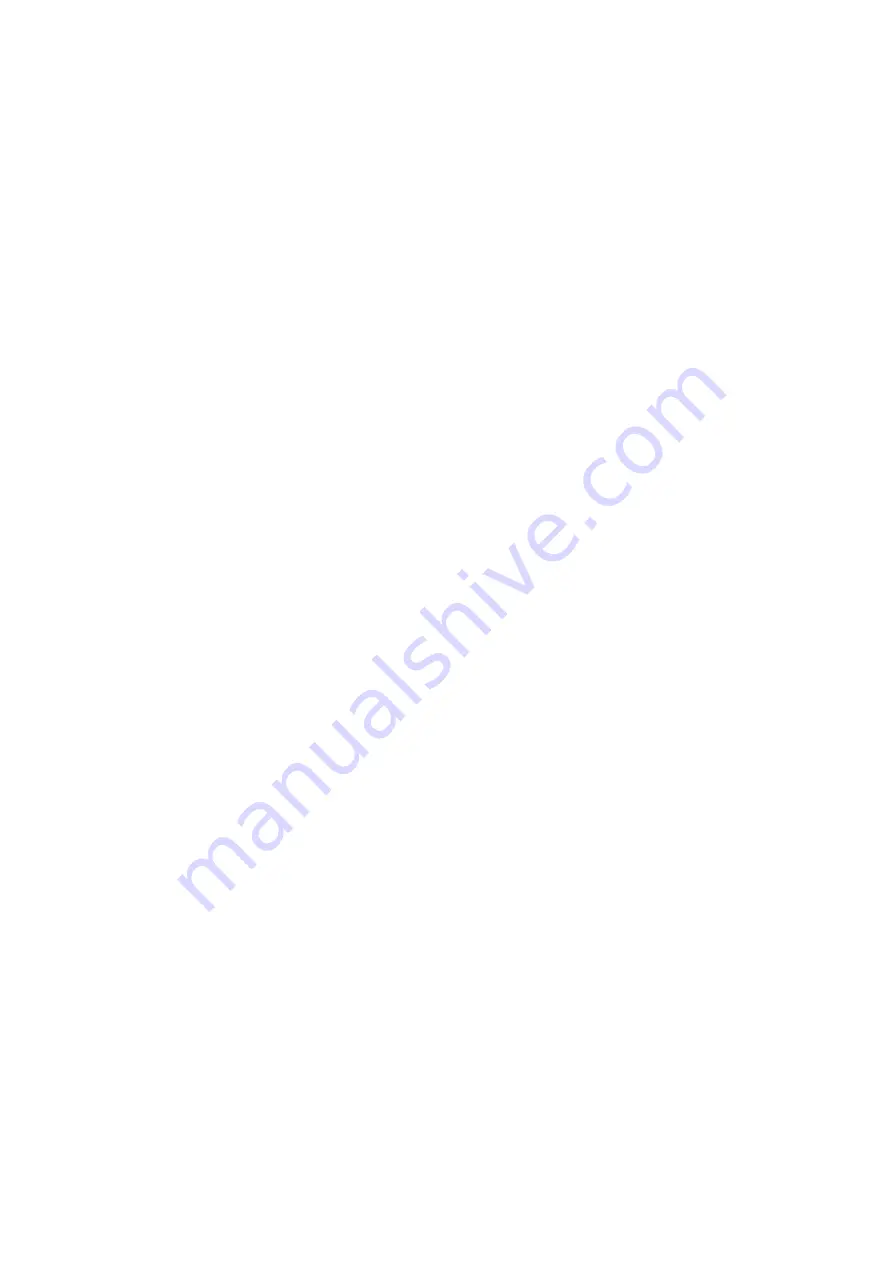
18
RC155 Components
1. Hopper, where you feed material into roller
2. Control rod, by which you control feeding, stopping, rejecting material
3. Roller, which is rolling by hydraulic to pull material in to drum housing
4. Housing cover, where you can open and check or change blade
5. Output chute, which can be turned 360 degrees for chips collecting
6. Deflector, which you can adjust throwing angle
7. Engine, which supplies power to drum and hydraulic system
8. Tow coupler, which use for connection for towing
9. Jacky wheel, which is used for support while machine is not connected to
truck.
10. Belt cover, which is used to cover belt and pulleys
11. Torsion axle, which is used to reduce bumping while transporting
12. Tire, This tubeless tire which is wear-resistant and explosion proof.
13. Serial plate, which contains product info and serial number
Summary of Contents for RATEL RC180 D
Page 46: ...45...