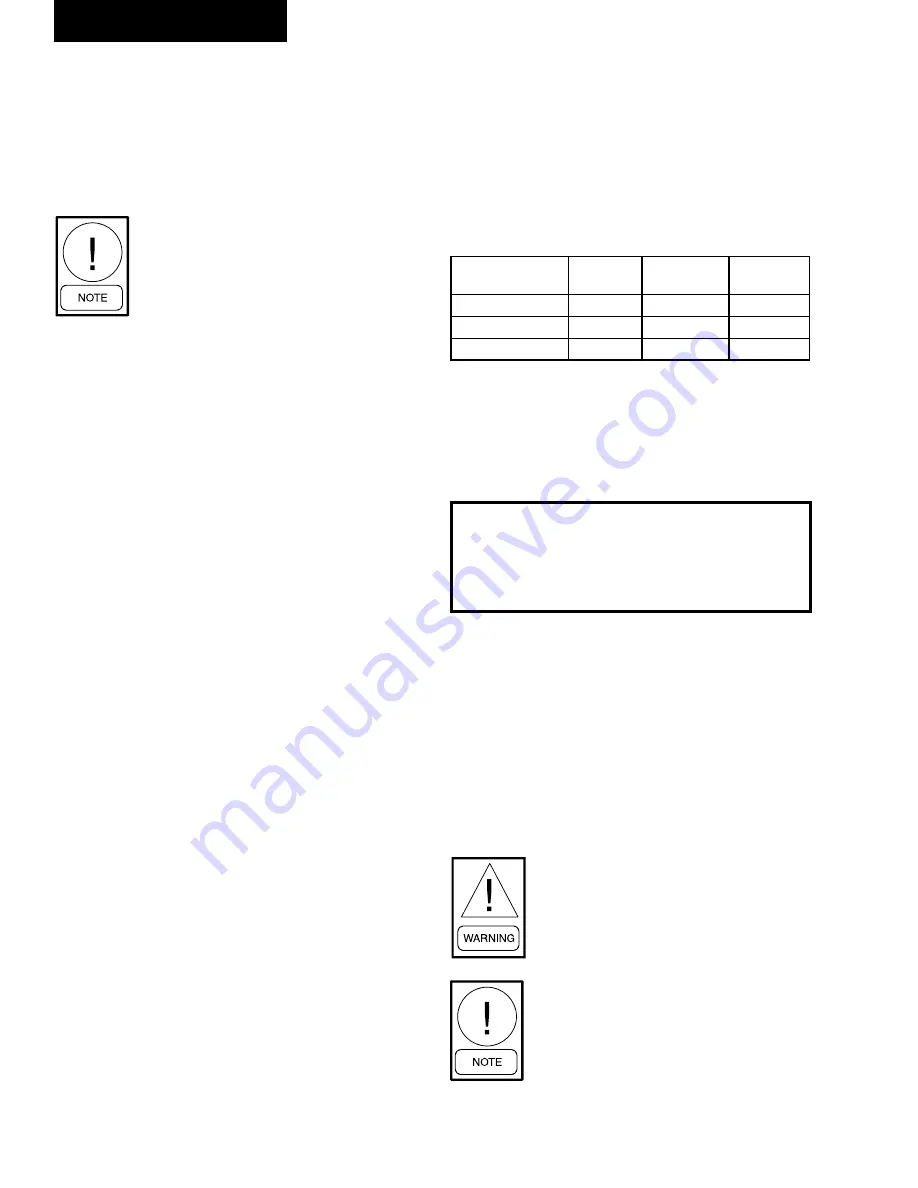
JOHNSON CONTROLS
FORM 160.75-O1 (309)
34
section 7
preVentiVe maintenance
It is the responsibility of the owner to provide the nec-
essary daily, monthly and yearly maintenance require-
ments of the system.
IMPoRtANt – If a unit failure occurs
due to improper maintenance during the
warranty period; Johnson Controls will
not be liable for costs incurred to return
the system to satisfactory operation.
In any operating system it is most important to provide
a planned maintenance and inspection of its functioning
parts to keep it operating at its peak efficiency. Therefore,
the following maintenance should be performed when
prescribed.
compressor
1.
Oil Filter
– When oil pump VSD frequency increases
to 55 hz to maintain target oil pressure.
When the oil filter is changed, it should be inspected
thoroughly for any aluminum particles which would
indicate possible bearing wear. If aluminum particles
are found this should be brought to the attention of
the nearest Johnson Controls office for their further
investigation and recommendations.
2.
Oil Changing
– The oil in the compressor must be
changed annually or earlier if it becomes dark or
cloudy. However, quarterly oil analysis can eliminate
the need for an annual change provided the analysis
indicates there is no problem with the oil.
compressor motor
1. Check motor mounting screws frequently to insure
tightness.
2. Meg motor windings annually to check for dete-
rioration of windings.
greased Bearings
Motor Operation and Maintenance manuals are supplied
with the chillers providing maintenance schedules and
instructions for the specific motors. The following are
lubrication schedules for the most common motors:
ram motor lubrication
Frame 143T thru 256T are furnished with double sealed
ball bearings, pre-lubricated prior to installation. Grease
fittings are not supplied and bearings are designed for
long life under standard conditions.
Frames 284T thru 587UZ are furnished with double
shielded or open ball or roller bearings. It is necessary
to re-lubricate anti-friction bearings periodically.
(See Table 4)
frame
size
standard
8hr/day
continuous
24hr day
grease
qty. oz.
143T-256T
*7 Years
*3 Years
*1
284TS - 286TS
210 Days
70 Days
1
324TS - 587uSS 150 Days
50 Days
2
* - On frame sizes 143T - 256T, changing bearings at these intervals
is recommended. However, removing the seal, cleaning and refilling
the bearing and the cavity with recommended grease can re-lubricate
these bearings.
Recommended greases for standard applications:
operating amBient temp. -30ºc to 50ºc
Chevron SRI
(Chevron)
Exxon unirex #2
(Exxon Corp.)
Exxon Polyrex
(Exxon Corp.)
Shell Dolum R
(Shell Oil Co.)
Westinghouse Motor Lubrication:
• Re-greasing should occur at 1000 operating hour
intervals.
• Westinghouse recommends using Westinghouse
Grease No. 53701.
• Motors with shaft diameters less than 2 3/8 inch
require 1 oz of grease per bearing while motors with
shaft diameters between 2 3/8 and 3 inches require
1.5 oz.
Mixing different greases is not
recommended
Additional information on motor lubri-
cation and other service issues can be
found in the A-C Motors Instruction
Manual.
preventive maintenance
taBle 4 –
BEARINg LuBRICATION
Summary of Contents for York MaxE YK Series
Page 2: ...Page 2 of 2 ...
Page 3: ......
Page 4: ......
Page 5: ......
Page 6: ......
Page 7: ......
Page 8: ......
Page 9: ......
Page 10: ......
Page 11: ......
Page 12: ......
Page 13: ......
Page 14: ......
Page 15: ......
Page 16: ......
Page 17: ......
Page 18: ......
Page 19: ......
Page 20: ......
Page 21: ......
Page 22: ......
Page 23: ......
Page 24: ......
Page 25: ......
Page 26: ......
Page 27: ......
Page 28: ......
Page 29: ......
Page 30: ......
Page 31: ......
Page 32: ......
Page 33: ......
Page 34: ......
Page 35: ......
Page 36: ......
Page 37: ......
Page 38: ......
Page 39: ......
Page 40: ......
Page 41: ......
Page 42: ......
Page 43: ......
Page 44: ......
Page 45: ......
Page 46: ......
Page 47: ......
Page 48: ......
Page 49: ......
Page 50: ......
Page 51: ......
Page 52: ......
Page 53: ......
Page 54: ......
Page 55: ......
Page 56: ......
Page 57: ......
Page 58: ......
Page 59: ......
Page 60: ......
Page 61: ......
Page 62: ......
Page 63: ......
Page 135: ...JOHNSON CONTROLS FORM 160 75 O1 309 36 SI metric conversion ...
Page 137: ...JOHNSON CONTROLS FORM 160 75 O1 309 38 NOTES ...
Page 138: ...FORM 160 75 O1 309 39 JOHNSON CONTROLS NOTES ...