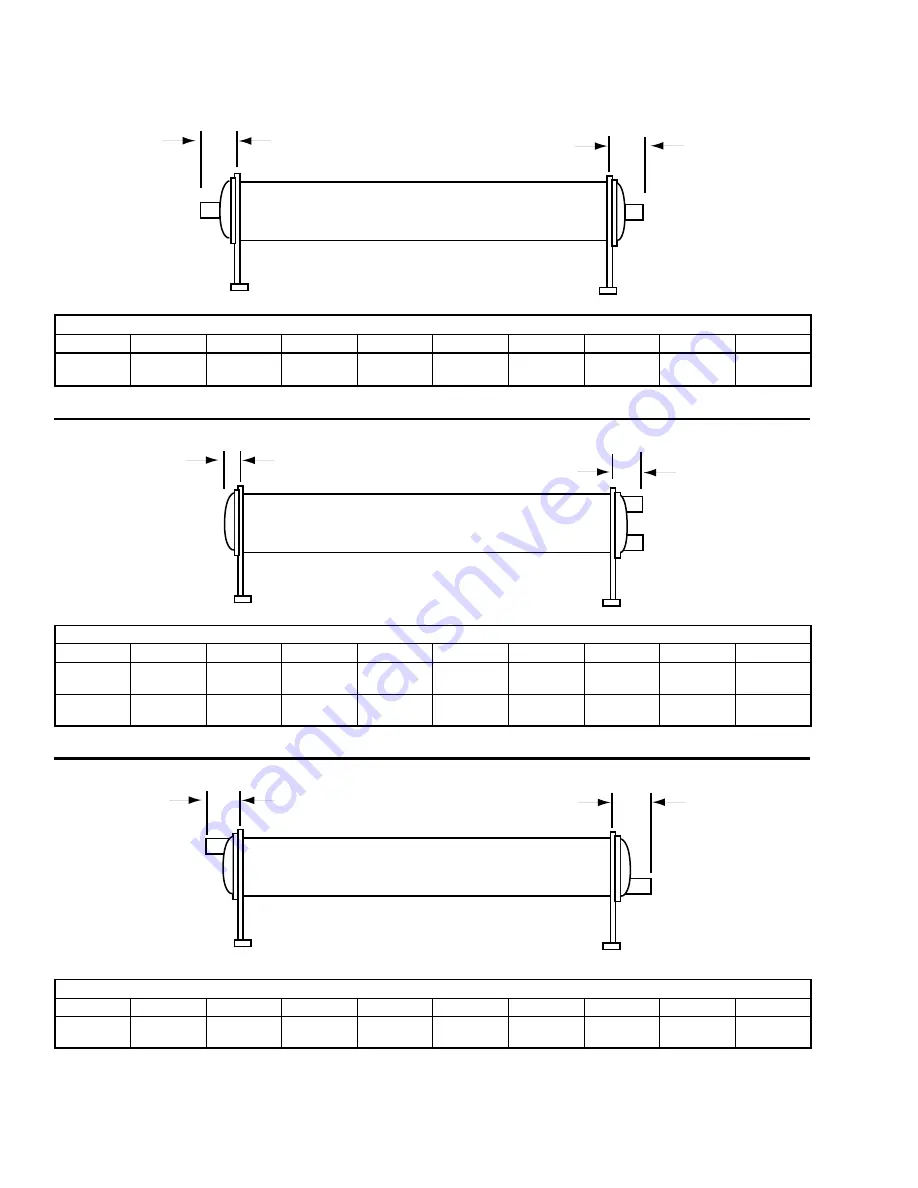
JohNSoN CoNtroLS
12
ForM 160.75-N1 (309)
fig. 8 –
DIMENSIoNS – EVAPorAtor CoMPACt WAtErBoXES
EVaPorator coMPact WatErBoxEs - ft - in (mm)
F
F
F
F
F
G
ONE PASS EVAPORATORS, CODES
DIM.
A
C,D
E,F
G,H
J,K,L
M,N
P,Q
R,S,W
X,Z
F
1'-2 1/4"
(362)
1'-3"
(381)
1'-3 1/2"
(394)
1'-3 3/4"
(400)
1'-5 1/2"
(445)
1'-11 5/8"
(600)
1'-11 5/8"
(600)
2'-0 5/8"
(625)
2'-1 3/4"
(654)
TWO PASS EVAPORATORS, CODES
DIM.
A
C,D
E,F
G,H
J,K,L
M,N
P,Q
R,S,W
X,Z
F
1'-2 1/4"
(362)
1'-3"
(381)
1'-3 1/2"
(394)
1'-3 3/4"
(400)
1'-5 1/2"
(445)
1'-11 5/8"
(600)
1'-11 5/8"
(600)
2'-0 5/8"
(625)
2'-1 3/4"
(654)
G
0'-6 1/2"
(165)
0'-7"
(178)
0'-7 1/2"
(191)
0'-7 3/4"
(197)
0'-9 1/2"
(241)
1'-3 5/8"
(397)
1'-3 5/8"
(397)
1'-4 3/4"
(425)
1'-5 3/4"
(451)
THREE PASS EVAPORATORS, CODES
DIM.
A
C,D
E,F
G,H
J,K,L
M,N
P,Q
R,S,W
X,Z
F
1'-2 1/4"
(362)
1'-3"
(381)
1'-3 1/2"
(394)
1'-3 3/4"
(400)
1'-5 1/2"
(445)
1'-11 5/8"
(600)
1'-11 5/8"
(600)
2'-0 5/8"
(625)
2'-1 3/4"
(654)
LD07619
see notes on page 14.
Summary of Contents for York MaxE YK Series
Page 2: ...Page 2 of 2 ...
Page 3: ......
Page 4: ......
Page 5: ......
Page 6: ......
Page 7: ......
Page 8: ......
Page 9: ......
Page 10: ......
Page 11: ......
Page 12: ......
Page 13: ......
Page 14: ......
Page 15: ......
Page 16: ......
Page 17: ......
Page 18: ......
Page 19: ......
Page 20: ......
Page 21: ......
Page 22: ......
Page 23: ......
Page 24: ......
Page 25: ......
Page 26: ......
Page 27: ......
Page 28: ......
Page 29: ......
Page 30: ......
Page 31: ......
Page 32: ......
Page 33: ......
Page 34: ......
Page 35: ......
Page 36: ......
Page 37: ......
Page 38: ......
Page 39: ......
Page 40: ......
Page 41: ......
Page 42: ......
Page 43: ......
Page 44: ......
Page 45: ......
Page 46: ......
Page 47: ......
Page 48: ......
Page 49: ......
Page 50: ......
Page 51: ......
Page 52: ......
Page 53: ......
Page 54: ......
Page 55: ......
Page 56: ......
Page 57: ......
Page 58: ......
Page 59: ......
Page 60: ......
Page 61: ......
Page 62: ......
Page 63: ......
Page 135: ...JOHNSON CONTROLS FORM 160 75 O1 309 36 SI metric conversion ...
Page 137: ...JOHNSON CONTROLS FORM 160 75 O1 309 38 NOTES ...
Page 138: ...FORM 160 75 O1 309 39 JOHNSON CONTROLS NOTES ...