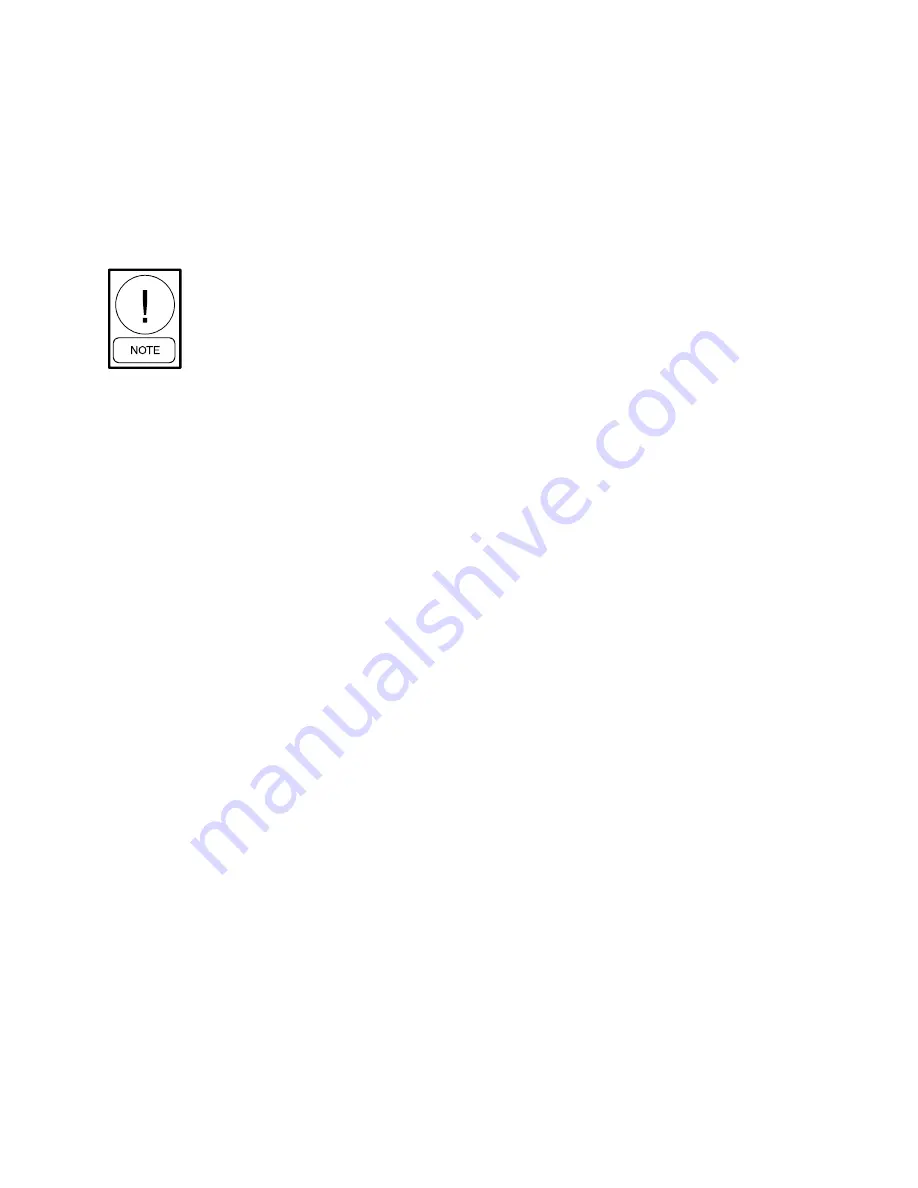
ForM 160.75-N1 (309)
31
JohNSoN CoNtroLS
installation
rigging unit to final location
Rig the unit to its final location on the floor or mounting
pad, lift the unit (or shell assembly) by means of an
overhead lift and lower the unit to its mounting position.
(If optional shipping skids are used, remove them before
lowering the chiller to its mounting position.)
At this point units shipped dismantled
should be assembled under the super
-
vision of a Johnson Controls repre
-
sentative.
If evaporator is to be field insulated, the insulation should
be applied to the evaporator before the unit is placed in
position while the unit is in the lift position. be sure unit
is properly supported. (See INSULATION, page 35)
locating and installing isolator Pads
(rEfEr to fig. 19)
The isolator pad mounts are to be located as shown in
FIG. 19 ( Rubber side down).
After the isolator pads have been placed into position on
the floor, lower the chiller onto the pads. When the unit
is in place, remove the rigging equipment and check that
the unit is level. The unit should be level within 1/4"
(6 mm) from one end to the other end and from front
to the rear. If the chiller is not level within the amount
specified, lift it and place shims between the isolation
pad and the chiller tube sheets. (Shims furnished by
the installer.) Lower unit again and recheck to see that
it is level.
chEcKing thE isolation Pad dEflEction
All isolation pads should be checked for the proper
deflection while checking to see if the unit is level. Each
pad should be deflected approximately 0.10 inches (2.5
mm) to 0.20 inches (5 mm). If an isolation pad is under-
deflected, shims should be placed between the unit tube
sheet and the top of the pad to equally deflect all pads.
lEVEling thE unit
The longitudinal alignment of the unit should be checked
by placing a level on the top center of the evaporator
shell under the compressor/motor assembly. Transverse
alignment should be checked by placing a level on top
of the shell end sheets.
installing oPtional sPring isolators
(rEfEr to fig. 21)
When ordered, spring type isolator assemblies will be
furnished with the unit. The 4 assemblies are identical
and can be placed at any of the 4 corners of the unit.
While the unit is still suspended by the rigging, the
isolators should be bolted to the unit by inserting the
cap screw(s) through the hole(s) in the mounting bracket
into the tapped hole in the top of the isolator leveling
bolt(s). Then the unit can be lowered onto the floor.
The leveling bolts should now be rotated one (1) turn at
a time, in sequence, until the unit end sheets are clear
of the floor by the dimension shown in
FIG. 20 or 22
and the unit is level. Check that the unit is level, both
longitudinally and transversely (see Leveling the Unit).
If the leveling bolts are not long enough to level unit
due to an uneven or sloping floor or foundation, steel
shims (grouted, if necessary) must be added beneath the
isolator assemblies as necessary.
After the unit is leveled, wedge and shim under each
corner to solidly support the unit in this position while
piping connections are being made, pipe hangers adjusted
and connections checked for alignment. Then the unit is
filled with water and checked for leaks. The leveling bolts
should now be finally adjusted until the wedges and shims
can be removed. The unit should now be in correct level
position, clear of the floor or foundation and without any
effect from the weight of the piping.
PiPing connEctions
After the unit is leveled (and wedged in place for optional
spring isolators) the piping connections may be made;
chilled water, condenser water and refrigerant relief. The
piping should be arranged with offsets for flexibility, and
adequately supported and braced independently of the
unit to avoid strain on the unit and vibration transmission.
Hangers must allow for alignment of pipe. Isolators (by
others) in the piping and hangers are highly desirable,
and may be required by specifications, in order to
effectively utilize the vibration isolation characteristics
of the vibration isolation mounts of the unit.
Check for piping alignment –
Upon completion of
piping, a connection in each line as close to the unit as
possible should be opened, by removing the flange bolts
or coupling and checked for piping alignment. If any of
the bolts are bound in their holes, or if the connection
Summary of Contents for York MaxE YK Series
Page 2: ...Page 2 of 2 ...
Page 3: ......
Page 4: ......
Page 5: ......
Page 6: ......
Page 7: ......
Page 8: ......
Page 9: ......
Page 10: ......
Page 11: ......
Page 12: ......
Page 13: ......
Page 14: ......
Page 15: ......
Page 16: ......
Page 17: ......
Page 18: ......
Page 19: ......
Page 20: ......
Page 21: ......
Page 22: ......
Page 23: ......
Page 24: ......
Page 25: ......
Page 26: ......
Page 27: ......
Page 28: ......
Page 29: ......
Page 30: ......
Page 31: ......
Page 32: ......
Page 33: ......
Page 34: ......
Page 35: ......
Page 36: ......
Page 37: ......
Page 38: ......
Page 39: ......
Page 40: ......
Page 41: ......
Page 42: ......
Page 43: ......
Page 44: ......
Page 45: ......
Page 46: ......
Page 47: ......
Page 48: ......
Page 49: ......
Page 50: ......
Page 51: ......
Page 52: ......
Page 53: ......
Page 54: ......
Page 55: ......
Page 56: ......
Page 57: ......
Page 58: ......
Page 59: ......
Page 60: ......
Page 61: ......
Page 62: ......
Page 63: ......
Page 135: ...JOHNSON CONTROLS FORM 160 75 O1 309 36 SI metric conversion ...
Page 137: ...JOHNSON CONTROLS FORM 160 75 O1 309 38 NOTES ...
Page 138: ...FORM 160 75 O1 309 39 JOHNSON CONTROLS NOTES ...