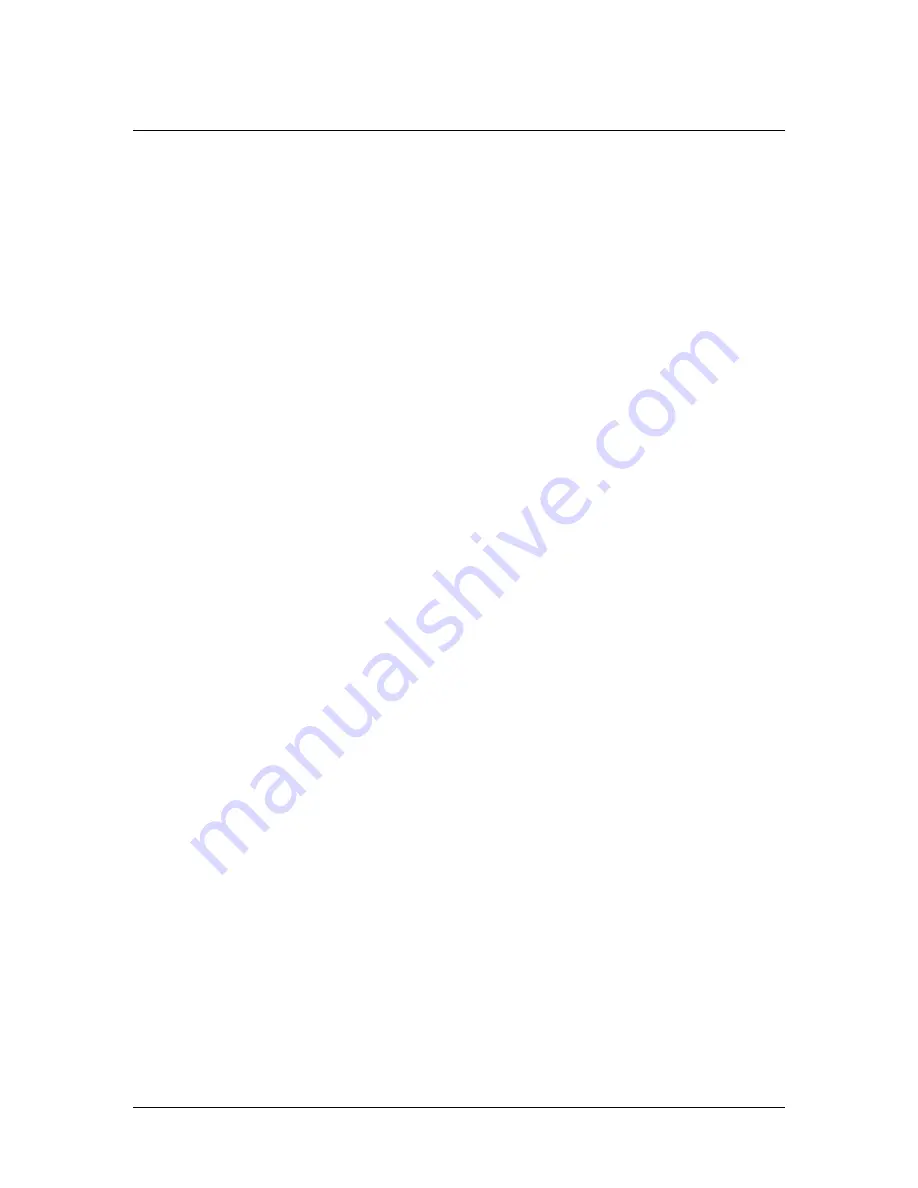
Chapter 3. Installation
STERRAD
®
100S Installation Guide
26
WARNING! USE A PARTNER. FOR SAFETY
PURPOSES, THIS STEP REQUIRES THE
PRESENCE OF AT LEAST TWO PEOPLE
CAPABLE OF HANDLING 100 LBS.
13. With one person pushing carefully at the back of the system and one
person guiding the system at the front, ease the system forward and
guide it down the ramp until all four wheels are on the floor.
14. Verify that no air pressure is present in the pneumatics.
15. Remove the blanking flange from the bottom of the chamber. This
removes any vacuum that may be present.
16. Remove the four 4 mm hex bolts securing the door in the closed
position.
17. Remove the two 6 mm hex bolts securing the counterweight.
Note: The screws are behind neoprene and fit
through the chamber flange into the door.
18. Manually open the door by pushing down on the top of the door. The
door should open with ease. Remove the boxes from inside the
system.
Note: The boxes shipped with the system contain
vacuum system parts and other system
accessories. Be sure to unpack the boxes
completely before discarding.
19. If you are going to move the unit to a different site, replace the side
and lower back panels.
20. Once the unit is in position in the installation site, remove all exterior
panels and temporarily store them in a safe location.
Summary of Contents for ASP STERRAD 100S
Page 1: ...STERRAD 100S Sterilizer Installation Guide ...
Page 5: ...STERRAD 100S Installation Guide 5 Chapter 1 Installation Overview ...
Page 14: ......
Page 15: ...STERRAD 100S Installation Guide 15 Chapter 2 For Your Safety ...
Page 20: ......
Page 21: ...STERRAD 100S Installation Guide 21 Chapter 3 Installation ...
Page 23: ...Chapter 3 Installation STERRAD 100S Installation Guide 23 Figure 1 Installation Diagram ...