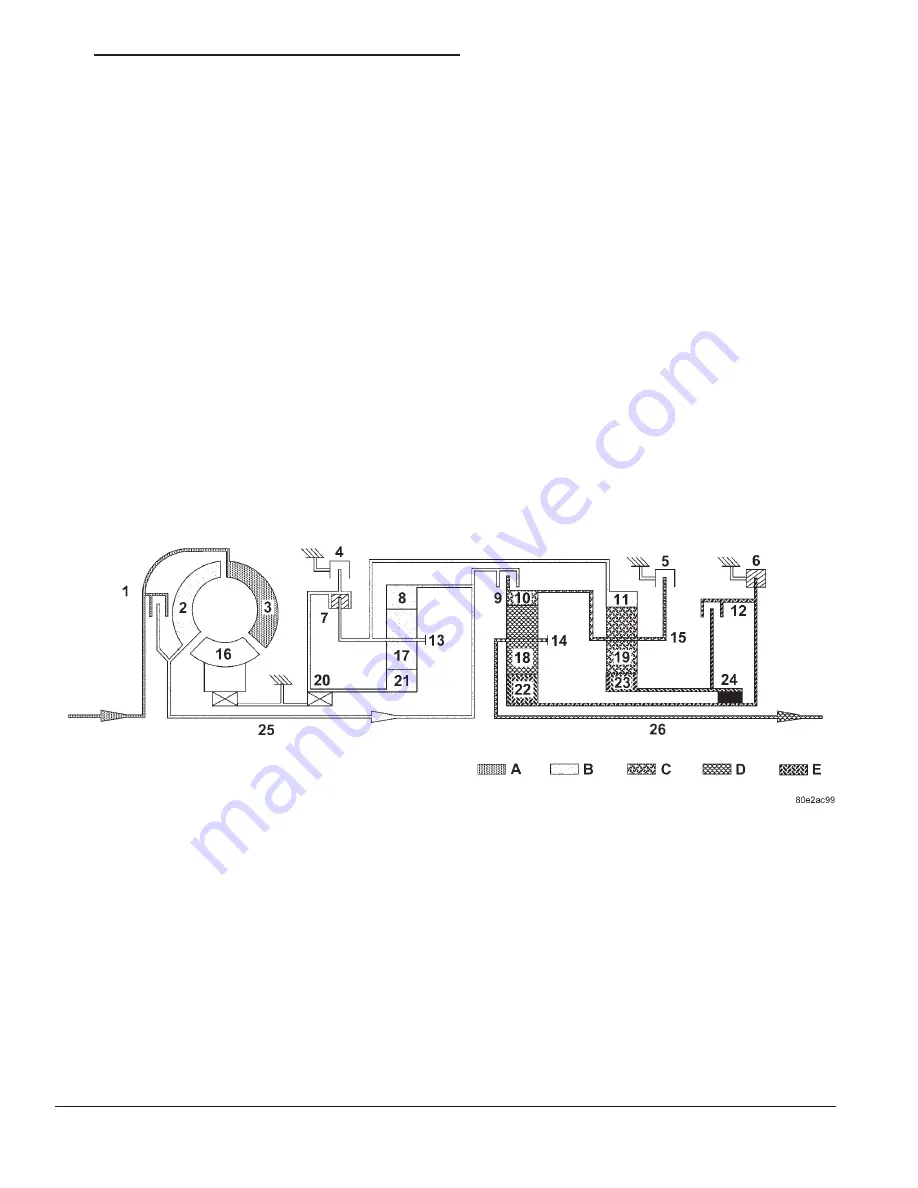
Center Planetary Gear Set
The annulus gear (10) is driven at the same speed
as the rear planetary carrier (15) as a result of a
mechanical connection. The sun gear (22) is held
against the housing by the multiple-disc holding
clutch B2 (6). The planetary pinion gears (18) turn
on the fixed sun gear (22) and increase the torque
from the annulus gear (10) to the planetary carrier
(14). The output shaft (5) connected to the planetary
carrier (14) turns at a reduced speed in the running
direction of the engine.
Fig. 4 Second Gear Powerflow
1 - TORQUE CONVERTER LOCK-UP CLUTCH
14 - CENTER PLANETARY CARRIER
2 - TORQUE CONVERTER TURBINE
15 - REAR PLANETARY CARRIER
3 - TORQUE CONVERTER IMPELLER
16 - TORQUE CONVERTER STATOR
4 - HOLDING CLUTCH B1
17 - FRONT PLANETARY PINION GEARS
5 - HOLDING CLUTCH B3
18 - CENTER PLANETARY PINION GEARS
6 - HOLDING CLUTCH B2
19 - REAR PLANETARY PINION GEARS
7 - DRIVING CLUTCH K1
20 - FREEWHEELING CLUTCH F1
8 - FRONT PLANETARY ANNULUS GEAR
21 - FRONT PLANETARY SUN GEAR
9 - DRIVING CLUTCH K2
22 - CENTER PLANETARY SUN GEAR
10 - CENTER PLANETARY ANNULUS GEAR
23 - REAR PLANETARY SUN GEAR
11 - REAR PLANETARY ANNULUS GEAR
24 - FREEWHEELING CLUTCH F2
12 - DRIVING CLUTCH K3
25 - DRIVE SHAFT
13 - FRONT PLANETARY CARRIER
26 - OUTPUT SHAFT
A - ENGINE SPEED
D - SECOND GEAR RATIO
B - TRANSMISSION INPUT SPEED
E - FIXED PARTS
C - FIRST GEAR RATIO
WG
TRANSMISSION AND TRANSFER CASE
21a - 7
AUTOMATIC TRANSMISSION - W5J400 (Continued)