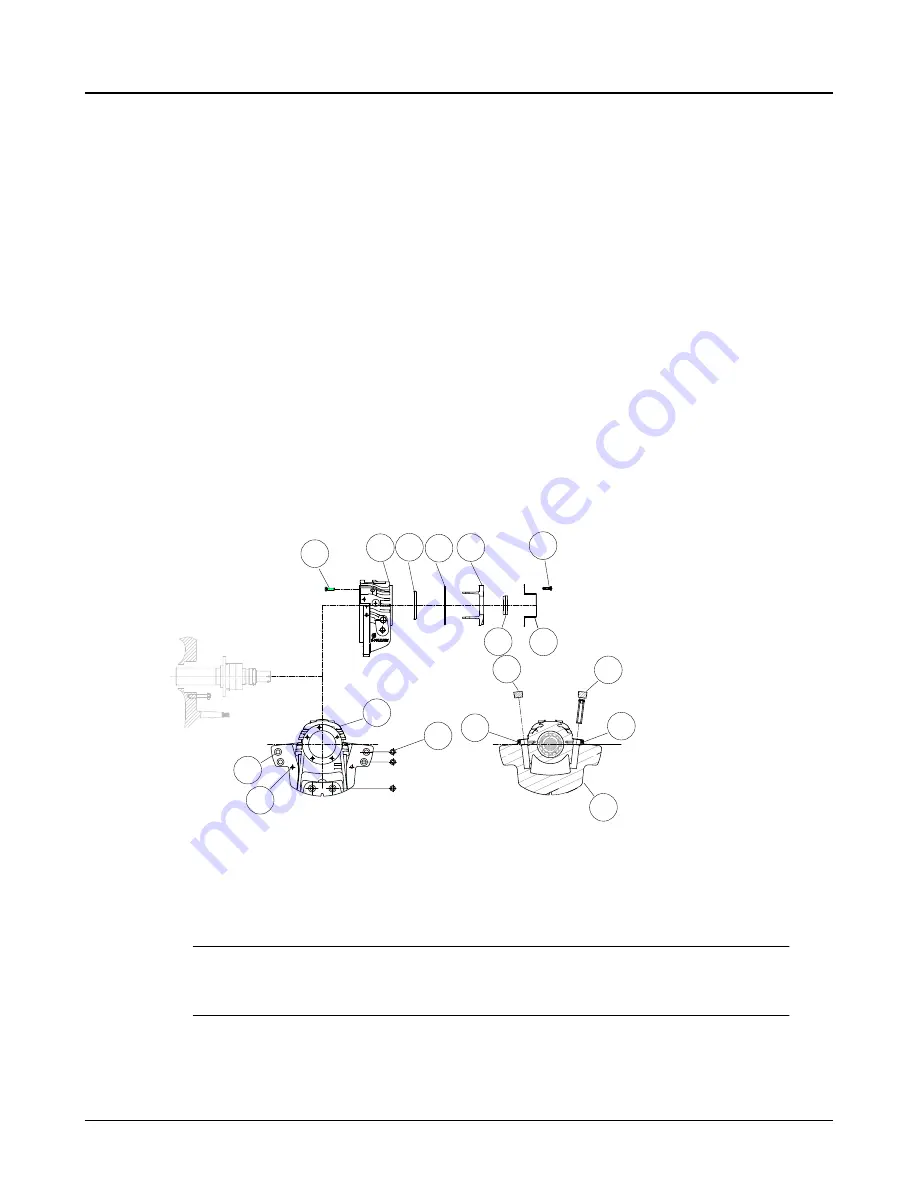
c)
While the bearings are hot, tighten the locknut by hand with a spanner wrench until the bearing
is snug against the shaft shoulder.
d) Allow the bearing assembly to cool slowly to room temperature.
Do not rapidly cool the bearings with compressed air or other means.
e) When the bearing assembly is fully cooled, remove the locknut, install the lockwasher (382),
and install the locknut.
f)
Hand-tighten the locknut with a spanner wrench. Do not over-tighten the bearing. Tap the end
of the spanner wrench with light strikes from a dead blow hammer while you note the location
of the next available lockwasher tab that aligns with the slots in the locknut.
The turning resistance of the nut increases as it tightens. Plan the alignment of the lockwasher tab
with the locknut fully tightened. If the locknut is still turning with light strikes with the hammer, then
continue to tighten the locknut until the next available tab is aligned with a slot. Do not use heavy
strikes with the hammer. If it is not possible to reach the next tab, then loosen the locknut to align
with the previous tab.
g) Check the condition of the outer races by rotating the bearings by hand in opposite directions:
• The outer races generally cannot be counter-rotated by hand, but if they do move, the resist-
ance must be high.
• If the outer races are loose, the bearing is not properly seated and must be retightened.
h) When you have achieved the proper bearing assembly, set the lockwasher tab in the slot in the
locknut.
371D
134 114A 360A 109A
371C
785C
332C
550A
113Q
113R
113R
134
427J
134
469J
371T
Figure 79: Thrust bearing housing assembly
5.
Install the bearing housing (134) over the bearings. Finger-tighten the nuts (427J) on the studs
(371T). Insert the dowel pins (469J); then tighten the nuts (427J).
The bearing housing is doweled to the casing (100) during the original build to assure the correct
running position of the shaft.
NOTICE:
The bearing housing flange must fit metal-to-metal (no gap) to the bearing saddle flange.
6.
Tighten the inboard end-cover capscrews .
7.
Install the oil ring (114).
8.
Assemble the outboard labyrinth seal (332C) into the outboard thrust end cover (109A):
a) Clean the end cover with a solvent.
6.6 Reassembly
108 Model 3600 i-FRAME API610 11th Edition / ISO 13709 2nd Edition to current API BB3 Multi-Stage, Axially Split Installa-
tion, Operation, and Maintenance Manual
Summary of Contents for GOULDS PUMPS 3600 i-FRAME
Page 2: ......