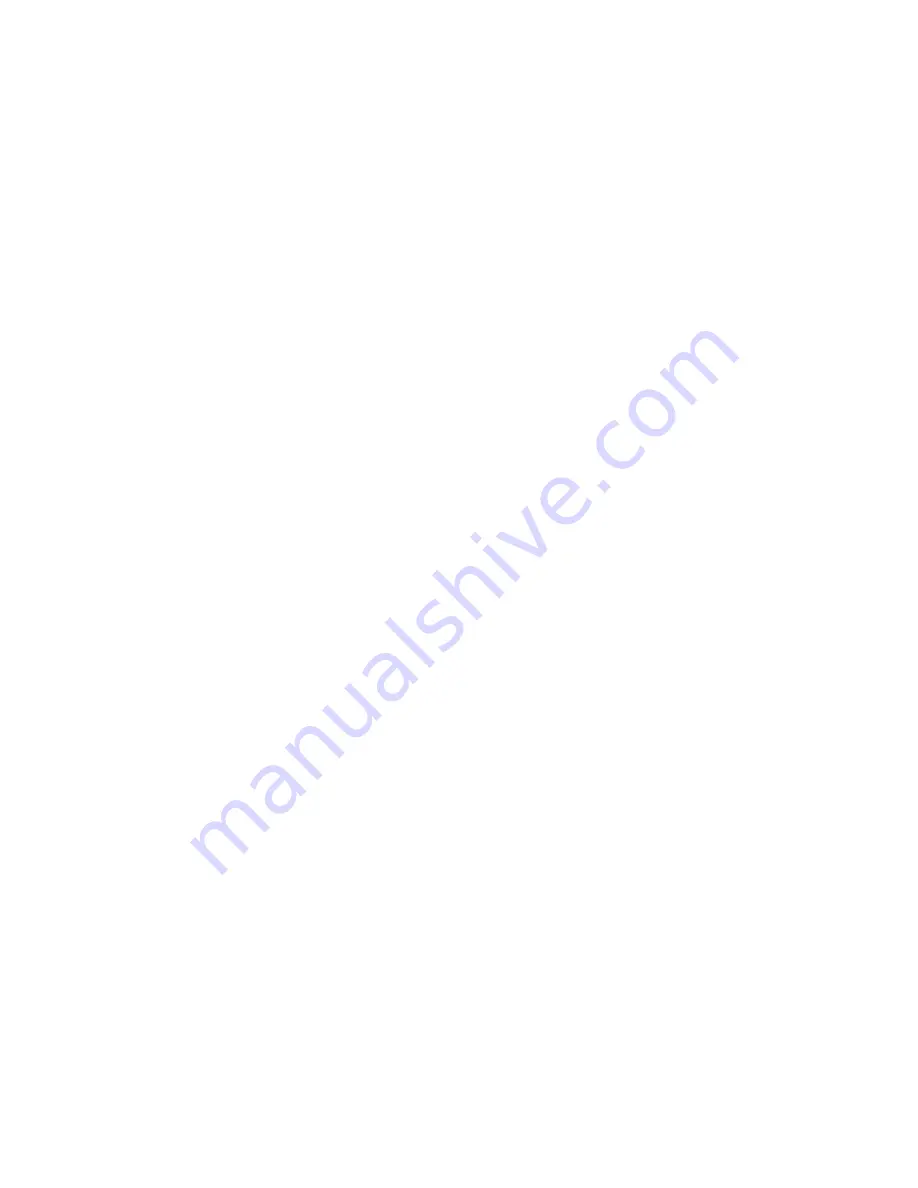
TJ75
14
TO HANDLE BOOSTER CABLES
When using booster cables, pay attention to the
following items for safe operation:
(1) Before connecting cables, remove the vent plugs.
This will lower the force in case of explosion.
(2) Before connecting cables, be sure to stop the engine.
Otherwise unexpected accidents may occur.
(3) Use booster cables with sufficient electrical capacity.
A cable of inadequate capacity will cause generation
of heat, which may lead to a fire.
SAFETY DECALS
The labels are stuck on the tractor. You should of course
read the safety instructions in the manual. But never fail
to read the labels on the machine as well.
・
The labels should always be clearly seen, that is,
nothing should obscure them.
・
When they have become dirty, wash them with
soap water and wipe off with soft cloth.
・
If any of them are torn or lost, order new labels
from your dealer. Their codes are mentioned in
SAFETY DECALS AND THEIR LOCATION.
・
A new label should be placed in the same place
where the old one was located.
・
When sticking on a new label, clean the place to
enable the label to stick and squeeze out all air
bubbles trapped under it.
Summary of Contents for TJ75
Page 1: ...TJ75 MODEL I S E K I T R A C T O R S ...
Page 65: ...TJ75 64 POWER OUTLET SUPPLY ...
Page 114: ...WIRING HARNESS CABLE 113 WIRING HARNESS CABLE WIRING HARNESS MAIN ...
Page 115: ...WIRING HARNESS CABLE 115 WIRING HARNESS ELC ...
Page 116: ...WIRING HARNESS CABLE 117 WIRING HARNESS CAB ...