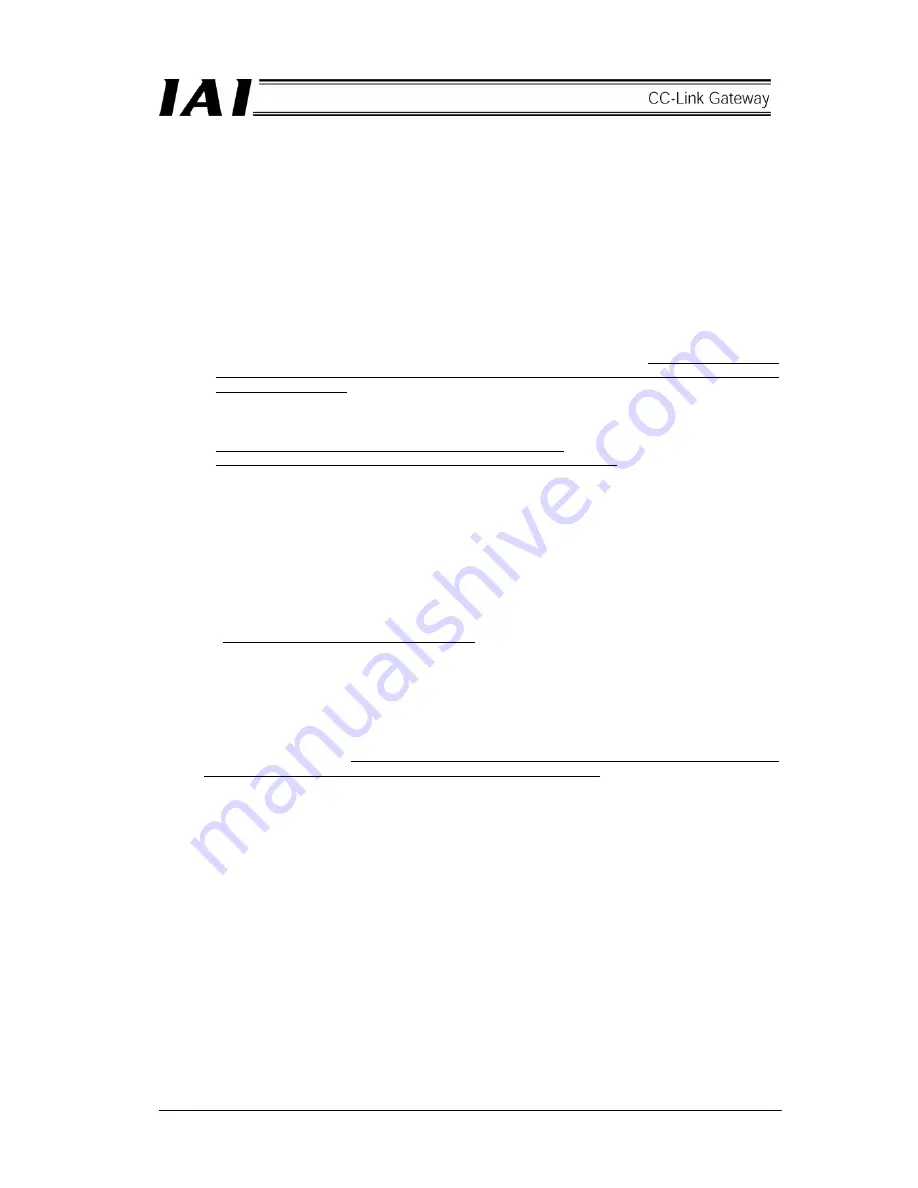
81
(6) Positioning data designated mode push operation
(Position data, acceleration and deceleration data, speed data, current limit value,
positioning width, present position data, DIR, PUSH, CSTR, PEND, MOVE)
This is a function to operate to push the actuator by directly writing position data, acceleration and
deceleration data, speed data, current limit value and positioning width onto the link register on the PLC
without using the position table for the controller.
This is an effective function when push operation mode (maximum number of controlled axes, 3 axes) is
selected in positioning data designated mode.
■
Function
[1] Set push a start position data to the position data designated register.
[2] Set a speed up to the push start position to the speed designated register, and set the acceleration
and deceleration at the time to the acceleration and deceleration register. Note that setting of the
parameter No.9 “Acceleration and deceleration initial value” is not applied unless the acceleration
and deceleration is set.
[3] Set a push operation moving amount (maximum push amount) to the positioning width designated
register. (*)
[4] Set a current limit value for setting push force to the current limit value register.
[5] Turn ON the PUSH (push operation mode designation) signal.
[6] Select a push direction with the DIR (push direction designation) signal.
Push operation is performed in home return reverse direction with the DIR signal ON, and in home
return direction with the DIR signal OFF.
[7] Turn ON the CSTR(start) after that (
≥
0)
Turn ON the CSTR in a status that the PEND (Positioning completed) or the MOVE (on-moving)
signal is OFF.
Data set in [1] to [4] is transmitted to the controller at the ON edge (at startup of signal).
[8] The PEND is turned OFF after the CSTR is turned ON, and after tdpf.
[9] Turn OFF the CSTR by turning OFF the PEND or turning ON the MOVE signal.
[10] The MOVE is turned ON at the same time when the PEND is turned OFF or within 1Mt after that.
[11] The PEND is turned ON when the CSTR is OFF and current from the motor reaches the current
limit value set in [4]. (Push completed)
The PSFL (push outside) signal is turned ON unless the current from the motor reaches the current
limit value set in [4] even if the positioning width set in [3] is reached.
In this case, the PEND is not turned ON. (Push outside)
[12] The present position data is always updated.
[13] Turn OFF the PUSH and DIR by turning ON the PEND or turning ON the PSFL.
◎
Normal positioning in push operation enable mode
Normal positioning in push operation enable mode is operated with the signal in [5] OFF. Setting in
[4] is also unnecessary. The PEND is turned ON when the CSTR is OFF and remaining movement
amount set in [3] enters a positioning width designated data range. The others are the same as
those in the “7.2(5) Direct numeric value designated operation.”
* Note that setting of the parameter No.10 “Positioning width initial value” unless the positioning width
designated data is set.
Summary of Contents for RCM-GW-CC
Page 1: ...IAI America Inc CC Link RCM GW CC Gateway Unit Operation ManualFirst Edition...
Page 4: ......
Page 10: ...6 1 5 How to identify model RCM GW CC Basic model For CC Link Gateway unit...
Page 12: ...8 2 2 External dimension drawing Mounting dimension...
Page 78: ...74...
Page 82: ...78 Position data measurement value Present position 1 2 3 4 4 5 6 7...
Page 84: ...80 Speed acceleration and deceleration set value Actuator speed Speed n2 Speed n3 1 2 3...
Page 88: ...84 Command position No Completion position No 1 2 3 4 5 6...
Page 91: ...87...
Page 93: ...89...
Page 125: ...121 No 3 Axis 1 pause No 3 Axis 1 pause lamp No 3 Axis 1 STP...
Page 130: ...126...
Page 131: ......