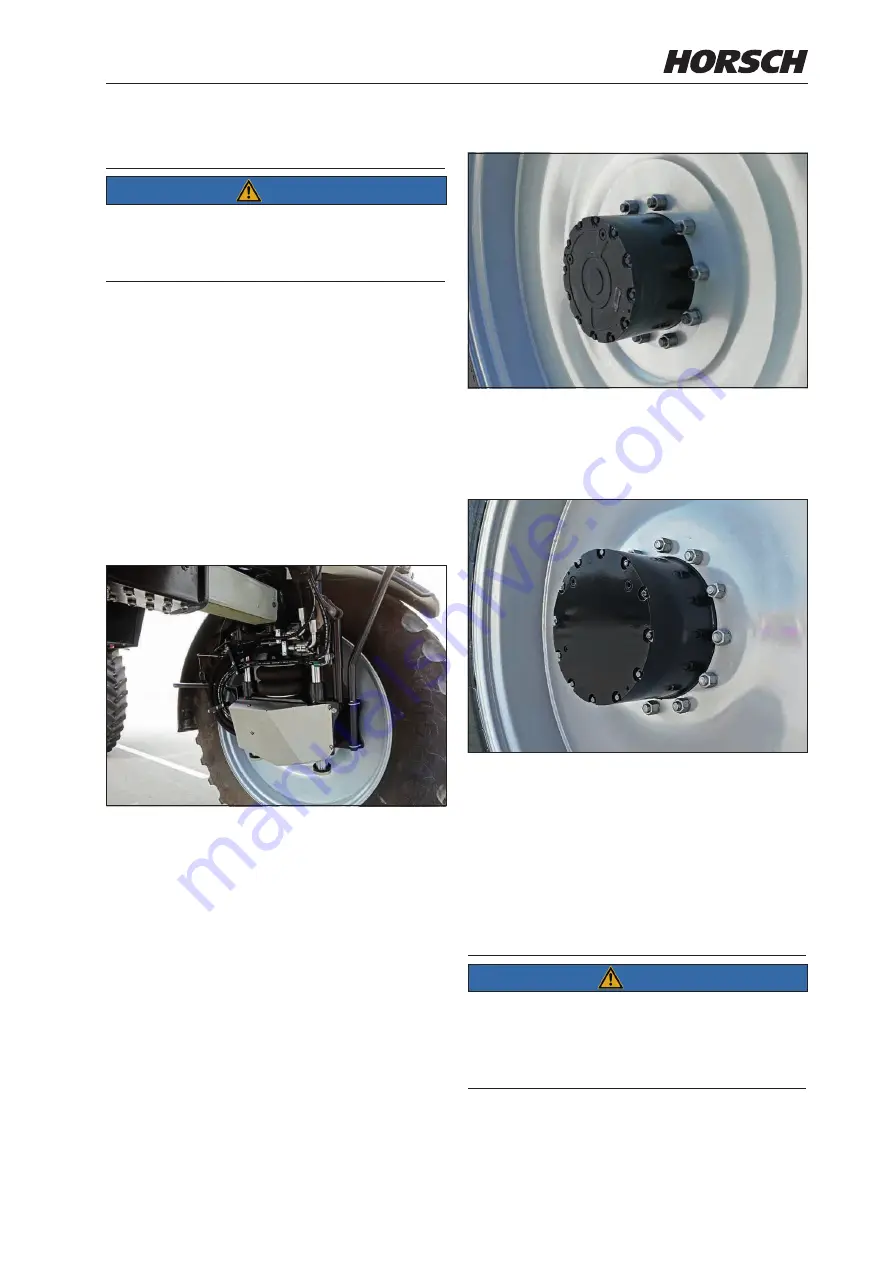
Axles
NOTE
All maintenance and repair works must solely be
carried out by expert personnel. Safety regula
-
tions must be strictly complied with!
The oil in the wheel gears must be changed at
regular intervals. Check for leaks on the gears.
Check the hoses for visible damages.
Remove all dirt from the steering knuckles once
every day. For this purpose turn steering once
completely to the left and the right.
Wheel drive
The wheel motor transmits its power to the wheel
via the wheel gear.
Two gear variants – PowerGear (GFT 8130) and
HighPowerGear (GFT 8144) – are available.
PowerGear (GFT 8130)
•
Small variant
•
10 wheel nuts
HighPowerGear (GFT 8144)
•
Large variant
•
12 wheel nuts
The correct amount of oil in the gears must be
ensured depending on the variant!
Oil change
NOTE
Change the oil of the wheel gears after the
first 100 hours and then after every 600 hours.
Refer also to the
Undercarriage maintenance over-
view
section.
70
71
Summary of Contents for Leeb 5.280 VL
Page 2: ......
Page 5: ......
Page 11: ...7...
Page 219: ...Diagram a with example 215...
Page 225: ...221...
Page 228: ...5 1 2 8 9 10 13 12 23 26 28 224...
Page 230: ...26 39 40 42 43 45 226...
Page 234: ...44 1 2 5 8 9 10 16 25 12 14 230...
Page 236: ...44 50 45 44 47 48 232...
Page 279: ...Central frame middle frame tractor link arm Parallelogram lock 275...
Page 307: ......