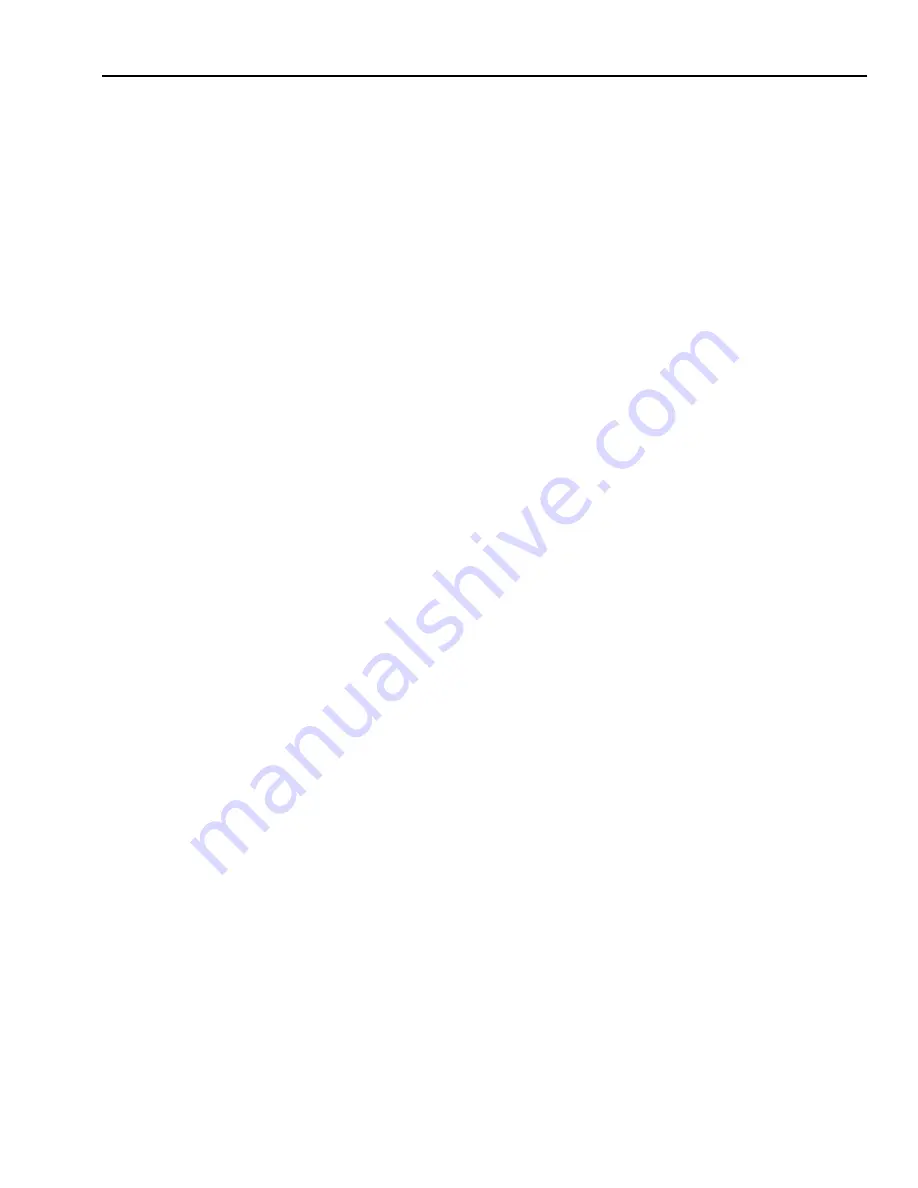
ENGINEERING MANUAL OF AUTOMATIC CONTROL
CHILLER, BOILER, AND DISTRIBUTION SYSTEM CONTROL APPLICATIONS
357
Each building is provided with a “choke” valve (V-1), and a
load reset loop to maintain water pressure within the building,
such that the most demanding AHU valve is always between
80 and 95 percent open. Each building requires a Valve V-1
Control Detail (inset) and a dynamic sequence description of
the program. Each control detail includes minimum and
maximum differential pressure setpoints, a software MANUAL
- AUTO selector, and a setpoint value for the manual position.
Ideally the control detail along with the current percent open
for each valve within the building is provided graphically for
each building.
NOTE: If the choke valve (V-1) is omitted on the most remote
building, the choke valves need not be considered for
pump sizing.
Pump speed is reset to keep the most demanding Building
Valve V-1 between 80 and 95 percent open.
Adjust balancing valves in buildings close to the pumping
plant with the choke valve in control, so that high balancing
valve differential pressures are not set to negate low load value
of the choke valve reset concept.
This concept can be combined with tertiary pumps in remote
buildings to control the building differential pressure and choke
valves in closer buildings utilizing central pumping.
Balancing Valve Considerations
BALANCING VALVE EFFECTS
Figure 80 assumes that all coils are equally loaded (1/3 flow),
and that all friction losses are 1/9th [(1/3)
2
] of their full load value.
In symmetrical loading and with valve position reset, the balancing
valves have no adverse effect. However, if at 25 L/s total flow,
AHU 1 and 2 are operating at full flow (12.5 L/s) and all others
are off, the required differential pressure across AHU 1 is 84 kPa,
36 kPa of which is wasted on the balancing valve.
BALANCING VALVE ELIMINATION
Elimination of all balancing valves allows the valve position
load reset control strategy to satisfy the non-symmetrical
loading described in BALANCING VALVE EFFECTS, by
producing only 48 kPa differential pressure at AHU 2 (slightly
higher at AHU 1) and save significant pumping energy during
most periods of non-symmetrical operation. Before eliminating
balancing valves consider:
1. Load coil temperature control setpoints must be strictly
maintained. In the example, lowering AHU 1 leaving air
temperature 2.5 kelvins below the design temperature
causes AHU 1 water flow loop to draw significantly more
than design flow because it is nearer the pump where the
differential pressure is higher. This will slightly starve
the other loads.
2. Cool-down periods for other than AHUs 1 and 2 will be
extended. With all valves full open, until AHUs 1 and 2
are satisfied, the other AHUs will be starved.
3. Industrial valves may be required to maintain acceptable
controllability. At properly controlled full load design
conditions, a 84 kPa differential pressure drop appears
across the AHU 1 control valve. This is the 48 kPa
differential pressure required at AHU 6 plus the 36 kPa
piping drop from AHU 1 to AHU 6. With the high
differential pressure, some piping configurations will
require an industrial valve.
Elimination of or fully open balancing valves might work
well in a continuously operating facility with operators who
understand disciplined setpoint and self-balancing concepts.
If eliminating balancing valves in a fixed setpoint scheme,
position the DP sensor across AHU 6, with a setpoint of 48 kPa.
If AHU 6 is very remote from the VSD pump controller, it is
recommended to put an additional differential pressure sensor at
the pump with a maximum set point of 108 kPa then reset the
setpoint down as required to prevent the AHU 6 differential
pressure from exceeding 48 kPa. Use of a DDC PID input and
output in separate controllers is not recommended because of the
communications system reliability.
If balancing valves are removed in a valve position load reset
scheme, use the single differential pressure sensor at the pump
with a maximum differential pressure setpoint of 108 kPa.
Differential Pressure Sensor Location Summary
Refer to Figure 79, in summary:
1. If valve position load reset is employed, the DP sensor may
be located in the pump room for simplicity (position DP-1)
2. If valve position load reset is not employed and balancing
valves are provided, the DP sensor should be located at
AHU-1 (position DP 2) and set for 84 kPa
3. If valve position load reset is not employed and balancing
valves are not provided, the DP sensor should be located
at AHU-6 (position DP 3) and set for 48 kPa.
4. If the sensor is located at AHU 6, resetting the setpoint
of a sensor located at position DP 1 is recommended as
noted in BALANCING VALVE CONSIDERATIONS.
Pump Minimum Flow Control
Pumps require a minimum flow to dissipate the heat generated
by the pump impeller. A bypass around the pump located out
in the system provides the required flow and prevents the heat
from building up in the pump. The minimum flow is calculated
from the equation:
Summary of Contents for AUTOMATIC CONTROL SI Edition
Page 1: ...AUTOMATIC CONTROL for ENGINEERING MANUAL of COMMERCIAL BUILDINGS SI Edition ...
Page 4: ...ENGINEERING MANUAL OF AUTOMATIC CONTROL iv ...
Page 6: ...ENGINEERING MANUAL OF AUTOMATIC CONTROL vi ...
Page 46: ...ENGINEERING MANUAL OF AUTOMATIC CONTROL CONTROL FUNDAMENTALS 36 ...
Page 66: ...ENGINEERING MANUAL OF AUTOMATIC CONTROL PSYCHROMETRIC CHART FUNDAMENTALS 56 ...
Page 128: ...ENGINEERING MANUAL OF AUTOMATIC CONTROL ELECTRIC CONTROL FUNDAMENTALS 118 ...
Page 158: ...MICROPROCESSOR BASED DDC FUNDAMENTALS 148 ENGINEERING MANUAL OF AUTOMATIC CONTROL ...
Page 208: ...ENGINEERING MANUAL OF AUTOMATIC CONTROL BUILDING MANAGEMENT SYSTEM FUNDAMENTALS 198 ...
Page 493: ...INDEX ENGINEERING MANUAL OF AUTOMATIC CONTROL 483 INDEX ...
Page 506: ...ENGINEERING MANUAL OF AUTOMATIC CONTROL INDEX 496 NOTES ...
Page 507: ...INDEX ENGINEERING MANUAL OF AUTOMATIC CONTROL 497 NOTES ...
Page 508: ...ENGINEERING MANUAL OF AUTOMATIC CONTROL INDEX 498 NOTES ...
Page 509: ...INDEX ENGINEERING MANUAL OF AUTOMATIC CONTROL 499 NOTES ...
Page 510: ...ENGINEERING MANUAL OF AUTOMATIC CONTROL INDEX 500 NOTES ...
Page 511: ...INDEX ENGINEERING MANUAL OF AUTOMATIC CONTROL 501 NOTES ...
Page 512: ...ENGINEERING MANUAL OF AUTOMATIC CONTROL INDEX 502 NOTES ...