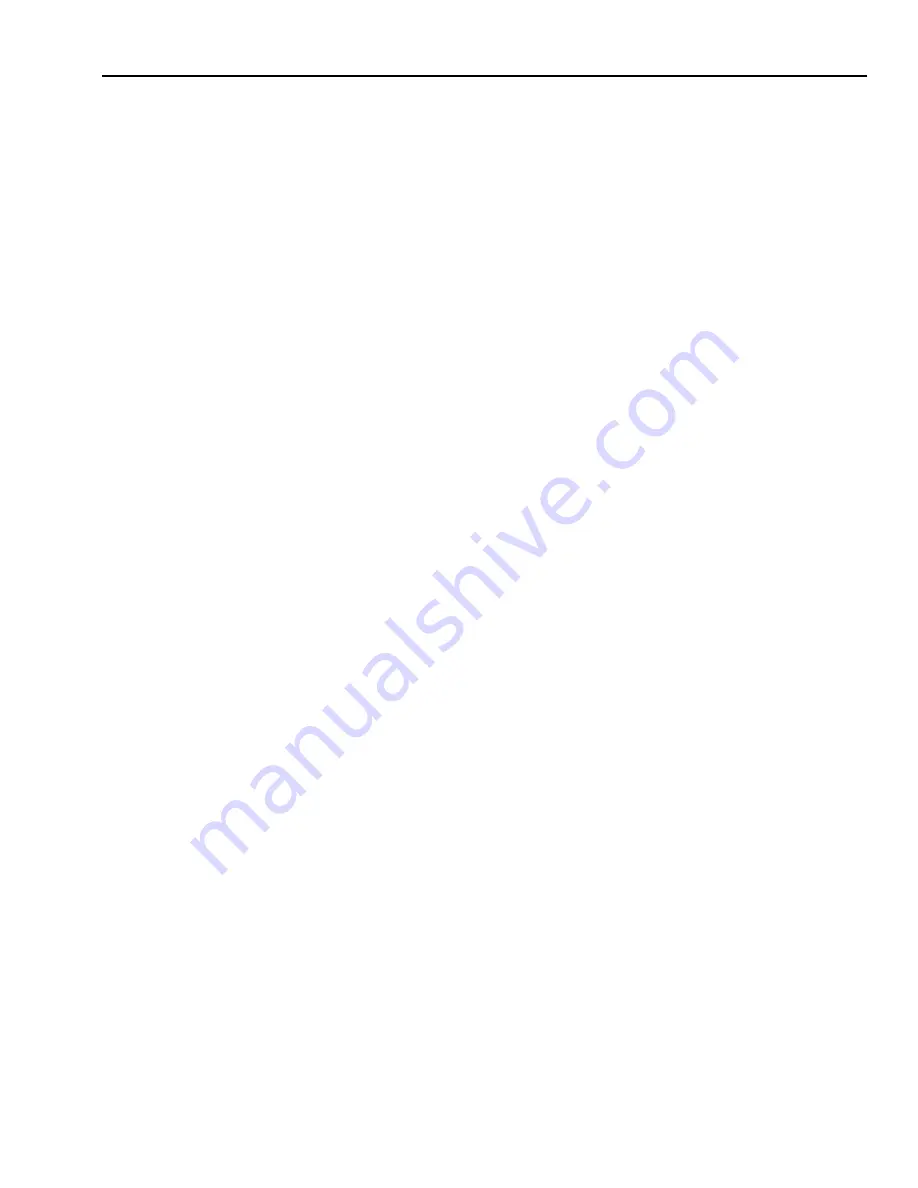
ENGINEERING MANUAL OF AUTOMATIC CONTROL
CHILLER, BOILER, AND DISTRIBUTION SYSTEM CONTROL APPLICATIONS
301
internal control that transfers liquid from refrigerant circuit to
absorbent circuit, transfers liquid from absorbent circuit to
refrigerant circuit, limits heat input, or a combination. Low
condenser water temperature decreases energy usage and
increases unit capacity.
When the condenser water temperature is too low, the
absorbent contains too much refrigerant and the solution
crystallizes. A safety control used by some absorption units
senses when the lithium bromide concentration is getting too
high with a low cooling water temperature and takes action to
avoid crystallization.
Absorption chillers are normally used where heat energy is
available at very low cost such as the exhaust from a steam
turbine. They also are used to reduce electric load and therefore
peak electric demand.
CHILLER CONTROL REQUIREMENTS
BASIC CHILLER CONTROL
Basic chiller control is a sensor in the chilled water supply
or return and a controller to provide a control signal to a capacity
control actuator. Capacity control is unique to each compressor
type. Summarized, the controls for each compressor type are:
1. Centrifugal–Controller output operates a pneumatic or
electric actuator to position inlet vanes as a function of the
controlled temperature. If speed control is available, the
controller sequences motor or rotor speed with inlet vanes.
2. Reciprocating–Controller provides a stepped output to
sequence refrigerant solenoid valves, valve unloading,
hot gas bypass, or multiple compressors as a function of
controlled temperature.
3. Screw–Controller operates speed control or a pneumatic
or electric actuator to position sliding bypass valve in
response to temperature input.
4. Absorption–Controller output operates a valve to
modulate the steam, hot water, or gas supply to maintain
controlled temperature.
Capacity high limit controls are used on centrifugal and screw
compressors to limit electrical demand during high load periods
such as morning cool-down. A load limiting control reduces
motor current draw to an adjustable maximum. Capacity of
some chillers can be reduced to as low as 10 percent.
Most chillers with modulating capacity control use proportional-
integral control, and often receive their chilled water setpoint from
a BMCS to optimize building energy efficiency.
When chilled water discharge temperature control is used,
offset can be reduced and control improved by using return
water temperature to reset the supply setpoint upward at light
loads to reduce the supply to return chilled water temperature
difference.
Proportional-integral (PI) control improves the accuracy of
control. When integral control is used, provisions to prevent
integral wind-up must be made. Integral wind-up during system
shut-down causes overshoot on start-up. For more information
on PI control, refer to Control Fundamentals section.
SYSTEM CONTROLS WHICH
INFLUENCE THE CHILLER
Whatever the configuration of a chilled water system, proper
control is necessary to meet the overall system requirements.
Condenser and chilled water temperatures establish refrigerant
pressure and energy needed per unit of cooling. Minimum
condenser temperature limits vary for different chiller designs.
Condenser temperatures should be maintained as close to the
minimum limits as possible to minimize refrigerant pressure.
Actual condenser water temperature is dependent on outdoor
wet bulb temperatures. Chilled water temperature is dependent
on system design and building load.
SAFETY CONTROLS
When an unsafe condition exists, the compressor should stop
automatically. Safety cutout controls may have automatic or
manual reset and include the following:
1. High condenser pressure.
2. Low refrigerant pressure or temperature.
3. Back-up for the low chilled water temperature controller
(on some reciprocating chillers).
4. High motor temperature.
5. Motor overload.
6. Low oil pressure.
7. Low oil sump temperature.
8. High oil sump temperature.
9. Chilled water flow interlock.
10. Condenser water flow interlock.
The preceding are all two-position (on-off) controls. In
addition, modulating limit controls sensing high condenser
pressure or low evaporator pressure-temperature reduce
compressor capacity to avoid the safety cutout conditions of
Items 1 and 2.
CHILLER/BMCS INTERFACE
Most chillers are supplied with microprocessor controllers
with a significant database of safety, operating, monitoring, and
setpoint status and values. The BMCS normally provides control
of the chilled water pump, the cooling tower fans, and the chiller
system (AUTO/OFF commands to the chiller controller). The
chilled water temperature setpoint and on occasions the
maximum load setpoint are also dictated by the BMCS.
Summary of Contents for AUTOMATIC CONTROL SI Edition
Page 1: ...AUTOMATIC CONTROL for ENGINEERING MANUAL of COMMERCIAL BUILDINGS SI Edition ...
Page 4: ...ENGINEERING MANUAL OF AUTOMATIC CONTROL iv ...
Page 6: ...ENGINEERING MANUAL OF AUTOMATIC CONTROL vi ...
Page 46: ...ENGINEERING MANUAL OF AUTOMATIC CONTROL CONTROL FUNDAMENTALS 36 ...
Page 66: ...ENGINEERING MANUAL OF AUTOMATIC CONTROL PSYCHROMETRIC CHART FUNDAMENTALS 56 ...
Page 128: ...ENGINEERING MANUAL OF AUTOMATIC CONTROL ELECTRIC CONTROL FUNDAMENTALS 118 ...
Page 158: ...MICROPROCESSOR BASED DDC FUNDAMENTALS 148 ENGINEERING MANUAL OF AUTOMATIC CONTROL ...
Page 208: ...ENGINEERING MANUAL OF AUTOMATIC CONTROL BUILDING MANAGEMENT SYSTEM FUNDAMENTALS 198 ...
Page 493: ...INDEX ENGINEERING MANUAL OF AUTOMATIC CONTROL 483 INDEX ...
Page 506: ...ENGINEERING MANUAL OF AUTOMATIC CONTROL INDEX 496 NOTES ...
Page 507: ...INDEX ENGINEERING MANUAL OF AUTOMATIC CONTROL 497 NOTES ...
Page 508: ...ENGINEERING MANUAL OF AUTOMATIC CONTROL INDEX 498 NOTES ...
Page 509: ...INDEX ENGINEERING MANUAL OF AUTOMATIC CONTROL 499 NOTES ...
Page 510: ...ENGINEERING MANUAL OF AUTOMATIC CONTROL INDEX 500 NOTES ...
Page 511: ...INDEX ENGINEERING MANUAL OF AUTOMATIC CONTROL 501 NOTES ...
Page 512: ...ENGINEERING MANUAL OF AUTOMATIC CONTROL INDEX 502 NOTES ...