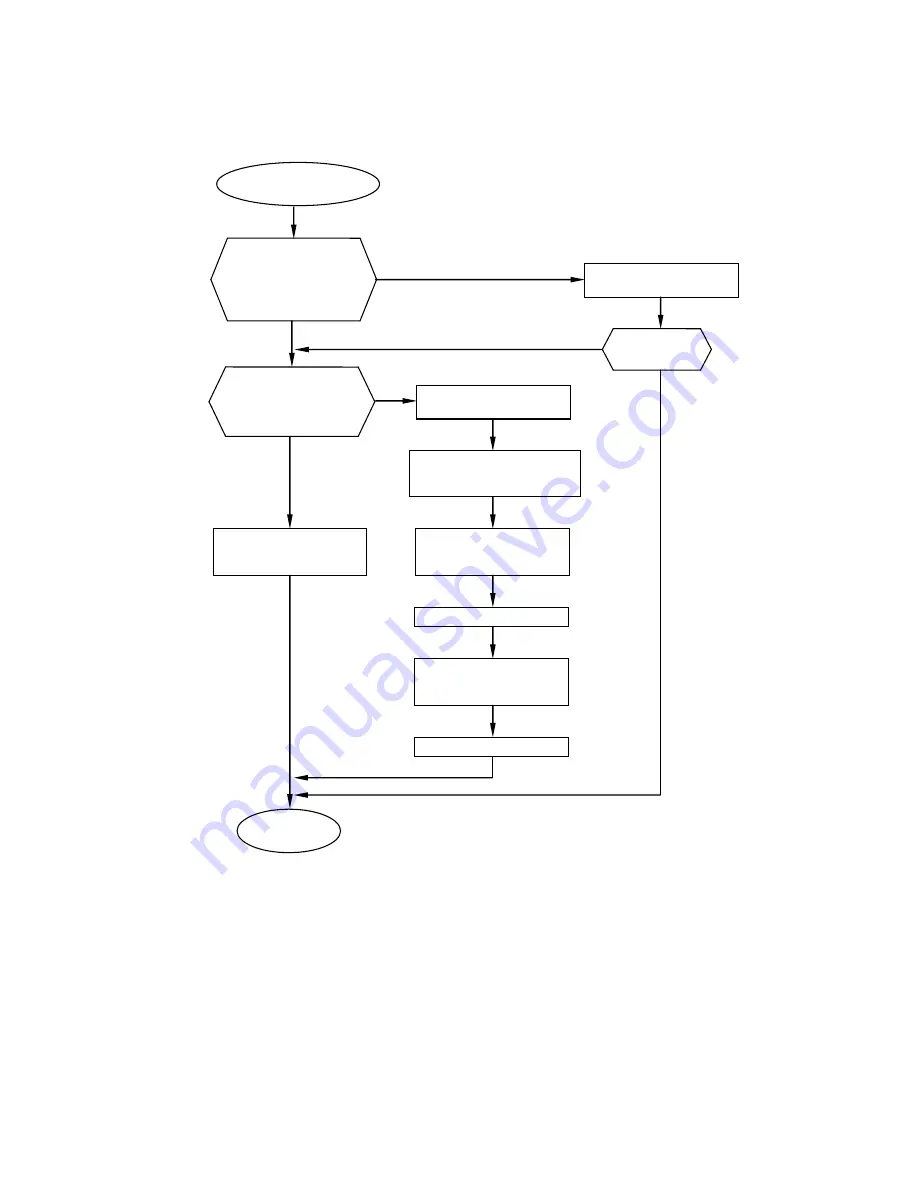
6-81
6.4.20 Makeup Level Sensor Broken (2)
(Follow the same procedure for
“Makeup Low Warning 2” and
“Makeup Low Fault 2”.)
[Caution]
1. When this warning “Makeup Level Sensor Broken (2)” is issued and the cause of this warning is not removed, the
other warning of “Makeup Low Warning 2” will be issued in one(1) hour. Furthermore, “Makeup Low Fault 2” will
be issued in another one (1) hour, and then IJP will be stopped.
2. Ink ejection is available even though IJP is stopped by the warning of “Makeup Low Fault 2”. However, if the cause
of this warning is not removed, “Makeup Level Sensor Broken (2)” will be issued again.
3. If the Makeup cartridge is replaced without Makeup ID validated properly, the state of level sensor becomes
invalid and this fault may occur.
Does the fault
recur?
Makeup Level
Sensor Broken (2)
Resume
operation
Go to “Level sensor
confirmation” screen
and check if all sensors
in Makeup reservoir
work properly.
Yes
No
Replace the sensor block
of Makeup reservoir.
Yes
Does the Remaining
Makeup Icon indicate
“Replaceable Makeup
Level”?
Yes
No
Execute “Reservoir
Makeup Drainage”
Confirm if the Remaining
Makeup Icon indicates
“Replaceable Makeup Level”.
Validate Makeup ID and
replace the Makeup
cartridge with new one.
Execute “ Ink refill”.
Validate Makeup ID and
replace
the
Makeup
cartridge with new one.
No
Execute “Ink drainage” to
prevent that the diluted
ink is used.
Execute “ Ink refill”.
Summary of Contents for UX Twin Nozzle
Page 1: ...Service Manual HITACHI Printer UX Twin Nozzle Model Revision February 2017 Version A ...
Page 106: ...3 30 Circuit diagram of EZJ127A board ...
Page 123: ...3 47 Circuit diagram of EZJ129 board ...
Page 131: ...3 55 3 3 20 Electrical Connection Diagram ...
Page 151: ...4 17 7 Reset the time of the replaced solenoid to 0 on the Parts usage time management screen ...
Page 352: ...7 1 7 Attached Drawing 7 1 Circulation System Diagram Circulation System Diagram ...
Page 354: ...7 3 7 3 Electrical Connection Diagram Electrical Connection Diagram ...