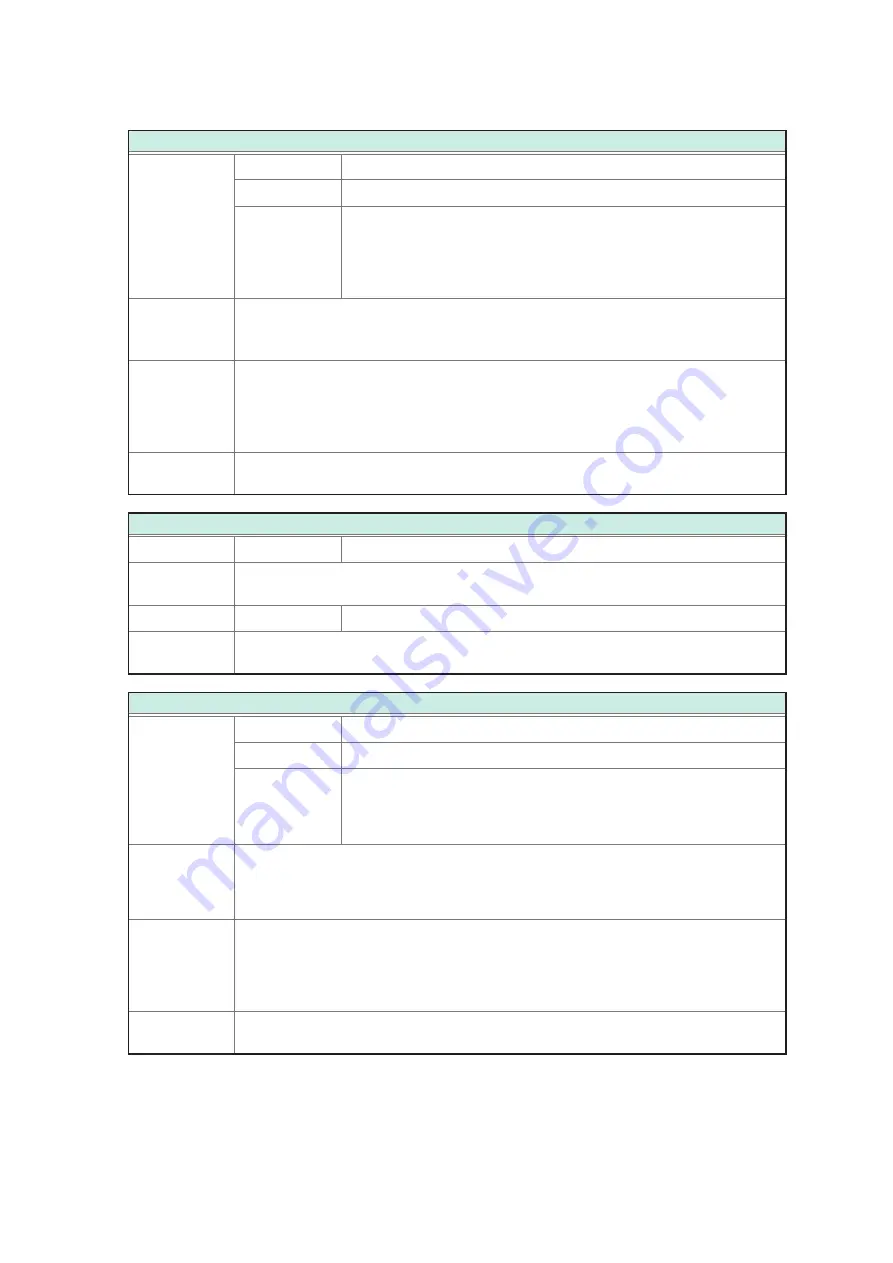
98
Message Reference
(4) Selecting the channel
Select and query channel
Syntax
Command
[ROUTe]: CLOSe <
Slot and channel No.
>
Query
[:ROUTe]:CLOSe?
Response
<Slot and channel No.>
<Slot and channel No.> = Slot No. × 100 + CH No.
A 3-digit number (or 4-digit number) is used to specify the channel.
Example: 208 (or 0208) when specifying channel 8 for
SLOT 2
.
1112 when specifying channel 12 for
SLOT 11
.
Description
Closes the specified slot and channel. The channel that was closed previously is
automatically opened. You can use the
*OPC?
query to check whether close operation has
completed.
Example
:CLOS 0122
Channel 22 for
SLOT 1
is closed.
:CLOS?
905
Channel 5 for
SLOT 9
is closed.
Note
•
Specifying a slot without a module will result in an execution error.
•
An execution error occurs during scan operation (command).
Open all relays
Syntax
Command
[:ROUTe]:OPEN
Description
Opens all channels. You can use the
*OPC?
query to check whether close operation has
completed.
Example
Command
:OPEN
Note
Executing this command while scan operation is in progress will cause scan operation to
stop and all relays to open.
Set and query channel delay time
Syntax
Command
:SYSTem:MODule:DELay <
Slot No.
>,<
Time/MIN/MAX/DEF
>
Query
:SYSTem:MODule:DELay?
Slot No.
>
Response
<Time>
<Slot No.> = 1 to 3 (NR1) (SW1001)
1 to 12 (NR1) (SW1002)
<Time> = 0 to 9.999 (NR2) [s] (MIN:0, MAX: 9.999, DEF: 0)
Description
Sets the additional delay time after relay operation (standby for the specified settling time
occurs).
After the delay time elapses, channel closing is completed.
The channel delay time can be specified for each slot.
Example
:SYSTem:MODule:DELay 1,0.01
Set the channel delay time for
SLOT 1
to 0.01 s.
:SYSTem:MODule:DELay? 3
0.5
The channel delay time for
SLOT 3
has been set to 0.5 s.
Note
•
Specifying a slot without a module will result in an execution error.
•
An execution error occurs during scan operation (command).
HIOKI SW1001A961-04
Summary of Contents for SW9001
Page 2: ...HIOKI SW1001A961 04...
Page 42: ...38 Channel Delay Function HIOKI SW1001A961 04...
Page 48: ...44 Scan Measurement Example HIOKI SW1001A961 04...
Page 50: ...46 Checking the Device Status HIOKI SW1001A961 04...
Page 52: ...48 Initialization Settings HIOKI SW1001A961 04...
Page 118: ...114 Sample Programs 3 Select FILE Save All HIOKI SW1001A961 04...
Page 160: ...156 Outline Drawings 12 4 Outline Drawings SW1001 Unit mm Tolerance 0 2 HIOKI SW1001A961 04...
Page 161: ...157 Outline Drawings SW1002 Unit mm Tolerance 0 2 12 Appendix HIOKI SW1001A961 04...
Page 162: ...158 Outline Drawings HIOKI SW1001A961 04...
Page 164: ...160 HIOKI SW1001A961 04...
Page 167: ...HIOKI SW1001A961 04...
Page 168: ...HIOKI SW1001A961 04...
Page 169: ...HIOKI SW1001A961 04...