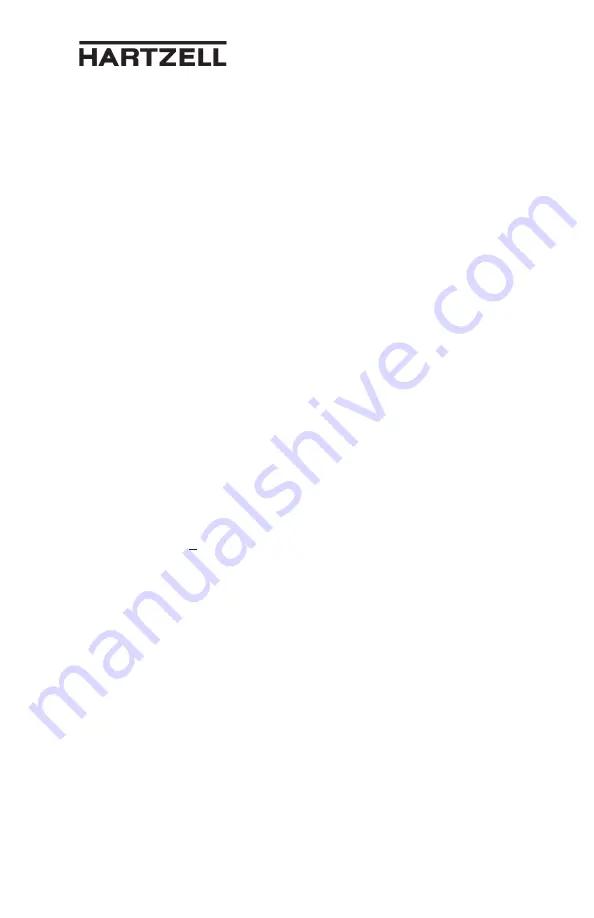
Propeller Owner's Manual
136
DESCRIPTION AND OPERATION
61-00-36
Page 2-9
Rev. 2 Feb/17
(f) A cockpit mounted pressure gage is attached
hydraulically to the pressure control unit.
(g) During flight propeller blade angle is controlled by
a governor to maintain a constant Propeller/Engine
RPM.
(h) During maneuvering (on land or water for fixed wing
aircraft or close to the ground maneuvering of a
craft that is lighter than air) reverse thrust as well as
positive thrust is required and is available in beta
range with manual blade angle control by the pilot.
(i) Beta operation (in Beta Range) for maneuvering
(positive and reverse thrust) is facilitated by the Beta
Lockout Assembly and a Reversing Spring. Refer
to Figure 2-1. The Beta Lockout Assembly prevents
Beta Operation unless a very low RPM (less than
900 RPM) is selected to insure ground or water
operation with fixed wing aircraft. The Reversing
Spring increases the force (oil pressure) required to
reverse blade angle.
(2) Pressure Control Unit
(a) The pressure control unit installs between the engine
and the governor on the governor accessory pad
provided on the engine. Refer to Figure 2-4.
1 A drive extension must be installed also for the
engine to still drive the governor and permit the
installation of the pressure control unit.
(b) Through a pilot control connected to the plunger, the
pressure control unit controls oil pressure from the
governor that is supplied to the propeller to permit
governed control and permit blade angle control in
beta range (low positive blade angles and reverse
blade angles).
(c) A cockpit mounted pressure gauge is attached
hydraulically to the pressure control unit to permit
the pilot to monitor the oil pressure output to the
propeller. Refer to Figure 2-2.