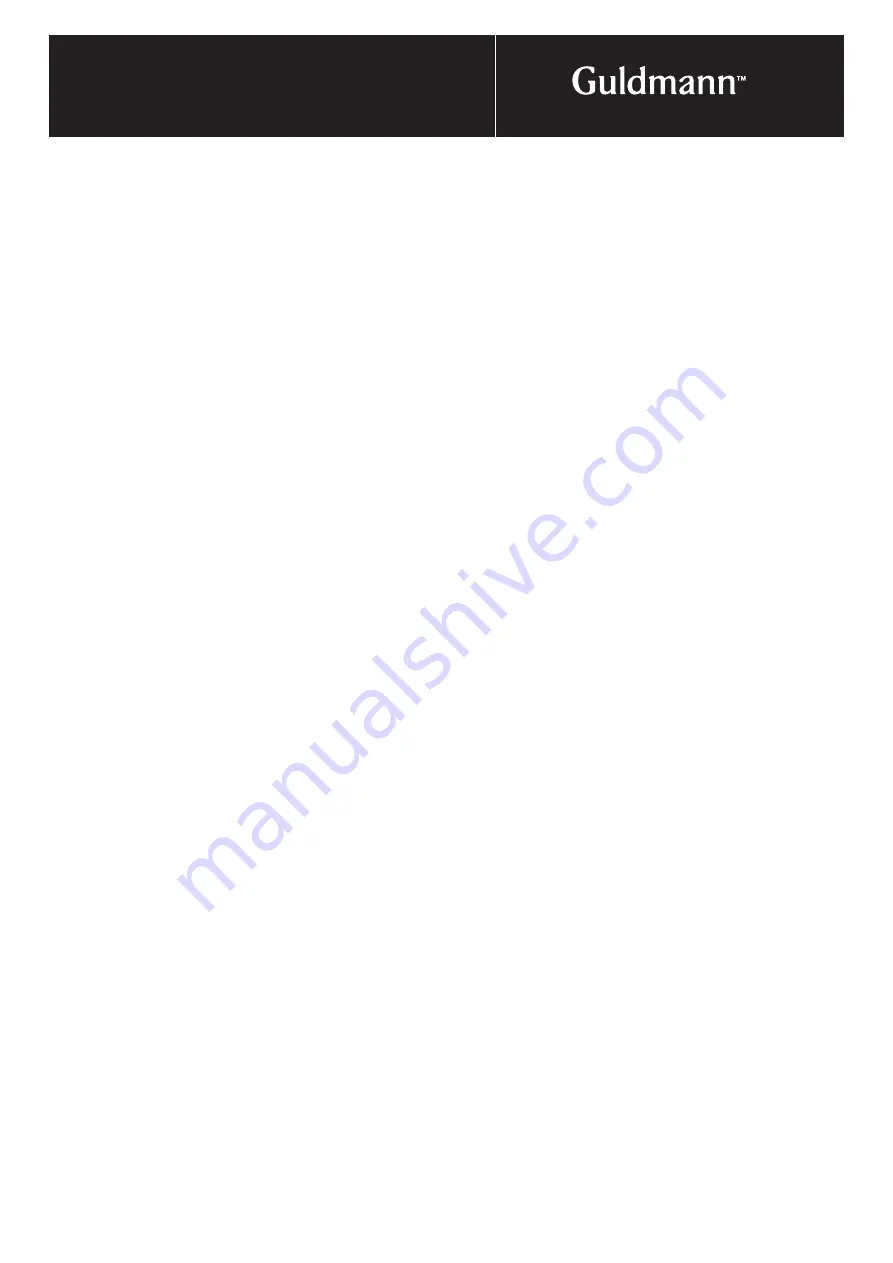
1.
I
n
tr
o
d
u
ct
Io
n
©
Guldmann
GB
-1394/11/08
General conditions
Installation in corrosive surroundings
Special guidelines must be observed when installing the
rail system around swimming pools, etc .
The surfaces of the brackets used, traverse travelling
trolleys, etc ., must be painted . Hoists, switch tracks,
Combi-locks, etc ., must be supplied with a special surface
treatment .
All fixing elements, nuts, washers, threaded rods, must be
acid-proof .
Acid-proof threaded rods and dual-component adhesive
must be used for installation in concrete, tiles, etc .
Through-going threaded rods or acid-proof screws must
be used for installation in wood .
Particular care should be taken to avoid damaging the
surface of painted components .
Washers made of synthetic material must be used in
between painted surfaces and nuts and ordinary washers .
Damaged paint must be repaired after installation, and
visible threaded rods, nuts, washers, etc ., must be covered
with paint RAL 9010 – white .
Hidden threaded rods, nuts, washers, and brackets in the
rail track must be treated with a silicone coating .
Wherever possible, nuts must be fitted with protective
caps .
There must be no swarf, dirt, or other impurities in the
rail system as they will accumulate moisture and lead to
corrosion .
Bearings in traverse travelling trolleys must be treated with
a silicone coating before installation .
NB!
Midi-rails with charging liners must not be used in corrosive
or dusty surroundings (areas around swimming pools and
at riding schools) .
Quality designation for bolts, etc .
A4/AISI 316 = acid-proof
A2/AISI 304/rustproof 18 .8 = not acid-proof
Installing rail systems with rated loads of more than
20 kg (0 lbs)
Certain precautions must be taken when installing rail
systems with rated loads of more than 250 kg (550 lbs) .
Room-covering rail systems and straight rail sections
including rail curves can be installed in cases where there
is a rated load of more than 250 kg (550 lbs) . Other rail
components must not be used .
A heavy duty model traverse travelling trolley must be used
in connection with room-covering rail systems .
Bracket types must be chosen in accordance with the list
of components, certain types of bracket must not be used
in connection with these installations .
Rails must be installed on top of the fitting when wall brack-
ets and floor posts are used .
The mutual distance between brackets must be adapted to
the type of rail in question in accordance with the instruc-
tions .
Two installation elements, must be used per bracket when
installing the system in a concrete ceiling or wall, in accor-
dance to the list page 40-41 .
Ceilings and walls made of materials other than concrete
must be carefully inspected and tested for suitability .
Special care should be taken when testing at 1 .5 times the
rated load .
Summary of Contents for GH2
Page 2: ......
Page 4: ......
Page 10: ...Bla bla Guldmann GB 1394 11 08 12 ...
Page 34: ...Bla bla Guldmann GB 1394 11 08 36 ...
Page 73: ...Bla bla Guldmann GB 1394 11 08 75 4 electrical connection Interconnection diagram GH2 twin ...
Page 87: ...Bla bla Guldmann GB 1394 11 08 89 ...
Page 88: ... Guldmann GB 1394 11 08 90 5 control Control 5 Checkliste 88 ...
Page 90: ... Guldmann GB 1394 11 08 92 6 toolbox ToolS 6 Overview of tools for rail installation 93 ...
Page 93: ... Guldmann GB 1394 11 08 95 7 service GH2 Service manual ...
Page 107: ... Guldmann GB 1394 11 08 109 7 service Periodic Inspection ...
Page 108: ......
Page 109: ......