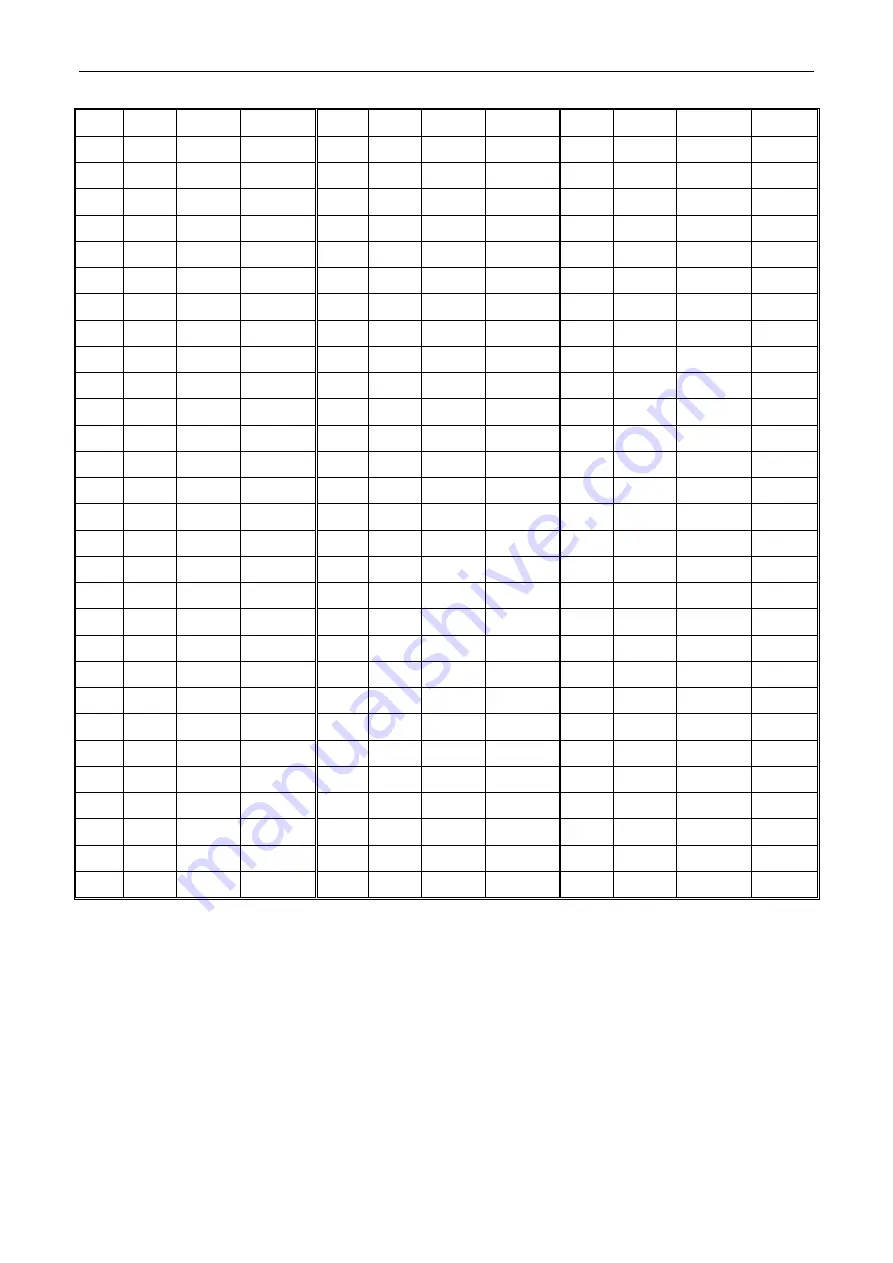
Ultra Heat GMV VRF Technical Service Manual_Heat Recovery Serial MAINTENANCE
185
4
39.2
53.46
0.898
68
154.4
3.729
2.781
132
269.6
0.5627
3.21
5
41
50.87
0.931
69
156.2
3.603
2.796
133
271.4
0.5487
3.212
6
42.8
48.42
0.965
70
158
3.481
2.811
134
273.2
0.5351
3.214
7
44.6
46.11
0.998
71
159.8
3.364
2.825
135
275
0.5219
3.216
8
46.4
43.92
1.033
72
161.6
3.252
2.838
136
276.8
0.509
3.218
9
48.2
41.84
1.067
73
163.4
3.144
2.852
137
278.6
0.4966
3.22
10
50
39.87
1.102
74
165.2
3.04
2.865
138
280.4
0.4845
3.222
11
51.8
38.01
1.138
75
167
2.94
2.877
139
282.2
0.4727
3.224
12
53.6
36.24
1.174
76
168.8
2.844
2.889
140
284
0.4613
3.226
13
55.4
34.57
1.209
77
170.6
2.752
2.901
141
285.8
0.4502
3.227
14
57.2
32.98
1.246
78
172.4
2.663
2.912
142
287.6
0.4394
3.229
15
59
31.47
1.282
79
174.2
2.577
2.923
143
289.4
0.4289
3.231
16
60.8
30.04
1.319
80
176
2.495
2.934
144
291.2
0.4187
3.232
17
62.6
28.68
1.356
81
177.8
2.415
2.944
145
293
0.4088
3.234
18
64.4
27.39
1.393
82
179.6
2.339
2.954
146
294.8
0.3992
3.235
19
66.2
26.17
1.429
83
181.4
2.265
2.964
147
296.6
0.3899
3.237
20
68
25.01
1.466
84
183.2
2.194
2.974
148
298.4
0.3808
3.238
21
69.8
23.9
1.503
85
185
2.125
2.983
149
300.2
0.3719
3.24
22
71.6
22.85
1.54
86
186.8
2.059
2.992
150
302
0.3633
3.241
23
73.4
21.85
1.577
87
188.6
1.996
3.001
151
303.8
0.3549
3.242
24
75.2
20.9
1.614
88
190.4
1.934
3.009
152
305.6
0.3468
3.244
25
77
20
1.65
89
192.2
1.875
3.017
153
307.4
0.3389
3.245
26
78.8
19.14
1.686
90
194
1.818
3.025
154
309.2
0.3312
3.246
27
80.6
18.32
1.722
91
195.8
1.763
3.033
155
311
0.3237
3.247
28
82.4
17.55
1.758
92
197.6
1.71
3.04
156
312.8
0.3164
3.249
29
84.2
16.8
1.793
93
199.4
1.658
3.047
157
314.6
0.3093
3.25
30
86
16.1
1.828
94
201.2
1.609
3.054
158
316.4
0.3024
3.251
31
87.8
15.43
1.863
95
203
1.561
3.061
159
318.2
0.2956
3.252
32
89.6
14.79
1.897
96
204.8
1.515
3.068
160
320
0.2891
3.253
33
91.4
14.18
1.931
97
206.6
1.47
3.074
Summary of Contents for Ultra Heat GMV-VQ72W/A-F
Page 1: ...Ultra Heat GMV Multi VRF TECHNICAL SERVICE MANUAL R410A Heat Recovery Series ...
Page 30: ...Ultra Heat GMV VRF Technical Service Manual_Heat Recovery Serial INSTALLATION 26 ...
Page 73: ...Ultra Heat GMV VRF Technical Service Manual_Heat Recovery Serial INSTALLATION 69 ...
Page 135: ...Ultra Heat GMV VRF Technical Service Manual_Heat Recovery Serial MAINTENANCE 131 ...
Page 203: ...Ultra Heat GMV VRF Technical Service Manual_Heat Recovery Serial MAINTENANCE 199 5 4 NCHS4B U ...
Page 205: ...Ultra Heat GMV VRF Technical Service Manual_Heat Recovery Serial MAINTENANCE 201 5 5 NCHS8B U ...
Page 207: ...Jf00303410 ...