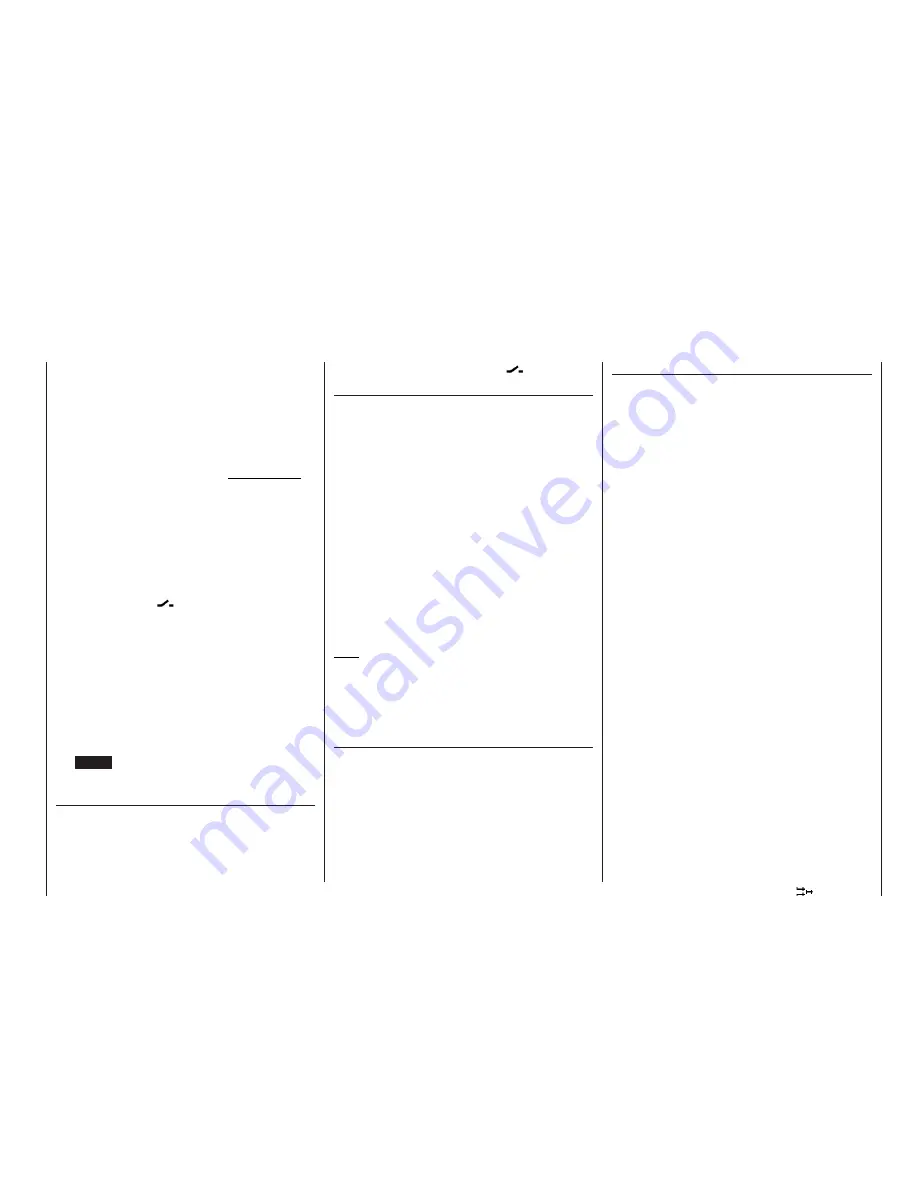
85
Program description:
Mixers
quired. In the »
MIX-only channel
« menu (see
page 108) it can now be separated from control
function input 1 (throttle / brake stick), and used
for some other purpose with the help of a “free mi-
xer” (see page 102). For instance, it could be used
to control an electric motor speed controller. The
same applies if the model features no braking sys-
tem at all, or no motor control at all.
•
You can use the option of setting transition times to
set up a “smooth” switch from one fl ight phase to
the next. This is carried out in the »
Phase setting
«
menu (see page 78).
Basic programming procedure:
1. Select the mixer with the rotary control pressed in.
Depending on the mixer, the bottom line of the
screen now displays
SEL
or
SYM
and
ASY
(for
setting mixer ratios separately for each side of
centre), and also
.
2. Select one of these fi elds using the rotary control.
3. Press the rotary control briefl y (inverse fi eld moves
to the selected line).
4. Use the rotary control to set the degree of differen-
tial or the mixer ratio, and assign the switch (if re-
quired).
Negative
and
positive parameter values can be
set; this allows you to reverse the direction of ser-
vo rotation if necessary, i.e. if one of the control
surfaces operates in the wrong “sense”.
(
CLEAR
= 0%).
5. Press the rotary control briefl y to leave the menu.
Assigning switches
With the exception of aileron differential, fl ap differen-
tial and the differential reduction function (see later),
all
wing mixers can be assigned an (optional) external
switch or control switch so that they can be switched
on and off in fl ight. If you call up this line you will see
the (by now) familiar switch symbol
.
Mixer neutral points (offset)
The neutral point of the mixers
• Aileron
NN
• Elevator
NN
• Flap
NN
is by default the zero point of the transmitter control,
i.e. that is the point at which they have no effect. At
full travel of the transmitter control the mixer provides
the full mixer value.
The neutral point (“offset”) of the mixer:
• Brake
NN
is by default the position of the transmitter control at
which the airbrakes are retracted.
The input (1, 8 or 9) and the
offset
are determined in
the “Brake” line of the »
Model type
« menu; see page
52. If you select “Input 1” please note that you should
enter your preferred “Throttle minimum” position (for-
ward / back) before you set the offset point.
Note:
If the offset is not positioned right at the end of the
transmitter control travel, the remainder of the travel
is a “dead zone”, i.e. the transmitter control does not
affect any of the airbrake
NN mixers from that point
on.
Mixer functions
The number of aileron and fl ap servos set in the »
Mo-
del type
« menu determines the extent of the mixer
list, but at least the “Brake
3 elevator” mixer will ap-
pear in addition to the “Aileron 2
4 rudder” mixer.
In the following section all the individual options of the
fi xed-wing menu will be discussed in turn.
Aileron differential
Aileron differential compensates for an unwanted
side-effect which occurs when ailerons are defl ected:
the problem known as “adverse yaw”. When the aile-
rons are defl ected, the drag generated by the down-
going aileron is greater than that produced by the up-
going aileron. The differential drag causes a yawing
motion around the vertical axis, in the opposite direc-
tion to the desired turn. This effect is much more pro-
nounced in model gliders with high aspect ratio wings
and short tail moments than in power models, whose
moment arms are much shorter. The pilot usually has
to counter the adverse yaw by giving a simultaneous
rudder defl ection in the opposite direction to the yaw.
However, this in turn causes additional drag and lo-
wers the aircraft’s effi ciency.
The alternative solution is to set up differential aile-
ron travel, i.e. the angular travel of the down-going ai-
leron is less than that of the up-going aileron, and this
reduces or even eliminates the (unwanted) adverse
yaw. This method can only be used if a separate ser-
vo is employed for each aileron. This solution usually
requires the aileron servos to be installed in the wing
panels themselves. An additional advantage of this
principle is that the shorter pushrods produce slop-
free aileron actuation systems which always centre
accurately.
Mechanical solutions are also possible, but they usu-
ally have to be “designed in” when the model is bu-
ilt, and in any case signifi cant mechanical differential
tends to cause additional slop in the control system.
Electronic differential is the modern solution, as it of-
fers the following important advantages:
The degree of differential can easily be varied without
affecting the travel of the up-going aileron. In the ex-
treme case it is possible to suppress the down-aile-
ron defl ection completely, i.e. only the up-going aile-
ron moves at all, and this arrangement is sometimes
called the “split” setting. “Split” ailerons not only tend
Summary of Contents for MC-22S
Page 1: ...1 mc 22s GB mc 22s 3D Rotary Programming System Programming manual ...
Page 33: ...33 Digital trims ...
Page 55: ...55 Program description Base setup model ...
Page 77: ...77 Program description Flight phases ...
Page 89: ...89 Program description Mixers ...
Page 174: ...174 ...
Page 175: ...175 ...
Page 176: ...176 ...
Page 177: ...177 ...
Page 178: ...178 ...