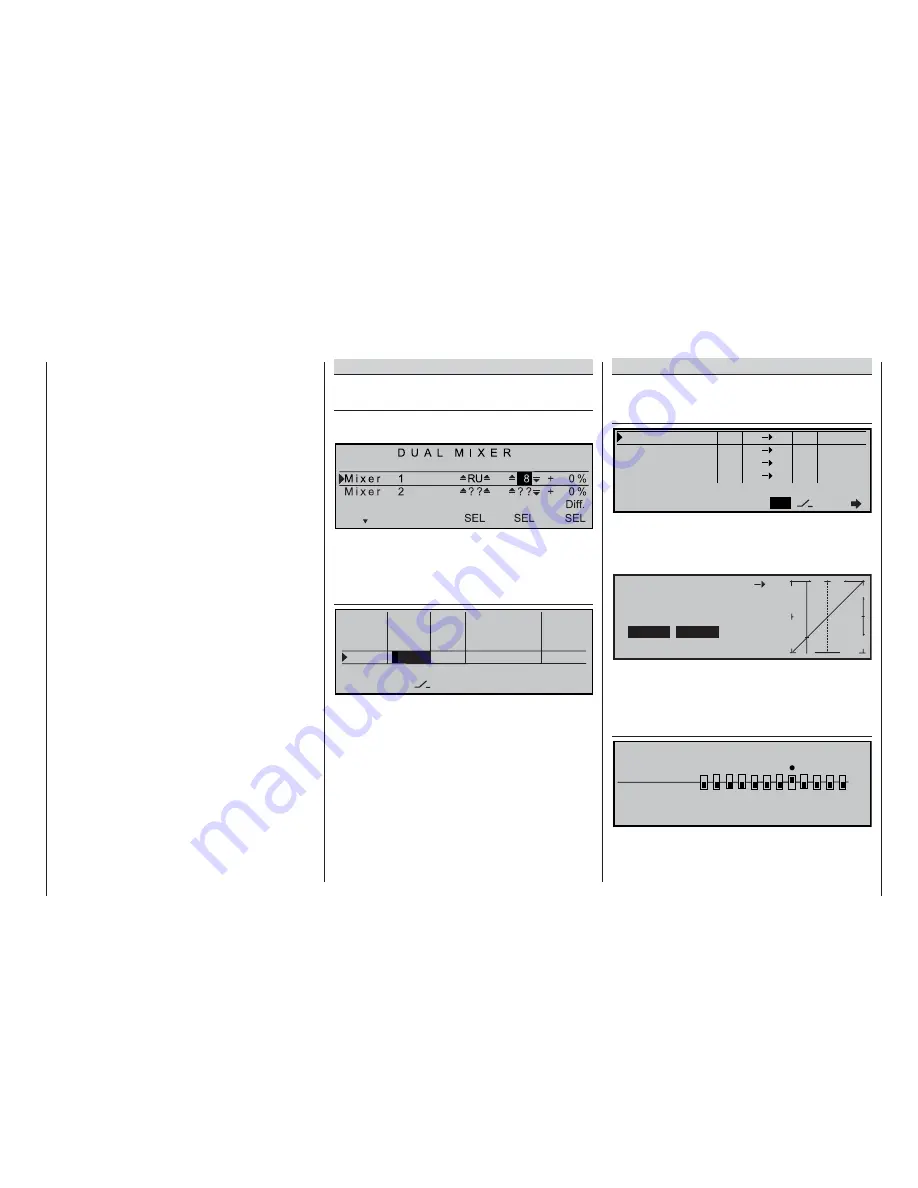
133
Servos operating in parallel
In many cases a second servo is required to run in
parallel with an existing servo; for example, if a se-
cond elevator or rudder is to be actuated by a separa-
te servo, or where a second servo is needed to cope
with the very high control forces required by a large
control surface. The same applies where two servos
are required simply due to the high control forces in-
volved.
This task could be solved simply by connecting both
servos together in the model using a conventional Y-
lead. However, this has the drawback that the linked
servos cannot be adjusted individually from the trans-
mitter, i.e. you forfeit the basic advantage of the com-
puter radio control system: freely variable servo set-
tings.
The fi rst variant of the two examples in this section
is preferable for applications of this type, as this kind
of system is simpler and faster to program using a
»
Dual mixer«
. In contrast to this, the second variant
– using the »
Free mixers«
menu – has to be used
where asymmetrical and / or non-linear curves are re-
quired.
In this example we want to “wire two rudders in paral-
lel”. The second rudder is connected to the otherwise
vacant receiver output 8.
Variant 1
In the menu …
»Dual mixer« (page 110)
… select one of the two dual mixers, and enter “RU”
and “8” using
SEL
, as shown in the screen shot:
Of course, the opposed movement „
“, which
would occur via “Input 8”, must not be allowed to take
place in this application. For this reason it is essential
to ensure in the menu …
»Control adjust« (page 58)
E n t e r 5 C n t r 5 0 % + 1 0 0 % + 1 0 0 % 0 . 0 0 . 0
E n t e r 6 C n t r 6
0 % + 1 0 0 % + 1 0 0 % 0 . 0 0 . 0
E n t e r 7 C n t r 7
0 % + 1 0 0 % + 1 0 0 % 0 . 0 0 . 0
E n t e r 8
f r e e
0 % + 1 0 0 % + 1 0 0 % 0 . 0 0 . 0
o f f s e t - t r a v e l + - t i m e +
t
s
A S Y
S Y M
A S Y
S Y M
S E L
S E L
… that “Input 8” is set to “free”, so that the control
function is separated from the control channel.
If both dual mixers are already in use for other purpo-
ses, you will need to fall back on the next solution.
Variant 2
In this variant you set up a “Tr RU
8” mixer in the
menu …
»Free mixers« (page 102)
L i n e a r M I X 1
T r R U 8
= >
L i n e a r M I X 2
? ? ? ?
- - - -
L i n e a r M I X 3
? ? ? ?
- - - -
L i n e a r M I X 4
? ? ? ?
- - - -
t y p e f r o m t o
A d j u s t
S E L
t
S E L
S E L
Selecting “Tr” setting in the “Type” column, so that the
rudder trim acts upon both rudder servos.
Now move to the graphic page and set a
SYM
metri-
cal mixer input of +100%:
L i n e a r M I X 1 R U 8
M i x i n p u t O f f s e t
+ 1 0 0 % + 1 0 0 %
0 %
®
O
U
T
P
U
T
-
+
10
0
S T O
A S Y
S Y M
C L R
Here again, “Input 8” should be programmed to “free”
in the »
Control adjust«
menu. Alternatively you
could separate control function “8” from control chan-
nel “8” in the menu …
»MIX-only channel« (page 108)
M I X O N L Y C H A N N E L
M I X o n l y
n o r m a l
1 2 3 4 5 6 7 8 9 1 0 1 1 1 2
Programming examples – Fixed-wing models
Summary of Contents for MC-22S
Page 1: ...1 mc 22s GB mc 22s 3D Rotary Programming System Programming manual ...
Page 33: ...33 Digital trims ...
Page 55: ...55 Program description Base setup model ...
Page 77: ...77 Program description Flight phases ...
Page 89: ...89 Program description Mixers ...
Page 174: ...174 ...
Page 175: ...175 ...
Page 176: ...176 ...
Page 177: ...177 ...
Page 178: ...178 ...