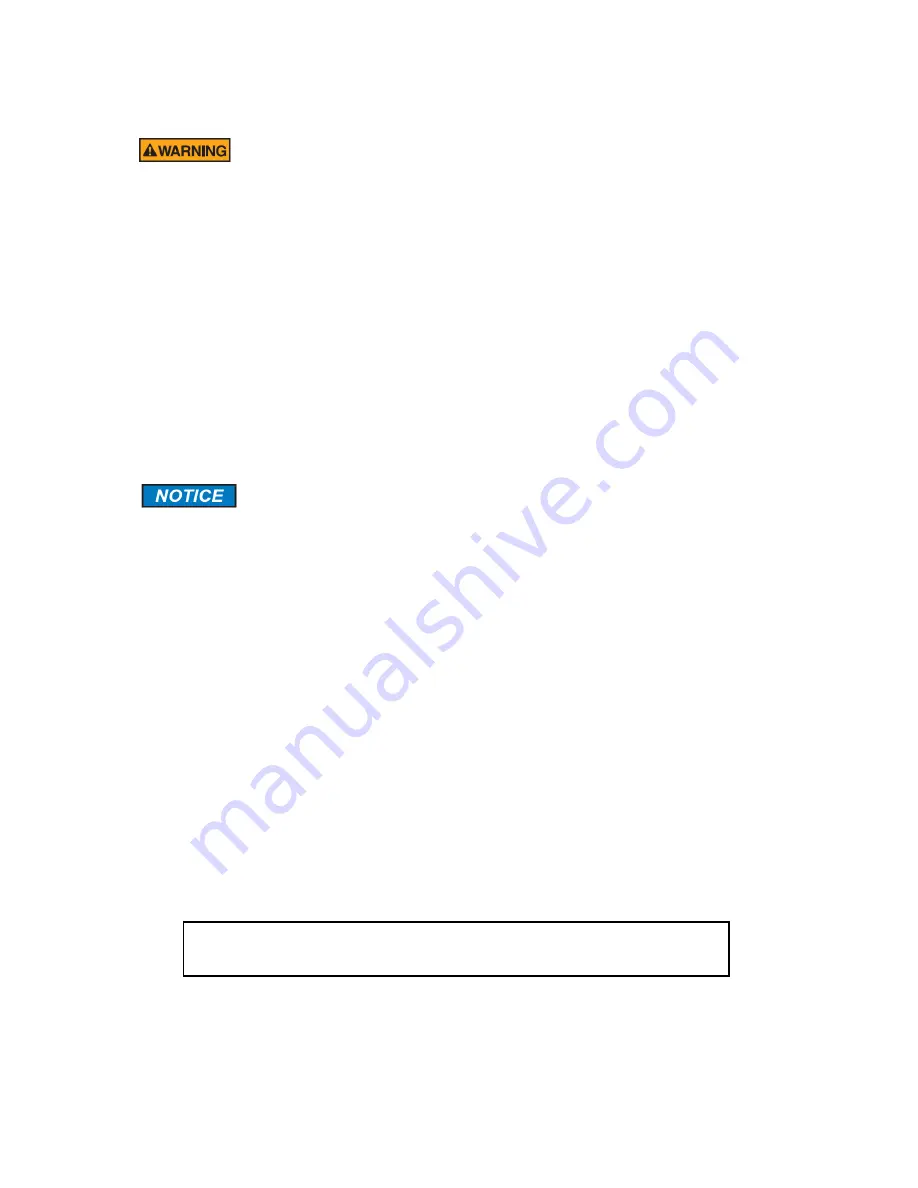
Revision 1
21
6/27/2017
Explosive, toxic and hot gases and molten sulfur may be released once the
stream jacketed ball valve is opened. All company and/or regulatory
agency safety procedures and rules should be adhered to. Breathing
apparatus and personal protective equipment (
ie.
gloves, coveralls and
protective eye wear) should be worn and a safety person(s) should be
observing.
Do not take unnecessary risks even if you believe the tailgas
line to be at negative pressure.
Before mounting the oven cabinet at the process (sample) connection, check to ensure that:
a) The bolt holes in the steam jacketed nozzle flange are large enough to accommodate the
four (4) bolts on the analyzer system flange
b) The two (2) flanges are correctly aligned
c) A new gasket of proper size and material is available
d) The appropriate nuts are available to put onto the system flange bolts.
The actual sample probe is sized so that it provides a minimum of 25%
penetration into the process pipe. The diameter of the pipe is provided by
the customer.
If
all of the above
conditions are satisfied:
a) Put the new gasket in place and move the analyzer system into position placing the four
(4) bolts through the steam jacketed nozzle flange holes.
b) Place the four (4) nuts onto the bolts and tighten.
c) Inspect the flange connection using company and/or regulatory agency procedures to
ensure that the connection is leak-tight (no gases are escaping).
d) Check that process gas is not leaking into the analyzer oven.
When the oven cabinet is securely fastened to the process sample point flange, make sure
that the oven cabinet cradle is secured to the support structure. This is to ensure that the
framework and support structure, not the flange connection, are bearing the weight of the
analyzer system.
Install the sample probe:
a) Remove the oven cabinet lid and insert the probe into the packing gland at the bottom of
the oven until it reaches the steam jacketed ball valve.
943-TGS-CE
Refer to the 943-TGS-CE User Manual Section 2.7.3.
Summary of Contents for 943-TGS
Page 50: ...Revision 1 50 6 27 2017 Figure 4 14 Network Sub Panel ...
Page 94: ...Revision 1 94 6 27 2017 Figure 9 1 Mounting Detail ...
Page 95: ...Revision 1 95 6 27 2017 Figure 9 2 Oven Cabinet Detail ...
Page 96: ...Revision 1 96 6 27 2017 Figure 9 3 Control Cabinet Detail ...
Page 97: ...Revision 1 97 6 27 2017 Figure 9 4 Power Air Steam Requirements and Input Output Detail ...
Page 98: ...Revision 1 98 6 27 2017 Figure 9 5 Control Cabinet to Oven Cabinet Interconnect Detail ...
Page 99: ...Revision 1 99 6 27 2017 Figure 9 6 AC Wiring Detail ...
Page 100: ...Revision 1 100 6 27 2017 Figure 9 7 DC and Signal Wiring Detail ...
Page 101: ...Revision 1 101 6 27 2017 This page intentionally left blank ...