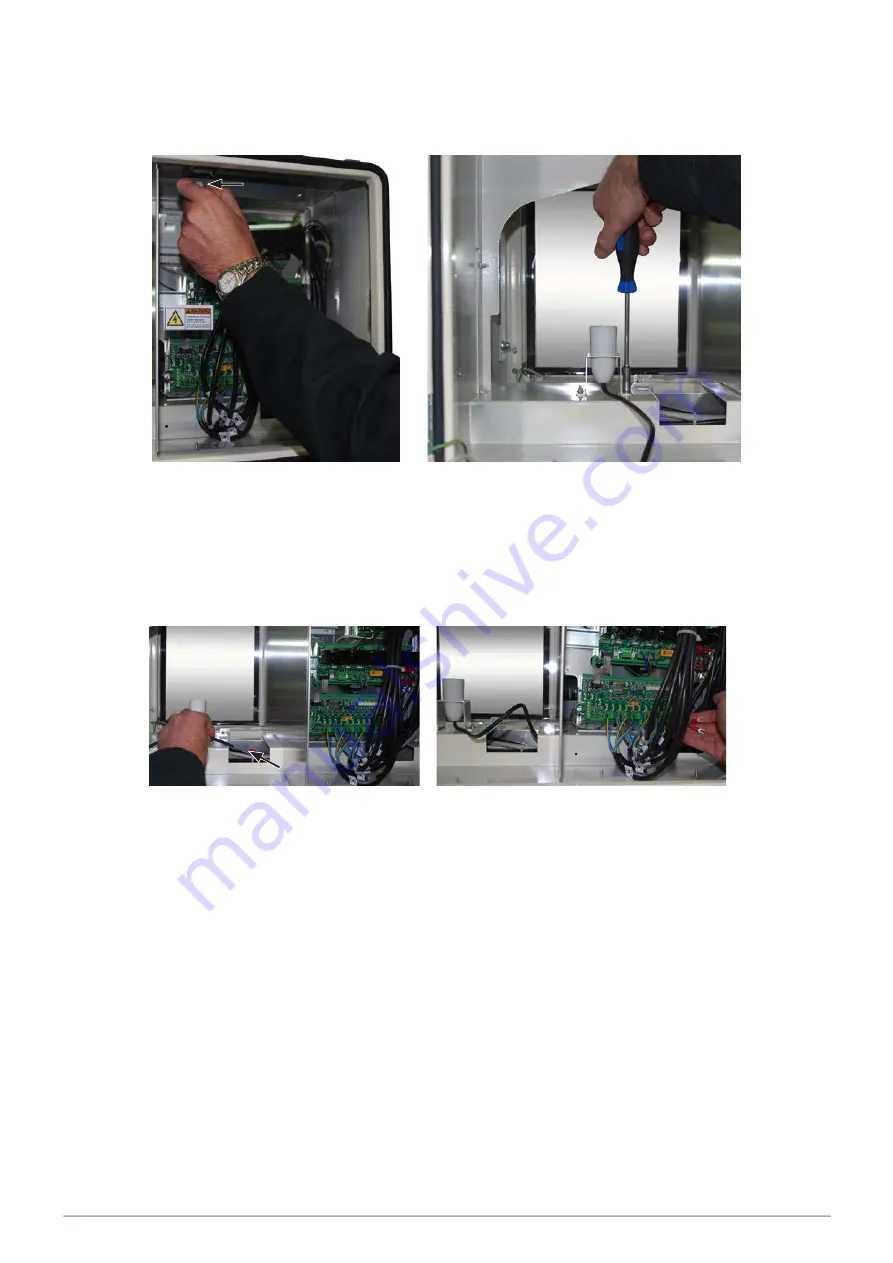
INST
ALLA
TION
36
PULSE Installation, Commissioning and Servicing Manual - Revision 19
Procedure
The following steps describe how to install the head lighting
Dome nut
Dome nut
1. At the rear of the head remove
the shield covering the gear
plate by first removing the
dome nuts on the top of the
shield.
2.
Fit the light mounting bracket to the 2
studs in the middle of the head. Secure
with 2 M4 nuts.
Cable channel
Cable channel
3.
Run the lighting assembly cable through the cable channel and up to the
Motor Drive Module.