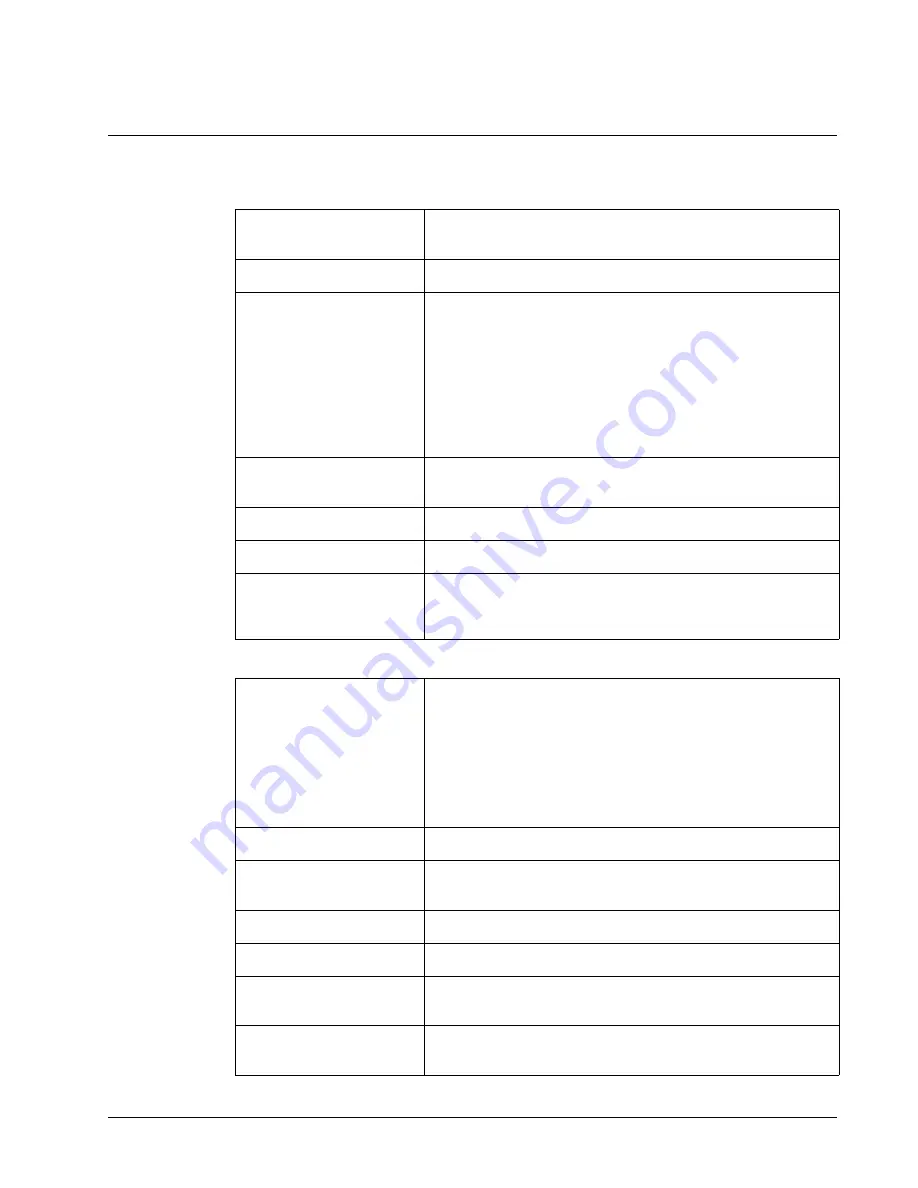
Signal Descriptions
Outputs
Motor Command
± 10 Volt range signal for driving amplifier. In servo mode, motor
command output is updated at the controller sample rate. In the motor
off mode, this output is held at the OF command level.
Amplifier Enable
Signal to disable and enable an amplifier. Amp Enable goes low on Abort
and OE1.
PWM / Step
PWM/STEP OUT is used for directly driving power bridges for DC servo
motors or for driving step motor amplifiers. For servo motors: If you are
using a conventional amplifier that accepts a ±10 Volt analog signal, this
pin is not used and should be left open. The PWM output is available in
two formats: Inverter and Sign Magnitude. In the Inverter mode, the
PWM (64kHz) signal is .2% duty cycle for full negative voltage, 50% for 0
Voltage and 99.8% for full positive voltage (64kHz Switching Frequency).
In the Sign Magnitude Mode (MT1.5), the PWM (128 kHz) signal is 0% for
0 Voltage, 99.6% for full voltage and the sign of the Motor Command is
available at the sign output (128kHz Switching Frequency).
PWM / Step
For stepper motors: The STEP OUT pin produces a series of pulses for
input to a step motor driver. The pulses may either be low or high. The
pulse width is 50%.
Sign / Direction
Used with PWM signal to give the sign of the motor command for servo
amplifiers or direction for step motors.
Error
The signal goes low when the position error on any axis exceeds the value
specified by the error limit command, ER.
Output 1-Output 8
Output 9-Output 16
(DMC-4250 thru 4080)
The high power optically isolated outputs are uncommitted and may be
designated by the user to toggle relays and trigger external events. The
output lines are toggled by Set Bit, SB, and Clear Bit, CB, instructions. The
OP instruction is used to define the state of all the bits of the Output port.
Inputs
Encoder, MA+, MB+
Position feedback from incremental encoder with two channels in
quadrature, CHA and CHB. The encoder may be analog or TTL. Any
resolution encoder may be used as long as the maximum frequency does
not exceed 22,000,000 quadrature states/sec. The controller performs
quadrature decoding of the encoder signals resulting in a resolution of
quadrature counts (4 x encoder cycles). Note: Encoders that produce
outputs in the format of pulses and direction may also be used by
inputting the pulses into CHA and direction into Channel B and using the
CE command to configure this mode.
Encoder Index, MI+
Once-Per-Revolution encoder pulse. Used in Homing sequence or Find
Index command to define home on an encoder index.
Encoder, MA-, MB-, MI-
Differential inputs from encoder. May be input along with CHA, CHB for
noise immunity of encoder signals. The CHA- and CHB- inputs are
optional.
Auxiliary Encoder, AA+, AB+, Aux
A-, Aux B-
Inputs for additional encoder. Used when an encoder on both the motor
and the load is required. Not available on axes configured for step motors.
Abort
A low input stops commanded motion instantly without a controlled
deceleration. Also aborts motion program.
Reset
A low input resets the state of the processor to its power-on condition.
The previously saved state of the controller, along with parameter values,
and saved sequences are restored.
Electronic Lock Out
Input that when triggered will shut down the amplifiers at a hardware
level. Useful for safety applications where amplifiers must be shut down
at a hardware level.
Appendices ▫ 179
DMC-42x0 User Manual
Summary of Contents for DMC-42 0 Series
Page 195: ...ICM 2900 PCB Layout Appendices 191 DMC 42x0 User Manual...
Page 205: ...CB 50 100 Drawings Appendices 201 DMC 42x0 User Manual...
Page 206: ...Appendices 202 DMC 42x0 User Manual...
Page 207: ...Appendices 203 DMC 42x0 User Manual...
Page 208: ...Appendices 204 DMC 42x0 User Manual...
Page 209: ...Appendices 205 DMC 42x0 User Manual...
Page 210: ...Appendices 206 DMC 42x0 User Manual...
Page 211: ...Appendices 207 DMC 42x0 User Manual...
Page 214: ...CB 50 80 Drawing Appendices 210 DMC 42x0 User Manual...