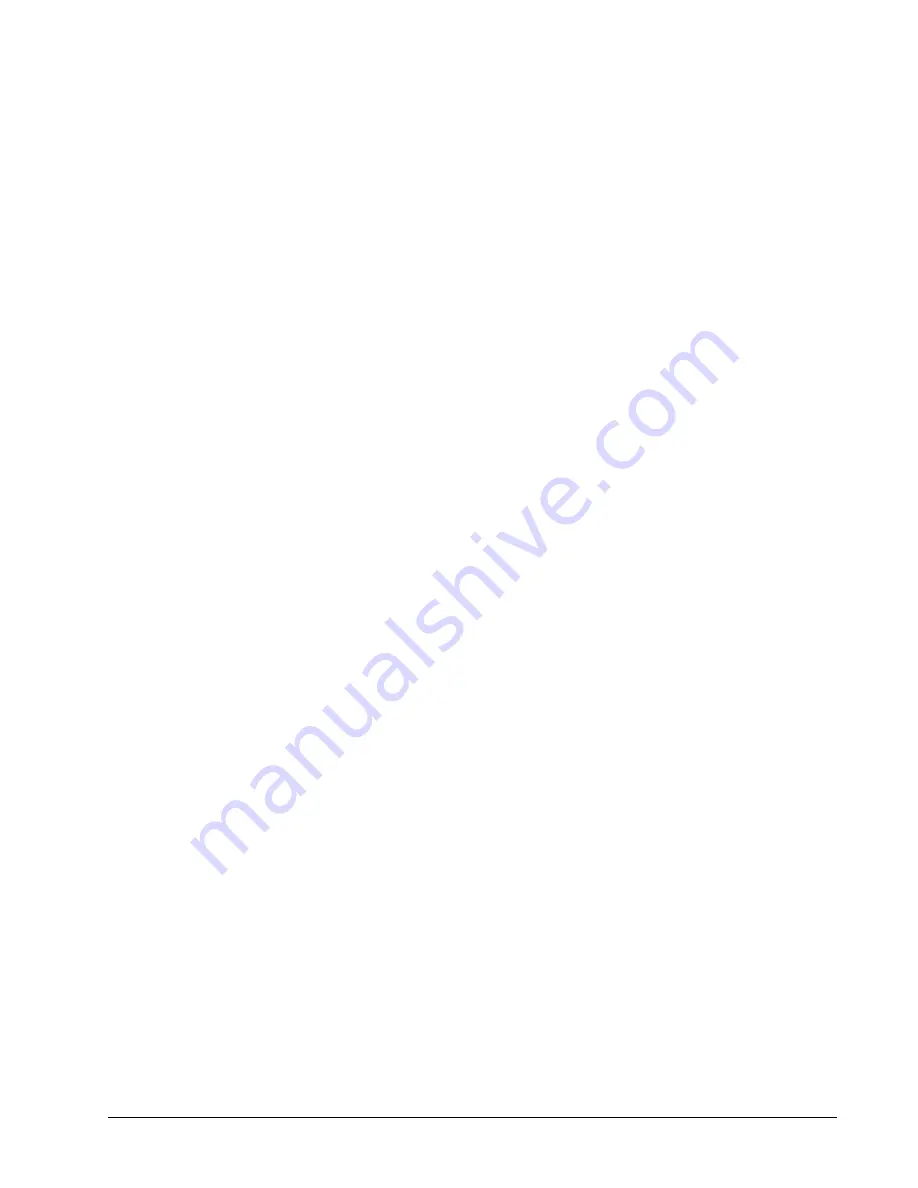
Trapezoidal commutation is a time-tested way for determining the motor location within a magnetic cycle;
However, interpretation of hall sensor feedback varies between motor manufactures requiring the user to find the
correct wiring combination.
Before wiring the motor the user should determine which is easier: Wiring the hall sensors or wiring the motor
phases. This method will start with wiring both the halls and motor phases at random then trying each of the 6
wiring combinations of either the halls
or
the motor phases (not both)
.
For each combination, the user will be
asked to check the open-loop velocity in both directions . Some of the wiring combinations will lead to no motion,
this is expected. The following directions are given using the A-axis as an example.
1. Wire the 3 motor phase wires and 3 hall sensors randomly. Do not connect the motor to any external
mechanics or load, a free spinning motor is required for testing. Take all safety precautions necessary as the
motor tests below will result in a runaway condition.
2. Set the PID’s and
BR
to zero and disable off-on-error (
OE
) to allow for full rotation of the motor in open-
loop. Issue the following commands from a Galil terminal program:
KPA= 0
KDA= 0
KIA= 0
BRA= 0
OE 0
SH A
3. Place a small offset voltage on the motor command line using the
OF
command (ex
OFA= 0.5
). The
smallest
OF
possible to see motion is recommended. If no motion presents itself, increase in small increments
until you see motion. If your
OF
is beyond what is expected to see motion, record “no motion” using one of
the tables below (Table 2.7 for swapping motor phases or Table 2.8 for swapping halls) and try the next wiring
combination.
Note: To stop the motor from spinning use either the
MO A
command or issue
OFA= 0
.
4. Once spinning, check the velocity of the motor with the
TV A
command. Record this value under “+
Velocity” in either Table 2.7 or Table 2.8.
5. Issue an equal but opposite
OF
. For example, if you previously issued
OFA= 0.5
now issue
OFA= -0.5
.
Record this velocity under “- Velocity.”
6. Issue
OFA= 0
or
MO A
to stop the motors. Power down the controller and amplifiers system and swap 2
wires of the hall sensors or motor power leads—whichever method is being used (Remember, chose one or
the other, not both!). Keep track of what cable combinations have been tested (labeling the phases maybe
useful) in the example table in Table 2.6, motor phases were recorded based upon their insulation color.
7. Repeat steps 2-6 for every possible wiring combination, there will be six and Table 2.7 or Table 2.8 below
should be completely filled out.
8. The correct wiring combination will be the one with the least difference in magnitude between the velocities
in the positive and negative direction. In the case where there are two combinations that meet this criteria,
choose the combination that has the higher velocities. In the example table shown in Table 2.6, Trial 1 would
be the correct choice.
Chapter 2 Getting Started ▫ 19
DMC-42x0 User Manual
Summary of Contents for DMC-42 0 Series
Page 195: ...ICM 2900 PCB Layout Appendices 191 DMC 42x0 User Manual...
Page 205: ...CB 50 100 Drawings Appendices 201 DMC 42x0 User Manual...
Page 206: ...Appendices 202 DMC 42x0 User Manual...
Page 207: ...Appendices 203 DMC 42x0 User Manual...
Page 208: ...Appendices 204 DMC 42x0 User Manual...
Page 209: ...Appendices 205 DMC 42x0 User Manual...
Page 210: ...Appendices 206 DMC 42x0 User Manual...
Page 211: ...Appendices 207 DMC 42x0 User Manual...
Page 214: ...CB 50 80 Drawing Appendices 210 DMC 42x0 User Manual...