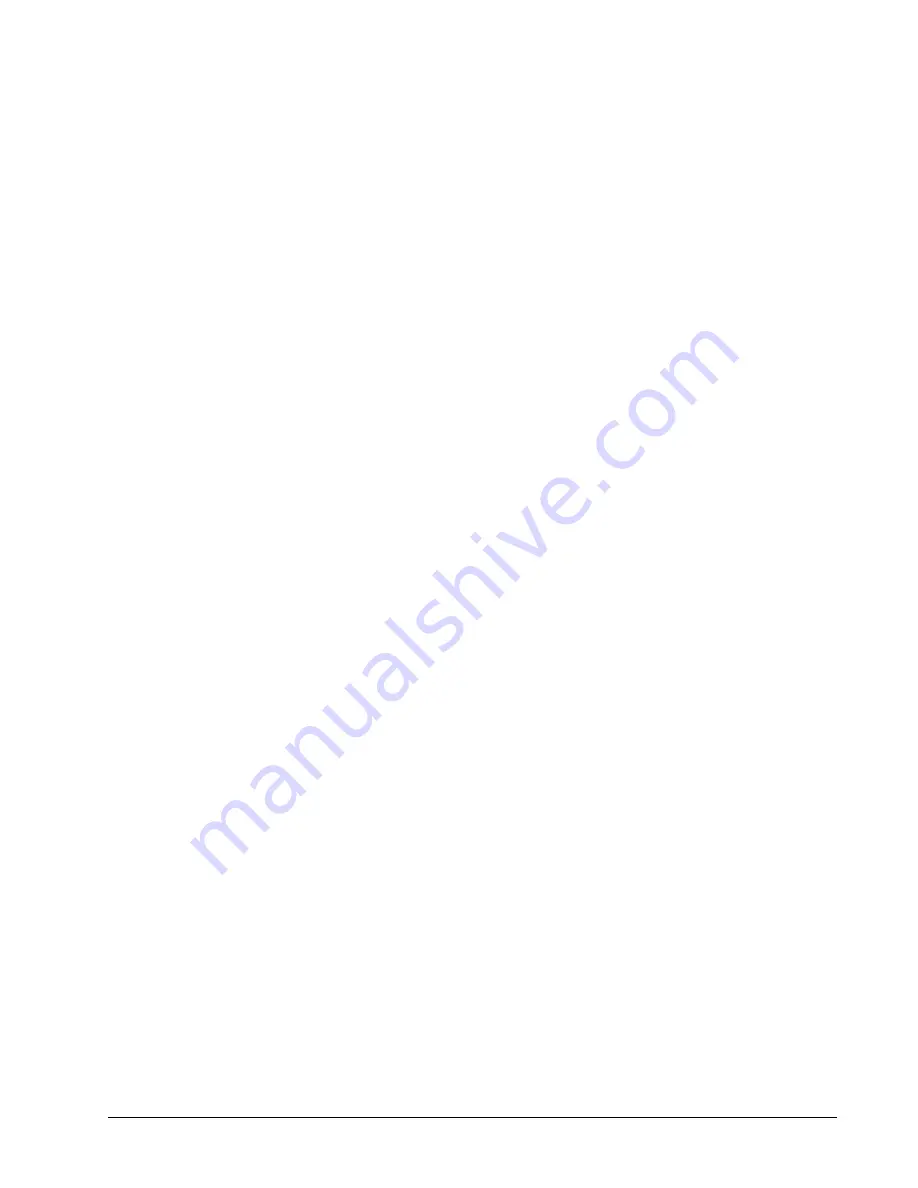
To illustrate the procedure of setting the cam mode, consider the cam relationship for the slave axis Y, when the
master is X. Such a graphic relationship is shown in Figure 6.13.
Step 1. Selecting the master axis
The first step in the electronic cam mode is to select the master axis. This is done with the instruction
EAp where p = X,Y,Z,W,E,F,G,H
p is the selected master axis
For the given example, since the master is x, we specify EAX
Step 2. Specify the master cycle and the change in the slave axis (or axes).
In the electronic cam mode, the position of the master is always expressed modulo one cycle. In this example, the
position of x is always expressed in the range between 0 and 6000. Similarly, the slave position is also redefined
such that it starts at zero and ends at 1500. At the end of a cycle when the master is 6000 and the slave is 1500,
the positions of both x and y are redefined as zero. To specify the master cycle and the slave cycle change, we use
the instruction EM.
EM x,y,z,w
where x,y,z,w specify the cycle of the master and the total change of the slaves over one cycle.
The cycle of the master is limited to 8,388,607 whereas the slave change per cycle is limited to 2,147,483,647. If
the change is a negative number, the absolute value is specified. For the given example, the cycle of the master is
6000 counts and the change in the slave is 1500. Therefore, we use the instruction:
EM 6000,1500
Step 3. Specify the master interval and starting point.
Next we need to construct the ECAM table. The table is specified at uniform intervals of master positions. Up to
256 intervals are allowed. The size of the master interval and the starting point are specified by the instruction:
EP m,n
where m is the interval width in counts, and n is the starting point.
For the given example, we can specify the table by specifying the position at the master points of 0, 2000, 4000 and
6000. We can specify that by
EP 2000,0
Step 4. Specify the slave positions.
Next, we specify the slave positions with the instruction
ET[n]=x,y,z,w
where n indicates the order of the point.
The value, n, starts at zero and may go up to 256. The parameters x,y,z,w indicate the corresponding slave position.
For this example, the table may be specified by
ET[0]=,0
ET[1]=,3000
ET[2]=,2250
ET[3]=,1500
This specifies the ECAM table.
Chapter 6 Programming Motion ▫ 77
DMC-42x0 User Manual
Summary of Contents for DMC-42 0 Series
Page 195: ...ICM 2900 PCB Layout Appendices 191 DMC 42x0 User Manual...
Page 205: ...CB 50 100 Drawings Appendices 201 DMC 42x0 User Manual...
Page 206: ...Appendices 202 DMC 42x0 User Manual...
Page 207: ...Appendices 203 DMC 42x0 User Manual...
Page 208: ...Appendices 204 DMC 42x0 User Manual...
Page 209: ...Appendices 205 DMC 42x0 User Manual...
Page 210: ...Appendices 206 DMC 42x0 User Manual...
Page 211: ...Appendices 207 DMC 42x0 User Manual...
Page 214: ...CB 50 80 Drawing Appendices 210 DMC 42x0 User Manual...