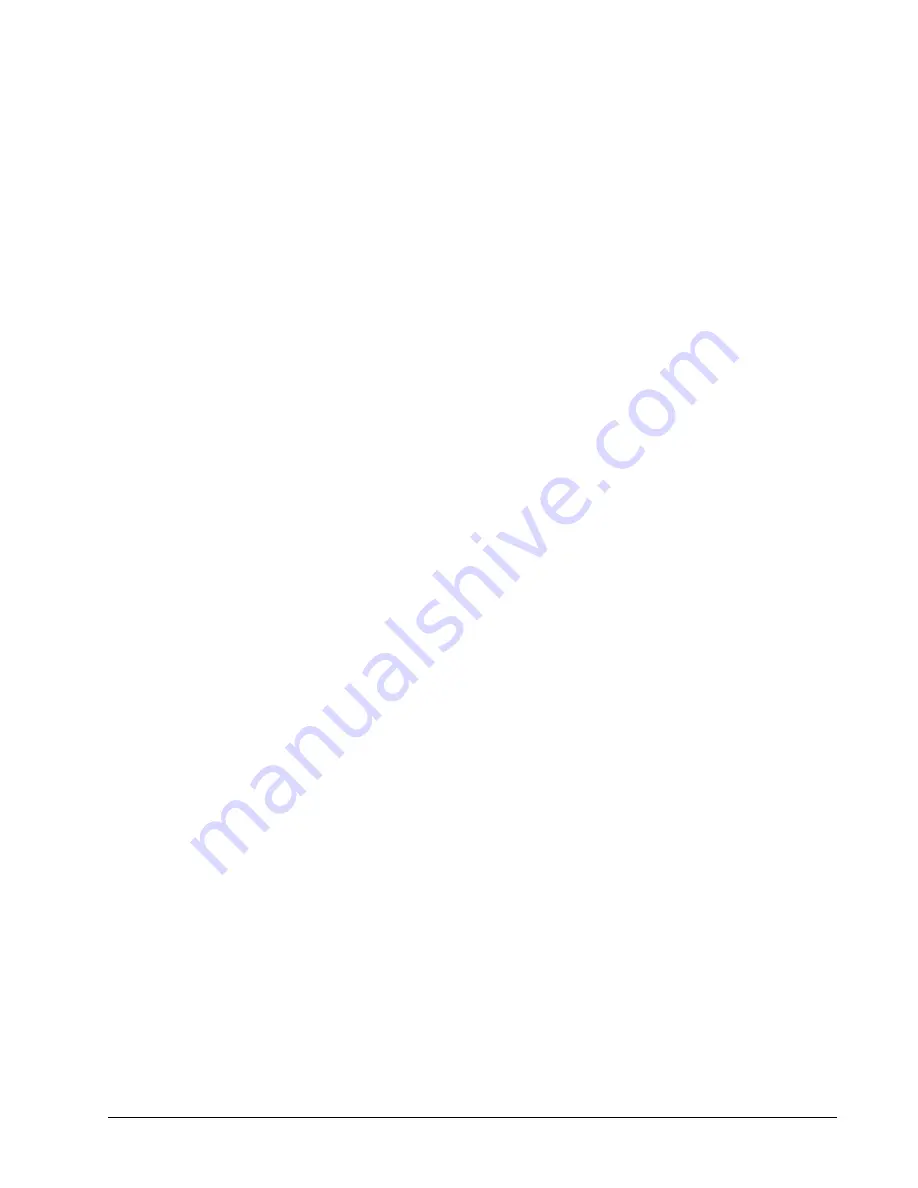
DMC-42x0 performs all the complex computations of linear and circular interpolation, freeing the host PC from this
time intensive task.
The coordinated motion mode is similar to the linear interpolation mode. Any pair of two axes may be selected for
coordinated motion consisting of linear and circular segments. In addition, a third axis can be controlled such that
it remains tangent to the motion of the selected pair of axes. Note that only one pair of axes can be specified for
coordinated motion at any given time.
The command VM m,n,p where ‘m’ and ‘n’ are the coordinated pair and p is the tangent axis (Note: the commas
which separate m,n and p are not necessary). For example, VM XWZ selects the XW axes for coordinated motion
and the Z-axis as the tangent.
Specifying the Coordinate Plane
The DMC-42x0 allows for 2 separate sets of coordinate axes for linear interpolation mode or vector mode. These
two sets are identified by the letters S and T.
To specify vector commands the coordinate plane must first be identified. This is done by issuing the command
CAS to identify the S plane or CAT to identify the T plane. All vector commands will be applied to the active
coordinate system until changed with the CA command.
Specifying Vector Segments
The motion segments are described by two commands; VP for linear segments and CR for circular segments. Once
a set of linear segments and/or circular segments have been specified, the sequence is ended with the command
VE. This defines a sequence of commands for coordinated motion. Immediately prior to the execution of the first
coordinated movement, the controller defines the current position to be zero for all movements in a sequence.
Note: This ‘local’ definition of zero does not affect the absolute coordinate system or subsequent coordinated
motion sequences.
The command, VP x,y specifies the coordinates of the end points of the vector movement with respect to the
starting point. Non-sequential axis do not require comma delimitation. The command, CR r,q,d define a circular
arc with a radius r, starting angle of q, and a traversed angle d. The notation for q is that zero corresponds to the
positive horizontal direction, and for both q and d, the counter-clockwise (CCW) rotation is positive.
Up to 511 segments of CR or VP may be specified in a single sequence and must be ended with the command VE.
The motion can be initiated with a Begin Sequence (BGS) command. Once motion starts, additional segments may
be added.
The Clear Sequence (CS) command can be used to remove previous VP and CR commands which were stored in the
buffer prior to the start of the motion. To stop the motion, use the instructions STS or AB1. ST stops motion at the
specified deceleration. AB1 aborts the motion instantaneously.
The Vector End (VE) command must be used to specify the end of the coordinated motion. This command requires
the controller to decelerate to a stop following the last motion requirement. If a VE command is not given, an
Abort (AB1) must be used to abort the coordinated motion sequence.
It is the responsibility of the user to keep enough motion segments in the DMC-42x0 sequence buffer to ensure
continuous motion. If the controller receives no additional motion segments and no VE command, the controller
will stop motion instantly at the last vector. There will be no controlled deceleration. LM? or _LM returns the
available spaces for motion segments that can be sent to the buffer. 511 returned means the buffer is empty and
511 segments can be sent. A zero means the buffer is full and no additional segments can be sent. As long as the
buffer is not full, additional segments can be sent at PC bus speeds.
The operand _CS can be used to determine the value of the segment counter.
Chapter 6 Programming Motion ▫ 67
DMC-42x0 User Manual
Summary of Contents for DMC-42 0 Series
Page 195: ...ICM 2900 PCB Layout Appendices 191 DMC 42x0 User Manual...
Page 205: ...CB 50 100 Drawings Appendices 201 DMC 42x0 User Manual...
Page 206: ...Appendices 202 DMC 42x0 User Manual...
Page 207: ...Appendices 203 DMC 42x0 User Manual...
Page 208: ...Appendices 204 DMC 42x0 User Manual...
Page 209: ...Appendices 205 DMC 42x0 User Manual...
Page 210: ...Appendices 206 DMC 42x0 User Manual...
Page 211: ...Appendices 207 DMC 42x0 User Manual...
Page 214: ...CB 50 80 Drawing Appendices 210 DMC 42x0 User Manual...