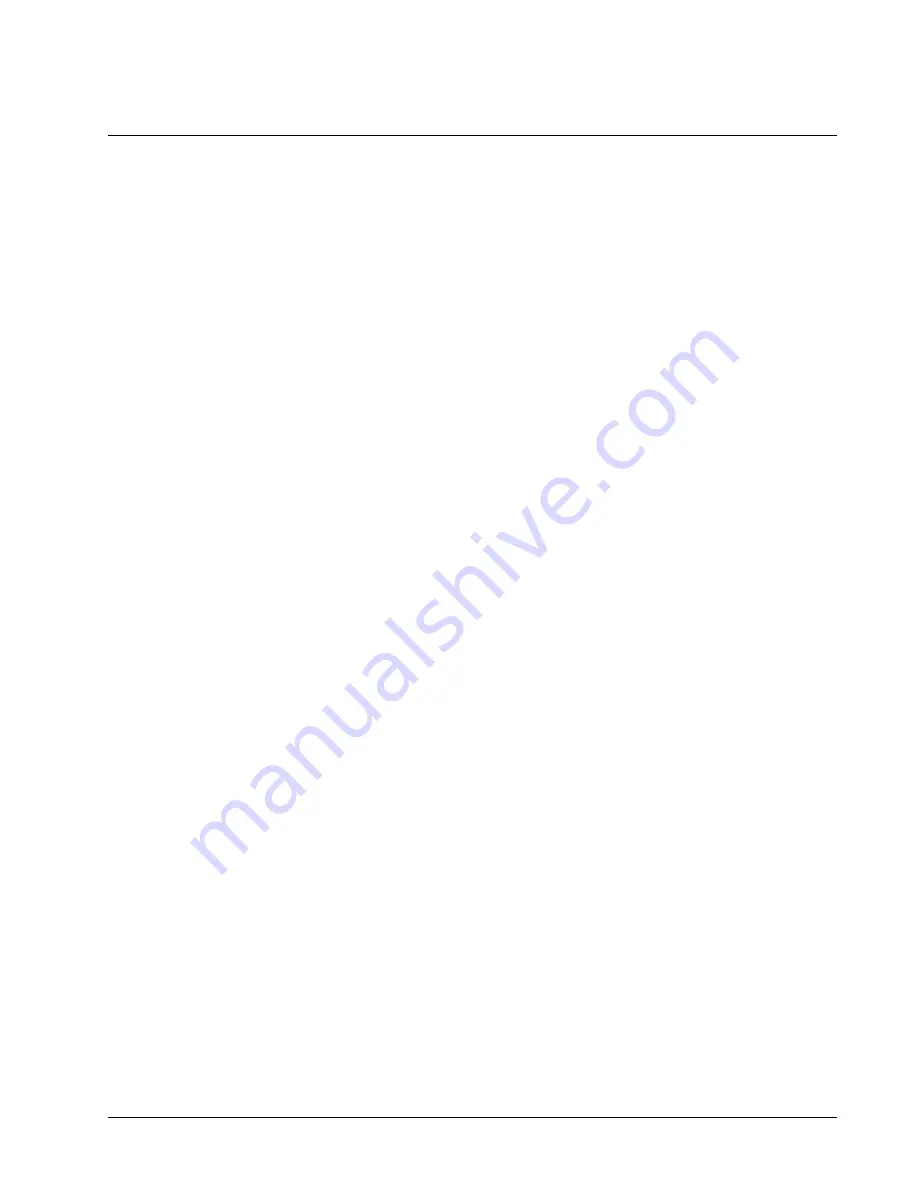
PVT Mode
The DMC-42x0 controllers now supports a mode of motion referred to as “PVT.” This mode allows arbitrary motion
profiles to be defined by position, velocity and time individually on all 8 axes. This motion is designed for systems
where the load must traverse a series of coordinates with no discontinuities in velocity. By specifying the target
position, velocity and time to achieve those parameters the user has control over the velocity profile. Taking
advantage of the built in buffering the user can create virtually any profile including those with infinite path
lengths.
Specifying PVT Segments
PVT segments must be entered one axis at a time using the PVn command. The PV command includes the target
distance to be moved and target velocity to be obtained over the specified timeframe. Positions are entered as
relative moves, similar to the standard PR command, in units of encoder counts and velocity is entered in
counts/second. The controller will interpolate the motion profile between subsequent PV commands using a 3rd
order polynomial equation. During a PV segment, jerk is held constant, and accelerations, velocities, and positions
will be calculated every other sample.
Motion will not begin until a BT command is issued, much like the standard BG command. This means that the user
can fill the PVT buffer for each axis prior to motion beginning. The BT command will ensure that all axes begin
motion simultaneously. It is not required for the “t” value for each axis to be the same, however if they are then
the axes will remain coordinated. Each axis has a 255 segment buffer. This buffer is a FIFO and the available space
can be queried with the operand _PVn. As the buffer empties the user can add more PVT segments.
Exiting PVT Mode
To exit PVT mode the user must send the segment command PVn=0,0,0. This will exit the mode once the segment
is reached in the buffer. To avoid an abrupt stop the user should slow the motion to a zero velocity prior to
executing this command. The controller will instantly command a zero velocity once a PVn=0,0,0 is executed. In
addition, a ST command will also exit PVT mode. Motion will come to a controlled stop using the DC value for
deceleration. The same controlled stop will occur if a limit switch is activated in the direction of motion. As a result,
the controller will be switched to a jog mode of motion.
Error Conditions and Stop Codes
If the buffer is allowed to empty while in PVT mode then the profiling will be aborted and the motor will come to a
controlled stop on that axis with a deceleration specified by the DC command. Also, PVT mode will be exited and
the stop code will be set to 32. During normal operation of PVT mode the stop code will be 30. If PVT mode is
exited normally (PVn=0,0,0), then the stop code will be set to 31.
Additional PVT Information
It is the users’ responsibility to enter PVT data that the system’s mechanics and power system can respond to in a
reasonable manner. Because this mode of motion is not constrained by the AC, DC or SP values, if a large velocity or
position is entered with a short period to achieve it, the acceleration can be very high, beyond the capabilities of
the system, resulting in excessive position error. The position and velocity at the end of the segment are
guaranteed to be accurate but it is important to remember that the required path to obtain the position and
velocity in the specified time may be different based on the PVT values. Mismatched values for PVT can result in
different interpolated profiles than expected but the final velocity and position will be accurate.
Chapter 6 Programming Motion ▫ 82
DMC-42x0 User Manual
Summary of Contents for DMC-42 0 Series
Page 195: ...ICM 2900 PCB Layout Appendices 191 DMC 42x0 User Manual...
Page 205: ...CB 50 100 Drawings Appendices 201 DMC 42x0 User Manual...
Page 206: ...Appendices 202 DMC 42x0 User Manual...
Page 207: ...Appendices 203 DMC 42x0 User Manual...
Page 208: ...Appendices 204 DMC 42x0 User Manual...
Page 209: ...Appendices 205 DMC 42x0 User Manual...
Page 210: ...Appendices 206 DMC 42x0 User Manual...
Page 211: ...Appendices 207 DMC 42x0 User Manual...
Page 214: ...CB 50 80 Drawing Appendices 210 DMC 42x0 User Manual...