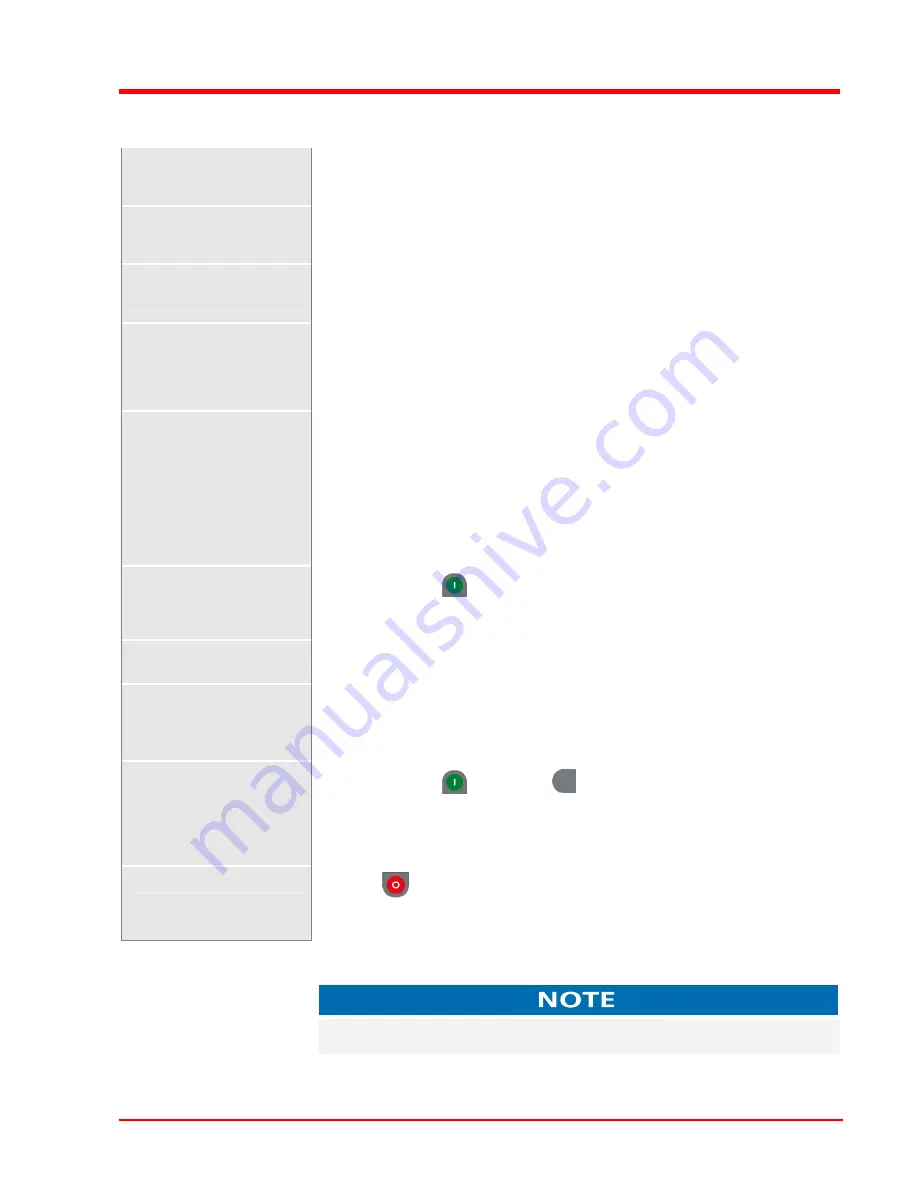
Lambdatronic P 3100 control system
Display messages
Fröling Heizkessel- und Behälterbau Ges.m.b.H, Industriestraße 12, A-4710 Grieskirchen, Austria
Page 25
Tel +43 (0) 7248 606-0 Fax +43 (0) 7248 606-600 [email protected] www.froeling.com
B0190806
4
4.2.1
Modes
Winter operation
The boiler controls the heating and hot water heating according to the timed
program settings. There is no reduction in temperature
the boiler stays at
the same temperature and maintains a constant burn.
Summer operation
Systems without storage
The boiler only controls the hot water heating according to the timed program
settings. There is no reduction in performance
the boiler switches to “Burner
Off”.
Summer operation
Systems with stores
The boiler regulates domestic hot water (DHW) heating according to the DHW
tank loading times, which have been set. After heating the domestic hot water,
the boiler switches to “Burner Off”.
Transitional operation
Systems without storage
The boiler produces heat during the specified heating phases (“Boiler times”
menu). Heating and hot water are regulated according to the specified times
(heating times, DHW tank loading times). There is no reduction in temperature
the boiler stays at the same temperature and maintains a constant burn.
When the heating phase ends, the boiler switches to “Burner Off”.
Transitional operation
Systems with stores
If the temperature falls below the “Store up min. temp.”, the boiler is turned on
within the specified store loading times. If the store is fully loaded, the boiler
switches to “Burner Off”. When the parameter “End of 1st or 2nd store loading”
is reached, the boiler also switches to “Burner Off”, even if the store is not fully
loaded.
NOTE: Set a sufficiently large time window (00:00 to 24:00 means that as soon
as the value falls below the parameter “Storage up min” the store is
immediately fully loaded)
NOTE: This is an ideal operating method for systems with storage tanks
Extra heating
Press and hold the
key for 5 seconds:
The controls are set to “Override”: the boiler switches on for 4 hours; hot water
heating and heating circuit regulation are active.
Firewood operation
This mode is for emergency firewood operation. The pellet feeding system is
deactivated.
Cleaning
The boiler turns off the combustion system as directed (“Burner Off” status)
Then the ID fan, combustion air fan, heat-exchanger system and ash screw are
controlled according to the program.
After the cleaning has finished, reset to original mode.
Chimney sweeper
Press and hold the
key and the
BACK
key for 5 seconds
The chimney sweeper program for boiler measurement is started.
The system is operated for 30 minutes at nominal load. For this aim the
maximum boiler temperature, the maximum heating circuit flow temperature
and the DHW tank loading are released.
Switched off
Press the
key
The boiler turns off following the shutdown routine. The system now only
regulates the connected heating components
For systems with a storage tank, always select transitional operation!