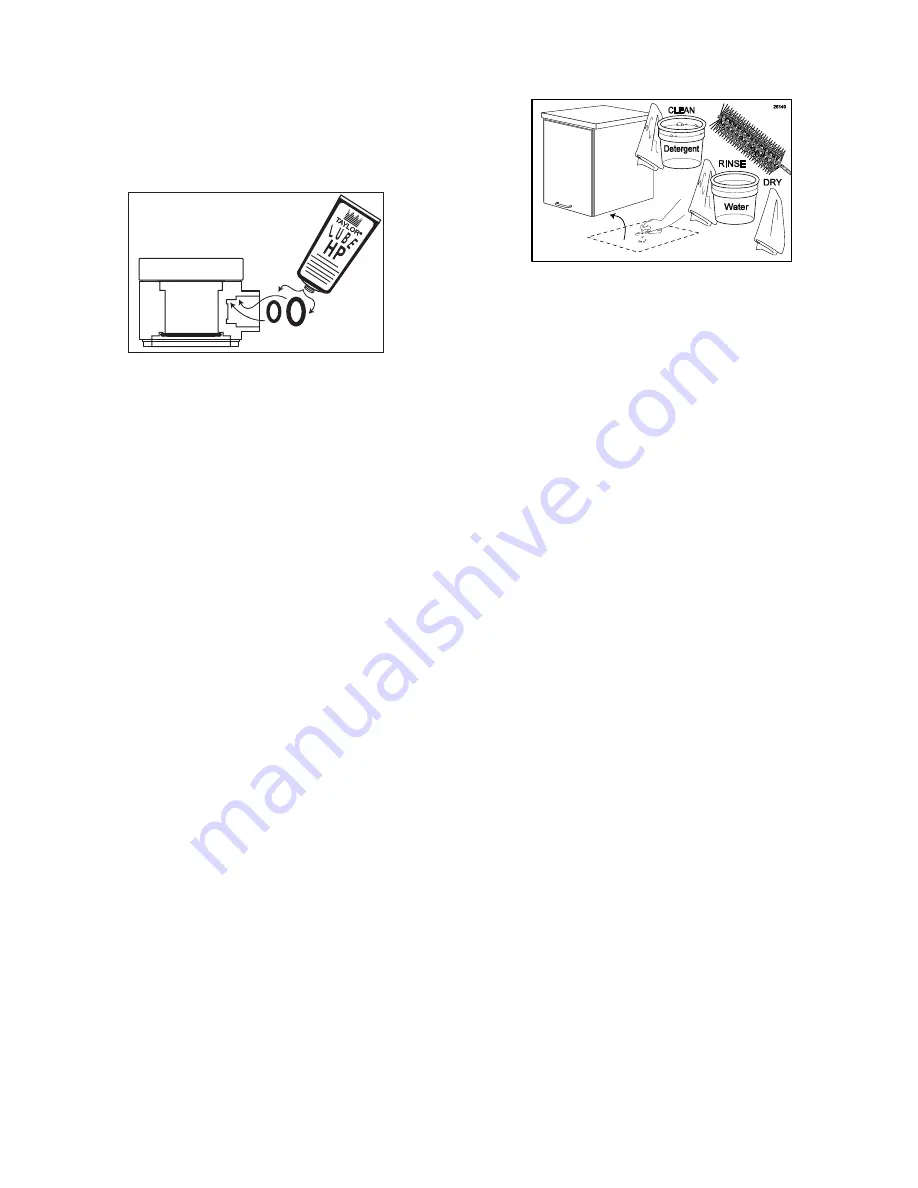
43
7. Apply Taylor HP Lubricant to the two syrup
port o-rings and then place them into their
respective places inside the syrup port. A
small tool may be used to ensure the
o-rings are fully seated in the grooves.
(See Figure 107.)
26021
Figure 107
NOTE:
O-RINGS MUST BE COMPLETELY
SEATED TO PREVENT LEAKAGE.
Miscellaneous Cleaning Procedures
The following cleaning procedures do not need
to be performed on a daily basis. Inspect these
areas periodically and clean when necessary
according to instructions.
Cleaning the Area Under the Cabinet
Figure 108
1. Prepare detergent water by mixing
McD
ALL PURPOSE SUPER CONCENTRATE
(APSC) (HCS)
with warm water according
to manufacturer’s instructions.
NOTE:
DO NOT USE AN EXCESSIVE
AMOUNT OF WATER OR DETERGENT IN
CLEANING THE OUTSIDE OF THE CABINET.
2. Carefully move the cabinet to an area
outside of where it was sitting.
3. Clean the area using a single service towel
moistened with warm detergent water. Use
a Large Brush if necessary.
4. Rinse area with a single service towel and
clean, warm water and then wipe dry with a
dry single service towel.
5. Clean the outside and underside of the
cabinet using detergent, water and single
service towels.
6. Carefully return the cabinet to its original
place.
Summary of Contents for FB 80M Series
Page 2: ......
Page 7: ...5 General System Overview 26000 13 2 1 3 5 6 15 14 10 8 11 12 9 7 17 16 4 Figure 1...
Page 9: ...7 Outer Cabinet 3 1 2 12 10 7 13 4 5 9 8 6 11 26001 Figure 2...
Page 11: ...9 Inner Cabinet 26002 15 11 13 16 14 11 12 1 9 2 6 6 11 18 19 16 4 5 8 3 4 17 11 10 7 Figure 3...
Page 22: ...20...
Page 34: ...32...
Page 50: ...48...
Page 66: ...64...
Page 72: ...70...
Page 82: ...80 WIRING DIAGRAM Figure 203...
Page 83: ...81...
Page 84: ...82 063285 M...