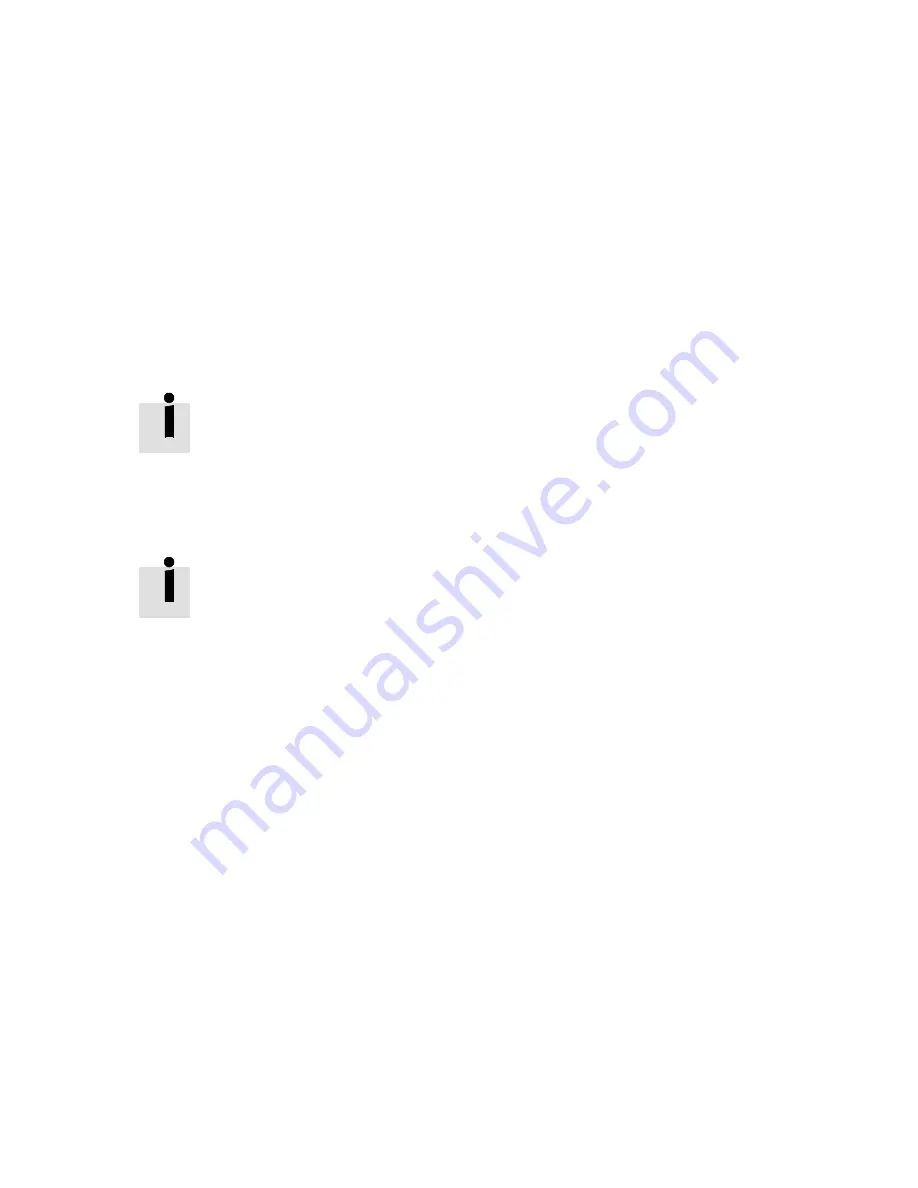
Installation
VII
Festo P.BE-CTEU-CO-OP+MAINT-EN en 1101NH
Notes on this manual
This manual is Part II of the complete product documentation
and contains specific information about the configuration,
parameterisation, commissioning, programming and
diagnostics of the bus node with the CANopen fieldbus
protocol.
Information relating to installing the bus node can be found in
Part I of the product documentation entitled “Installation and
Interface manual”, which is supplied with the bus node.
Information for mounting the bus node on the CAPC… electric
sub-base can be found in the assembly instructions supplied
with the electric sub-base.
Information about other bus nodes and components of the
CTEU… product family can be found in the user documenta-
tion for the respective product.
Summary of Contents for CTEU-CO
Page 2: ......
Page 14: ...Installation XII Festo P BE CTEU CO OP MAINT EN en 1101NH ...
Page 15: ...Commissioning 1 1 Festo P BE CTEU CO OP MAINT EN en 1101NH Chapter 1 Commissioning ...
Page 37: ...Diagnosis 2 1 Festo P BE CTEU CO OP MAINT EN en 1101NH Chapter 2 Diagnosis ...
Page 51: ...Error treatment 3 1 Festo P BE CTEU CO OP MAINT EN en 1101NH Chapter 3 Error treatment ...
Page 58: ...3 Error treatment 3 8 Festo P BE CTEU CO OP MAINT EN en 1101NH ...
Page 59: ...Technical appendix A 1 Festo P BE CTEU CO OP MAINT EN en 1101NH Appendix A Technical appendix ...
Page 74: ...A Technical appendix A 16 Festo P BE CTEU CO OP MAINT EN en 1101NH ...
Page 75: ...Index B 1 Festo P BE CTEU CO OP MAINT EN en 1101NH Appendix B Index ...
Page 76: ...B Index B 2 Festo P BE CTEU CO OP MAINT EN en 1101NH Contents B Index B 1 ...