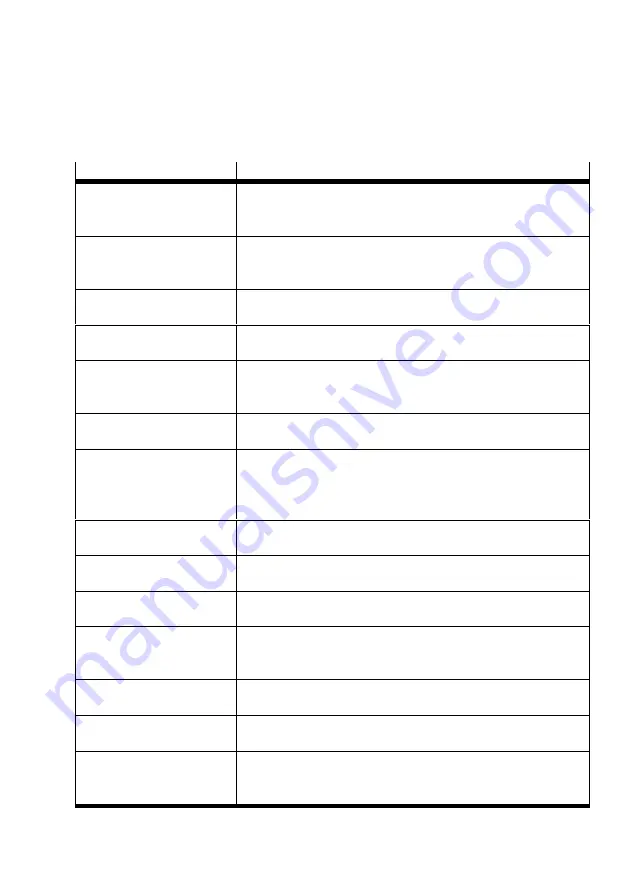
E
Terms and abbreviations
Festo – GDCP-CMMO-ST-LK-C-HP-EN – 2017-05b – English
179
E
Terms and abbreviations
The following terms and abbreviations are used in this description.
You can find fieldbus-specific terms and abbreviations in the respective chapter.
Term/abbreviation
Significance
Axis
Mechanical component of a drive that transfers the drive force for
the movement. An axis enables the attachment and guiding of the
effective load and the attachment of a reference switch.
Axis zero point (AZ)
Point of reference of the software end positions and project zero
point. The axis zero point AZ is defined by a preset distance (offset)
from the reference point REF.
Controller
Programmable logic controller; short: controller (also IPC: industrial
PC).
Drive
Complete actuator, consisting of motor, encoder and axis, optionally
with gear unit, if necessary with motor controller.
Encoder
Electrical pulse generator (usually a rotor position encoder). The
motor controller evaluates the generated electrical signals and cal
culates from this the position and speed.
Enhanced Festo Parameter
Channel (EFPC)
Extended function of the Festo Parameter Channel (FPC), e.g. for
transmission of parameter files.
Festo Configuration Tool (FCT)
Software with uniform project and data management for supported
types of equipment. The special requirements of a device type are
supported with the necessary descriptions and dialogues by means
of plug-ins.
Festo Handling and Position
ing Profile (FHPP)
Uniform fieldbus data profile for position controllers from Festo
Festo Parameter Channel
(FPC)
Parameter access according to the “Festo Handling and Positioning
Profile” (I/O messaging, optionally additional 8 bytes I/O)
FHPP standard
Defines the sequence control in accordance with the “Festo Hand
ling and Positioning Profile” (I/O messaging 8 bytes I/O)
Force/torque mode
(Profile Torque Mode)
Operating mode for execution of a direct positioning task with force
control (open loop transmission control) through regulation of the
motor current.
Homing run
Positioning procedure in which the reference point and therefore the
origin of the measuring reference system of the axis are defined.
Homing
(Homing mode )
Operating mode for determining the measurement reference system
of the axis.
Jogging
Manual travel in a positive or negative direction.
Function for setting positions by approaching the target position,
e.g. when teaching position sets (Teach mode).
Summary of Contents for CMMO-ST-C5-1-LKP
Page 182: ......