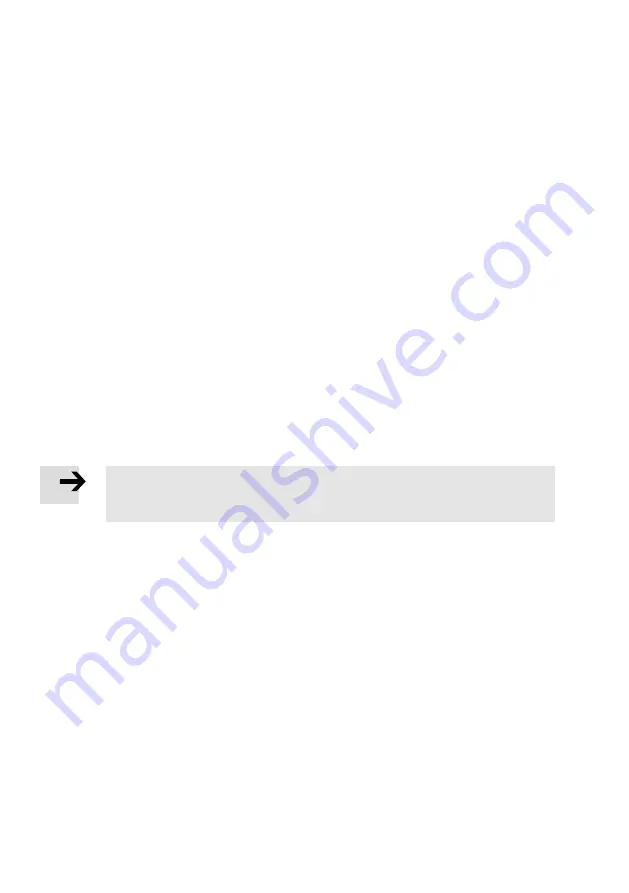
2
Product description for safety module CAMC-G-S1
18
Festo – GDCP-CAMC-G-S1-EN – 1412b – English
2.2.6
Status display
To display the status of the safety function, the safety module has an LED on its front
è
The status LED displays the module’s operating state (green = STO inactive, yellow = STO active). The
display corresponds to the state of the feedback contact C1/C2.
2.2.7
DIP switch
Located on the front of the safety module are DIL switches. These switches have no safety function. The
meaning of the individual switches depends on the interface used for the fieldbus communication.
The fieldbus communication can be activated/deactivated and a station address can be set, for exam
ple, via the DIL switches.
2.3
Functionalities in motor controller CMMP-AS-...-M3
The following functions in motor controller CMMP-AS-...-M3 are not certified to EN 61800-5-2. They are
functional supplements and offer additional diagnostics options.
Error messages generated by the safety module, such as exceeding the discrepancy time, are detected
and analysed by the non-safety finite state machine of the motor controller. If conditions for an error
status are detected, an error message is generated. In this case, it cannot always be guaranteed that
power end stage has been safely switched off.
The safety module CAMC-G-S1 controls only the provisioning of the driver supply for the motor con
troller CMMP-AS-…-M3. Although input voltage levels are monitored area by area, the safety module
does not have its own error analysis function and is unable to display errors.
Note
When error messages are acknowledged, all acknowledgeable errors regarding
functional safety are also always acknowledged
è
The motor controller CMMP-AS-M3 monitors the status of the control ports STO-A and STO-B.
Consequently, the motor controller firmware detects the request for the safety function STO (Safe
Torque Off ) and various non-safety functions are then performed:
–
Detection of deactivated driver supply for the power semiconductor via the safety module,
–
Deactivation of the drive controller and activation of the power semiconductor (PWM),
–
The holding brake controller is deactivated (if configured),
–
Finite state machine on the motor controller with activation analysis (discrepancy time),
–
Detection of application-related error messages,
–
Hardware diagnostics,
–
Status and error display via display, digital outputs, fieldbuses etc.