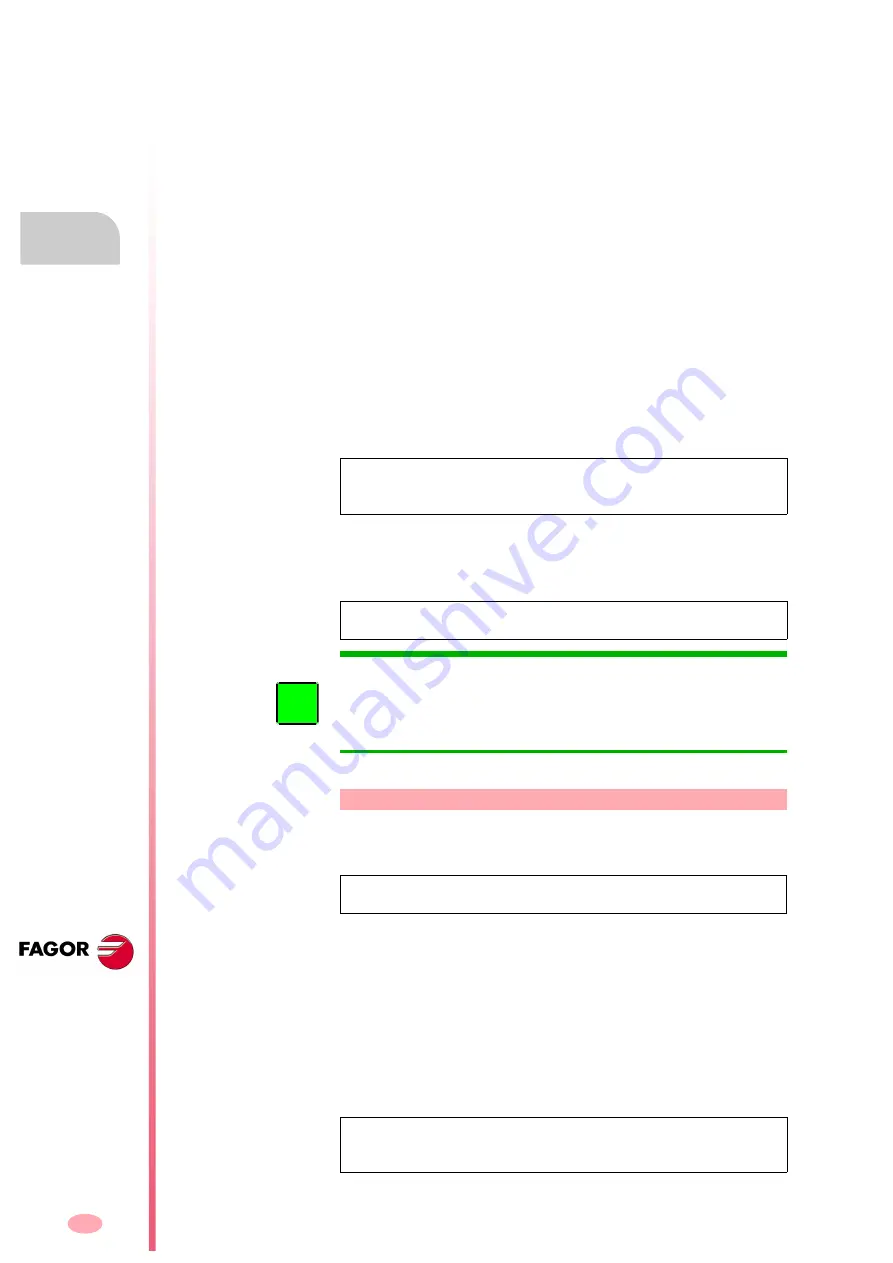
Installation
312
8.
INSTAL
LAT
ION
C
onne
cti
on
of the
con
trol
a
nd
communica
tions
signa
ls
302
DDS
HARDWARE
Ref.1310
CAN bus connection
The ISO 11898 CAN interface is an international standard for digital
communications between CNC's and servo drives of CNC machines. The
communication protocol is CanOpen according to EN 50325-4.
The CAN communication bus integrates several functions:
It carries the velocity command from the CNC to the drive in digital for-
mat with greater accuracy and immunity against outside disturbances.
It carries the feedback signal from the drive to the CNC.
It communicates the errors and manages the basic control signals of
the drive (enables).
It allows setting, monitoring and diagnosis of the parameters from the
CNC with simple and standard procedures.
Its open standard structure provides compatibility between CNC's and ser-
vo systems from different manufacturers on the same machine.
The different drive modules and the CNC are connected through CAN con-
nector (X6) carried by each drive of the FAGOR catalog (see their front
panel) through the CAN cable. See chapter
in this manual .
It is a tree type connection where the 16-position rotary switch (0-15) of
each drive permits selecting the address of each module integrated in it.
Particular
Differentiate each drive with the 16-position rotary switch “NODE SELECT”
with sequential numbers starting from 1.
If a drive is assigned the 0 identifier, the module will be ignored.
For example, a machine has four servo drives identified as 1, 2, 3 and 4.
To ignore the second one, another one must be renamed so they are con-
secutive. The easiest solution for a situation like this will be 1, 0, 3 and 2.
Interconnection
Connect in the CAN field bus all the drives that will be governed by the
CNC.
Use the CAN cable to connect the first drive to the adjacent one (this
one will then be the second drive) through their X6 connectors.
Repeat this procedure with the second drive and so on up to the last
drive.
Use a CAN cable to connect the X6 connector of the first drive to the
CAN connector of the CNC model being used.
NOTE.
Remember that it is not possible to use both SERCOS and CAN
interfaces at the same time. The hardware can only be used with one of
the two boards in the drive.
NOTE.
The module must be reset in order for any change made on the
rotary switch to be effective.
INFORMATION.
The DRIBUSID parameters of the CNC must have the
same ID numbers as the ones assigned by means of the Node_Select
switch. See figure
.
If the same motor is to be used as C axis and spindle, the two CNC tables
must have the same value for the DRIBUSID parameter.
i
Example.
NOTE.
Remember that
the DRIBUSID parameters of the CNC can also
be modified the same way.
NOTE.
Note that the CAN cable is supplied without connectors. Before
connecting it, put the cable and connectors together as indicated in figure
Summary of Contents for DDS
Page 1: ...DRIVE DDS Hardware manual Ref 1310...
Page 6: ...I 6 DDS HARDWARE Ref 1310...
Page 9: ......
Page 10: ......
Page 11: ......
Page 12: ......
Page 16: ...16 Ref 1310 DDS HARDWARE...
Page 30: ...1 DESCRIPTION 30 Description DDS HARDWARE Ref 1310...
Page 94: ...2 POWER SUPPLIES 94 Power supplies DDS HARDWARE Ref 1310...
Page 188: ...3 DRIVE MODULES 188 Drive modules DDS HARDWARE Ref 1310...
Page 204: ...4 AUXILIARY MODULES 204 Auxiliary modules DDS HARDWARE Ref 1310...
Page 232: ...SELECTING CRITERIA 5 232 Selection criteria DDS HARDWARE Ref 1310...
Page 266: ...7 CABLES 266 Cables DDS HARDWARE Ref 1310...
Page 312: ...8 INSTALLATION 312 Installation DDS HARDWARE Ref 1310...
Page 326: ...9 FUNCTIONAL SAFETY 326 Functional safety DDS HARDWARE Ref 1310...
Page 354: ...10 CONNECTION DIAGRAMS 354 Connection diagrams DDS HARDWARE Ref 1310...
Page 378: ...12 SALES REFERENCES 378 Sales references DDS HARDWARE Ref 1310...
Page 384: ...13 COMPATIBILITY 384 Compatibility DDS HARDWARE Ref 1310...
Page 385: ......