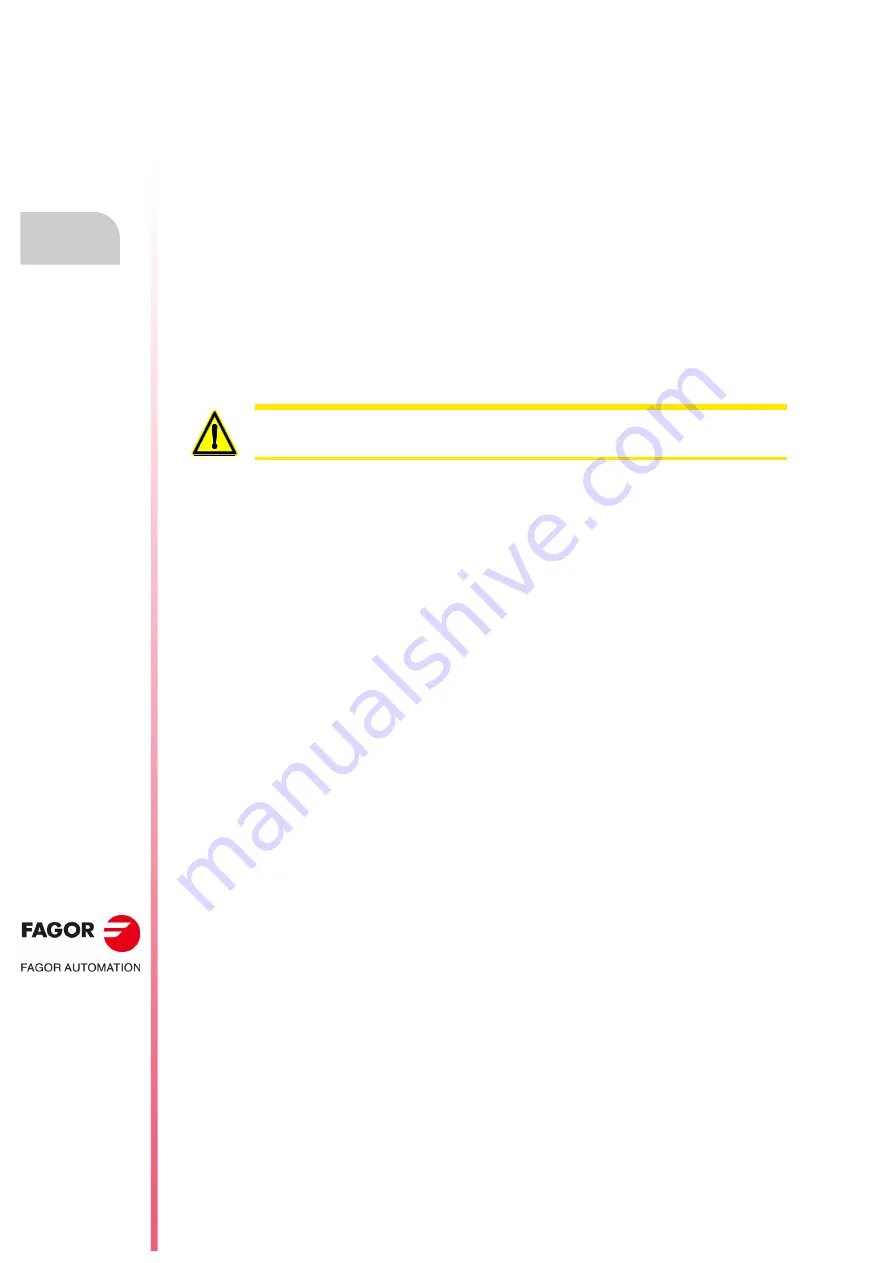
·80·
Programming manual
CNC 8055
CNC 8055i
5.
ISO CODE
PR
OGRAMMING
·M· & ·EN· M
ODELS
S
OFT
: V02.2
X
Au
xilia
ry function
(M)
• Auxiliary spindle: PLCM45 (M5076) to stop the auxiliary spindle and PLCM45S (M5077) to start
it up.
The PLC activates these marks to indicate to the CNC that it must execute the corresponding M
function at the indicated spindle.
If that spindle is not the main spindle at that moment, it changes the M in the execution history, it
activates the corresponding PLC mark DM3/4//5 and executes the transfer with the PLC (it writes
the M number in the MBCD1 (R550) register, it activates the MSTROBE signal, it waits for the
AUXEND signal to go up and it cancels the MSTROBE signal; if the M function is set as not to wait
for AUXEND in the M function table, it waits for the time period set with MINAENDW and cancels
the MSTROBE).
When acting upon the secondary spindle, it executes the same operation, but having activated the
mark S2MAIN (M5536) first and then cancelling it at the end. This operation is done automatically;
i.e. there is no need to program it at the PLC.
Even if the M3, M4 or M5 function has an associated subroutine in the M function table, that
subroutine will not be executed when they are executed using the PLC marks.
When executing M3, M4 or M5 using the PLC marks, the gear change that could be required by
the new S is not output to the PLC even if the gear change is automatic.
The CNC will admit the M functions from the PLC as long as it is not in an error state or with LOPEN
(M5506) high, whether there is an execution active or not, either in manual or automatic. If the M
function is executed during a tool inspection and the spindle turning direction is changed, the change
will be identified in repositioning and it will offer the choice to change it again.
If when activating the M3, M4 or M5 marks via PLC, the main channel is transferring something to
the PLC, the PLC keeps the mark active until the CNC can attend to it. Once the M function is
executed, the CNC deactivates the mark.
In the following cases, the CNC ignores these PLC marks and deletes the mark so the request is
not left as pending:
• When the spindle is threading in electronic threading (G33).
• When it is doing a rigid tapping or a regular tapping.
• When the CNC is in error state or when LOPEN (M5506) is high.
If several marks of different spindles are activated at the same time, the below order will be followed:
first the first spindle, then the second spindle and finally the auxiliary spindle.
When receiving contradictory marks, they will all be ignored. When receiving several marks at the
same time and there is a stop (PLCM5 / PLCM45) between them, only this will be considered and
the rest will be ignored and not saved.
If the spindle has M19TYPE=1, the spindle is homed with the first M3 or M4 after start-up, as long
as that M function is executed in manual or automatic mode. If the M function is executed using one
of the PLC marks, the spindle will not be homed.
When activating the PLC marks while homing the spindle, the PLC command stays waiting for the
homing operation to be over. If the home search is associated with the first M3 or M4 after start-
up, the PLC command stays waiting for the homing operation is over.
If there are synchronized spindles, it acts upon the command of the main and secondary spindles
at the same time.
While executing the M function, it is possible to abort the process by deactivating the PLC mark that
has initiated it.
Note:
The PLCM5 mark is used to handle the open-door safety operation defined by Fagor Automation.
If the CNC is started up with no gear being active yet, because no M3 or M4 has been executed in
the main channel, the CNC will issue an error message even if it has been configured as AUTOGEAR.
Summary of Contents for 8055 EN
Page 1: ...CNC 8055 M EN Programming manual Ref 1711 Soft V02 2x...
Page 8: ...8 Programming manual CNC 8055 CNC 8055i SOFT V02 2X...
Page 12: ...12 CNC 8055 CNC 8055i Declaration of conformity and Warranty conditions...
Page 16: ...16 CNC 8055 CNC 8055i Version history...
Page 22: ...22 CNC 8055 CNC 8055i Returning conditions...
Page 24: ...24 CNC 8055 CNC 8055i Additional notes...
Page 26: ...26 CNC 8055 CNC 8055i Fagor documentation...
Page 448: ......
Page 464: ...464 Programming manual CNC 8055 CNC 8055i D M EN MODELS SOFT V02 2X Key code...
Page 466: ...466 Programming manual CNC 8055 CNC 8055i D M EN MODELS SOFT V02 2X Key code MC operator panel...
Page 467: ...Programming manual CNC 8055 CNC 8055i D M EN MODELS SOFT V02 2X 467 Key code...
Page 468: ...468 Programming manual CNC 8055 CNC 8055i D M EN MODELS SOFT V02 2X Key code...
Page 471: ...Programming manual CNC 8055 CNC 8055i D M EN MODELS SOFT V02 2X 471 Key code 11 LCD Monitor...
Page 472: ...472 Programming manual CNC 8055 CNC 8055i D M EN MODELS SOFT V02 2X Key code...
Page 478: ...478 Programming manual CNC 8055 CNC 8055i F M EN MODELS SOFT V02 2X Maintenance...
Page 479: ...Programming manual CNC 8055 CNC 8055i F SOFT V02 2X 479...
Page 480: ...480 Programming manual CNC 8055 CNC 8055i F SOFT V02 2X...
Page 481: ......