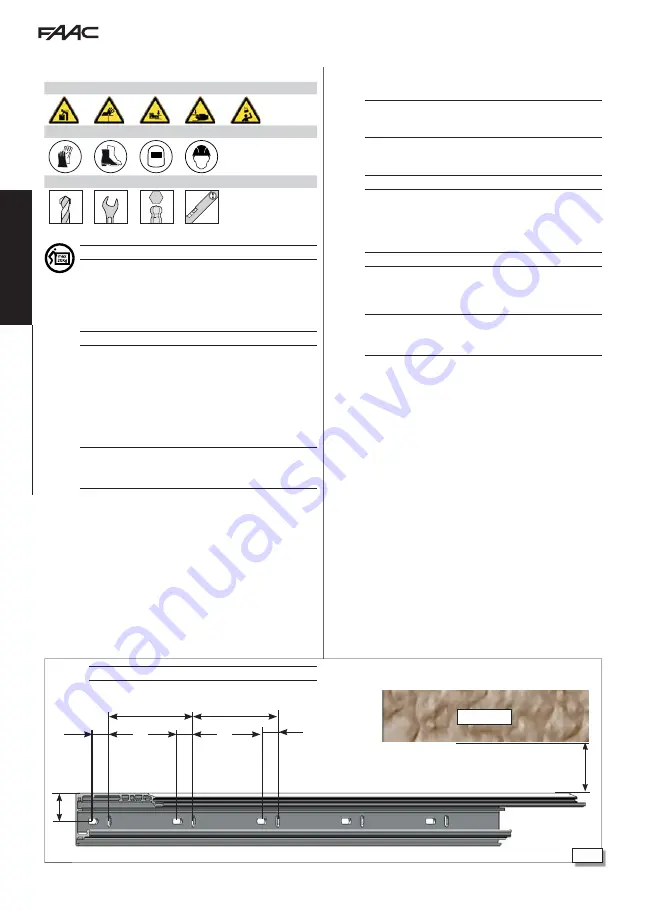
A1000
28
532210 04 - Rev.A
37,5
37,5
37,5
38
25
8
0
80
Tr
ansla
tion of the original instruc
tions
ENGLISH
8. INSTALLING THE HEAD SECTION
ceiling
Screws and dowels not supplied.
8.2 FASTENING TO THE WALL
!
The supporting wall must be adequate for the weight of the entry door
(automation with leaves). It is recommended to use dowels with adequate
screws and tightening torque.
1. Lift the support profile to the established fastening height.
2. Mark the drilling points on the wall.
!
Check the horizontal with a spirit level.
3. Drill the holes on the wall.
-
Use suitable drill bits for the wall material.
4. Lift the support profile. Start fastening at a vertical slot at one end
and a horizontal slot at the other end.
!
Check the horizontal with a spirit level.
5. First fasten it in the centre and then fasten it at the other points,
alternating vertical and horizontal slots at a distance of 200 mm
25
.
Upon completing head section installation, reposition the components you
have moved and reassemble the electronics module in the correct position.
Finally, fit again the safety cables and the casing.
RISKS
PERSONAL PROTECTIVE EQUIPMENT
REQUIRED TOOLS
Ø 8 mm
8-10-13
5
For manual lifting, there should be 1 person for every 20 kg to be lifted.
8.1 PRELIMINARY OPERATIONS
1. To be able to perform fastenings, the casing and electronics mod-
ule must be temporarily disassembled and the components must
be moved as they are a hindrance.
To make subsequent replacing easier, mark components’ positions.
-
With the automation on the ground, extract the safety cables
and remove the casing.
-
Loosen the screws of the electronics module and remove it.
-
Loosen the screws of the components that are a hindrance (e.g.
motors) and slide them along the profile.
2. Establish the fastening height of the support profile:
see installation diagrams
102
103
104
!
The minimum distance between the top of the support profile and the
ceiling must be 80 mm
80 mm
25
.
Check the horizontal with a spirit level.
3. Proceed according to the intended type of installation.
Summary of Contents for A1000
Page 1: ...A1000 EN16005 2012 E1SL fw 3 0 SDK EVO fw 3 0 LK EVO fw 1 2...
Page 108: ...A1000 108 53221004 Rev A Translation of the original instructions ENGLISH...
Page 110: ...A1000 110 53221004 Rev A...
Page 114: ...A1000 114 53221004 Rev A...
Page 115: ...Translation of the original instructions ENGLISH...