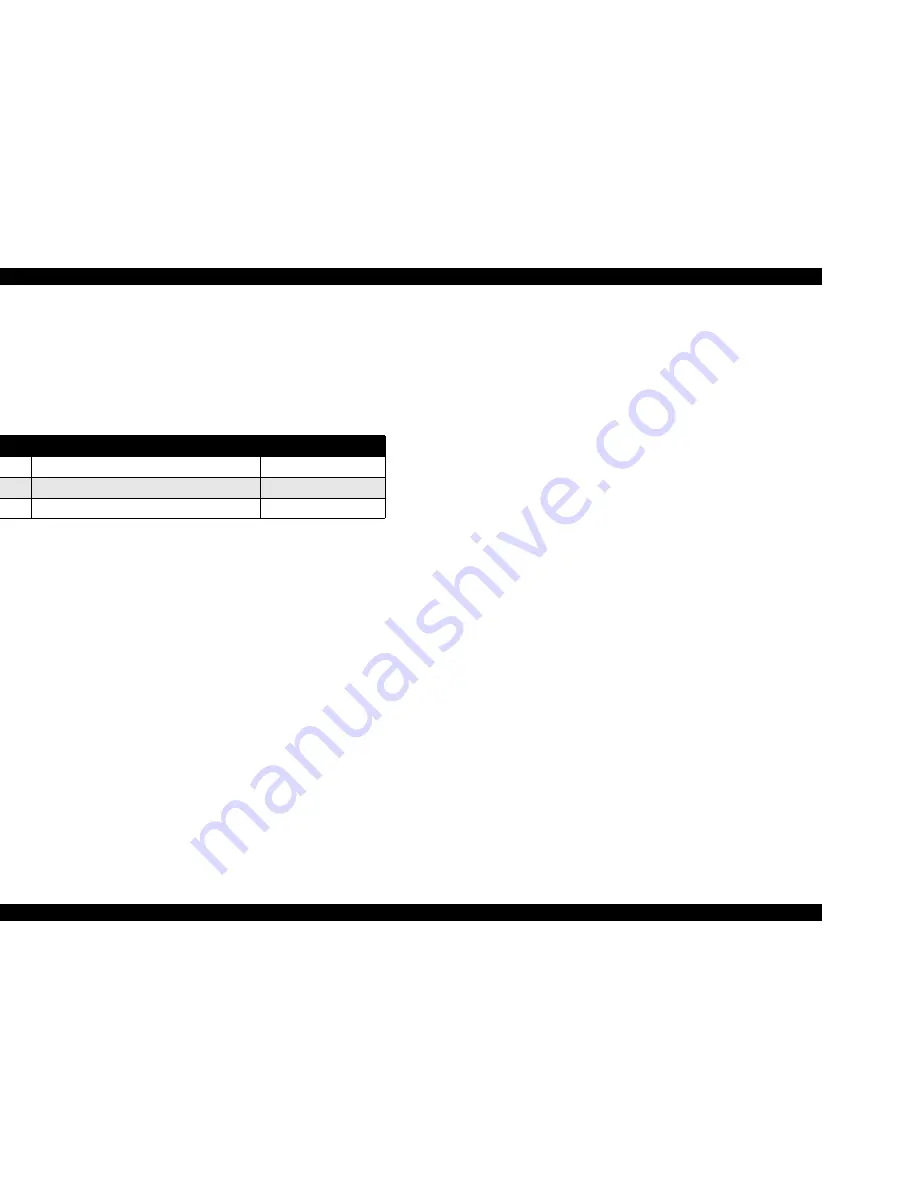
EPSON Stylus COLOR 760
Revision C
Troubleshooting
Overview
67
3.1.3 Isolating the Faulty Part according to the Phenomenon
Refer to this section if you could not solve the problem in Section 3.1.1
or Section 3.1.2 or need more information to isolate the cause
according to the exhibited phenomenon. The contents mostly cover the
problems relating to the C298 and their remedies.
Table 3-12. Phenomens Exhibited
No.
Phenomenon Exhibited
Table to refer to
1
CR motor does not rotate.
Table 3-13
2
PF motor does not rotate.
Table 3-14
3
Cleaning does not solve the print problem.
Table 3-15
Summary of Contents for Stylus Color 760
Page 1: ...EPSONStylusCOLOR760 Color ink jet printer SEIJ99004 SERVICE MANUAL ...
Page 8: ...C H A P T E R PRODUCTDESCRIPTION ...
Page 27: ...C H A P T E R OPERATINGPRINCIPLES ...
Page 53: ...C H A P T E R TROUBLESHOOTING ...
Page 72: ...C H A P T E R DISASSEMBLYANDASSEMBLY ...
Page 109: ...C H A P T E R ADJUSTMENT ...
Page 142: ...C H A P T E R MAINTENANCE ...
Page 152: ...APPENDIX C H A P T E R ...