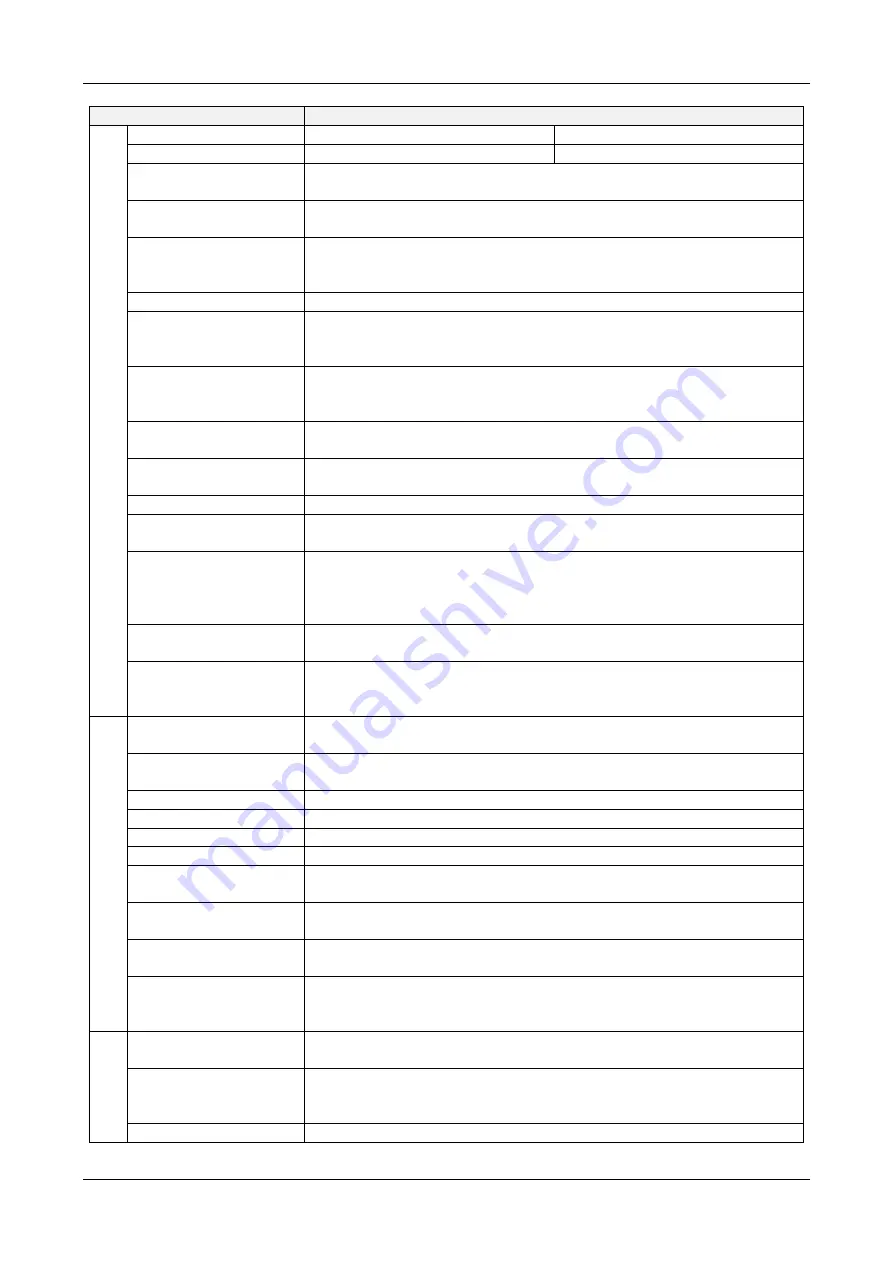
EM12 User’s Manual
2. Product Information
7
Item
Specifications
Speed stability accuracy ± 0.5% (SVC)
± 0.02% (FVC)
Torque control accuracy ± 10% (SVC)
± 5% (FVC)
Overload capacity
G type: 60s for 150% of the rated current, 3s for 180% of the rated current
P type: 60s for 120% of the rated current, 3s for 150% of the rated current
Torque boost
Auto boost
Manual boost 0.1%~30.0%
V/F curve
Straight-line V/F curve
Multi-point V/F curve
N-power V/F curve (1.2-power, 1.4-power, 1.6-power, 1.8-power, square)
V/F separation
Two types: complete separation; half separation
Acceleration/deceleration
curve
Straight-line ramp
S-curve ramp
Four groups of acceleration/deceleration time with the range of 0.0s~65000s
DC braking
DC braking frequency: 0.00 Hz ~ maximum frequency
Braking time: 0.0s~36.0s
Braking trigger current value: 0.0%~100.0%
JOG control
JOG frequency range: 0.00Hz~50.00 Hz
JOG acceleration/deceleration time: 0.00s~6500.0s
Built-in simple PLC,
multiple speeds
It realizes up to 16 speeds via the simple PLC function or combination of DI
terminal states.
Built-in PID
It realizes closed loop control system easily.
Auto voltage regulation
(AVR)
It can keep constant output voltage automatically when the mains voltage
fluctuation.
Overvoltage/ Over current
stall control
The current and voltage are limited automatically during the running process
so as to avoid frequently tripping due to overvoltage / over current.
Rapid current limit
function
It can auto limit running current of frequency inverter to avoid frequently
tripping.
Torque limit and control
(Excavator characteristics) It can limit the torque automatically and prevent
frequently over current tripping during the running process.
Torque control can be implemented in the VC mode.
Indi
v
idua
liz
ed func
ti
o
ns
High performance
Control of asynchronous motor and synchronous motor are implemented
through the high-performance current vector control technology.
Instant power off not stop
The load feedback energy compensates the voltage reduction so that the
frequency inverter can continue to run for a short time.
Rapid current limit
To avoid frequently over current faults of the frequency inverter.
Virtual I/O
Five groups of virtual DI/DO can realize simple logic control.
Timing control
Time range: 0.0~6500.0 minutes
Multi-motor switchover Two motors can be switched by two groups of motor parameters.
Multiple communication
protocols
It supports communication bus via Modbus-RTU, PROFIBUS-DP, CANlink
and CANopen.
Motor overheat protection
The optional I/O extension card enables AI3 to receive the motor temperature
sensor input (PT100, PT1000) so as to realize motor overheat protection.
Multiple encoder types
It supports various encoders such as differential encoder, open-collector
encoder, resolver, UVW encoder, and SIN/ COS encoder.
Advanced background
software
It supports the operation of frequency inverter parameters and virtual
oscillograph function, by which the state of frequency inverter can be
monitored.
RUN
Running command giving
key panel; Control terminals; Serial communication port; You can switch
between these giving in various ways.
Frequency giving
There are 10 kinds frequency giving: digital setting, analog voltage setting,
analog current setting, pulse setting and serial communication port setting.
You can switch between these giving in various ways.
Auxiliary frequency giving There are 10 kinds auxiliary frequency giving. It can implement tiny tuning of
Summary of Contents for EM12 Series
Page 5: ......