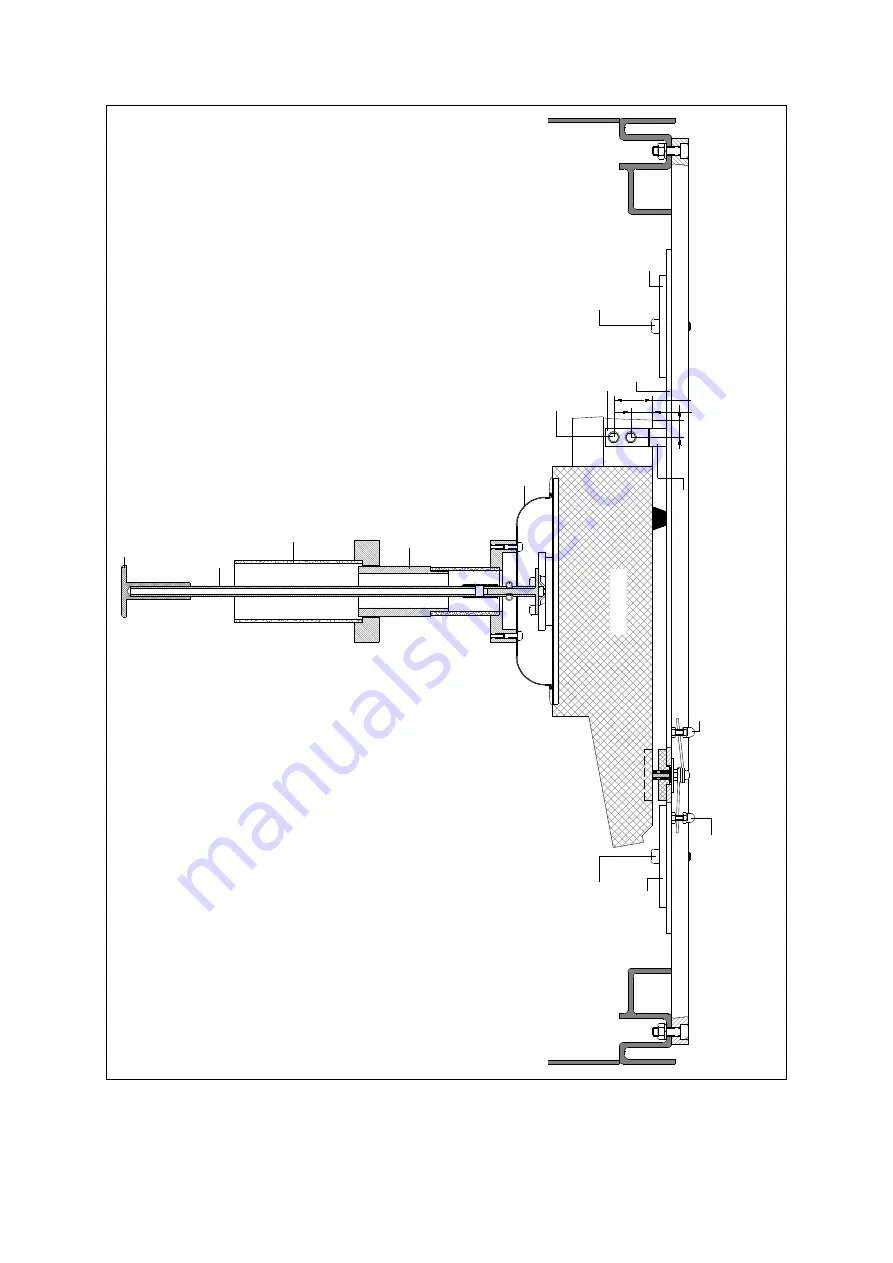
2009 by ELTRA GmbH Germany – July 2009 – Service Manual Thermostep
Page 71
12
.5
22
.5
1
0
2
6
1
1
3
2
6
1
1
0
2x
B
ohr
s
c
h
r
aube
3,
5x
9,
5
D
IN
7
5
04
K
/V
Z
26290
2
6
1
1
4
g
e
k
le
b
t
S
enk
s
c
hr
aube
m
it
Innens
ec
hs
k
ant
M
3x
12
D
IN
7991
A
2
M
ut
ter
M
3
D
IN
934
A
2
S
ec
hs
k
ant
-
H
ut
m
ut
ter
M
3
D
IN
1587
A
2
2
6
2
8
5
2
6
2
8
8
S
enk
s
c
hr
aube
m
it
Innens
ec
hs
k
ant
M
3x
12
D
IN
7991
A
2
M
ut
ter
M
3
D
IN
934
A
2
S
ec
hs
k
ant
-
H
ut
m
ut
ter
M
3
D
IN
1587
A
2
2
6
1
1
5
2
6
2
7
6
2
6
2
8
7
2
6
1
1
2
2
6
1
1
2
Z
y
li
nder
s
c
h
r
aube
m
it
Innens
ec
hs
k
ant
M
5x
18
D
IN
912
A
2
Z
y
li
n
d
er
s
c
hr
aube
m
it
Innens
ec
hs
k
ant
M
5x
18
D
IN
912
A
2
2
6
2
8
1
Fig. 4.11: Cross-section – Balance