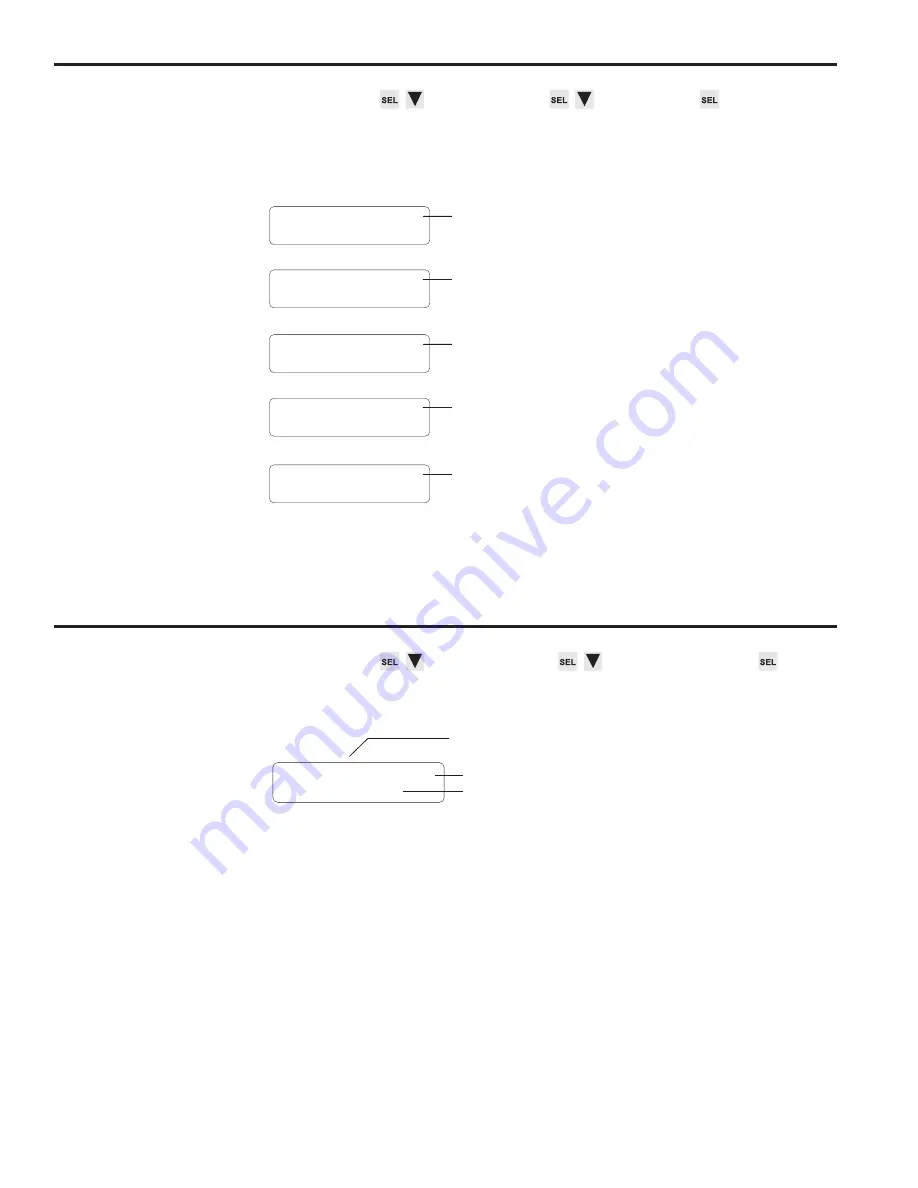
3-6 Programming
Communications
Menu Path
MAIN SCREEN
to CONFIG MENU
to COMMUNICATION
Purpose
This function sets the communications type, controller address, and baud rate for
communicating with a host computer.
Screen
TYPE:485 ADR: 1<
BAUD: 9600
Communications Type: RS-232 or RS-485
Address: 0-255
Baud Rate: 4800, 9600, 19.2Kb, 38.4Kb
Type
Use SEL to toggle between RS-232 and RS-485 communications on units shipped with
date code 9549 or newer (default setting is RS 485).
Address
The address must be unique for each controller installed on a network. This address
is used by a host computer to identify and send information to a particular controller. A
PLuS controller will ignore incoming information if the address field of the communication
packet does not match the address of the controller.
The address set through COMMUNICATIONS programming takes effect only when
the DIP switch shown in Figure 13 is set to an address value of zero. Whereas the DIP
switch can set a maximum address of “7,” the COMMUNICATIONS function can set
addresses ranging from 0-255.
Use the numeric keys and ENT to program the address.
Channel Copy
Menu Path
MAIN SCREEN
to SETUP MENU
to CHN COPY
Purpose
Channel Copy allows you to copy all setpoints to another channel in the specified pro
-
gram.
Screens
The Channel Copy function consists of four screens:
Programming
Use the numeric keys and SEL to enter program numbers.
During programming, the cursor keys allow you to move between the Source and Des-
tination screens to allow you to change values before selecting EXECUTE.
SOURCE PGM:---<
Program containing channels
DEST PGM:---<
Program containing channel
to be copied
SOURCE CHN:---<
Channel to be copied
DST CHN:---<
Destination channel to be copied to
DEST CHN:
EXECUTE<
Move cursor to EXECUTE, then press
SEL to copy program
Summary of Contents for Plus PS-6144 Series
Page 3: ......
Page 4: ......
Page 12: ...2 2 Installation Wiring Mounting Dimensions Figure 4 Mounting Dimensions ...
Page 114: ......
Page 115: ......