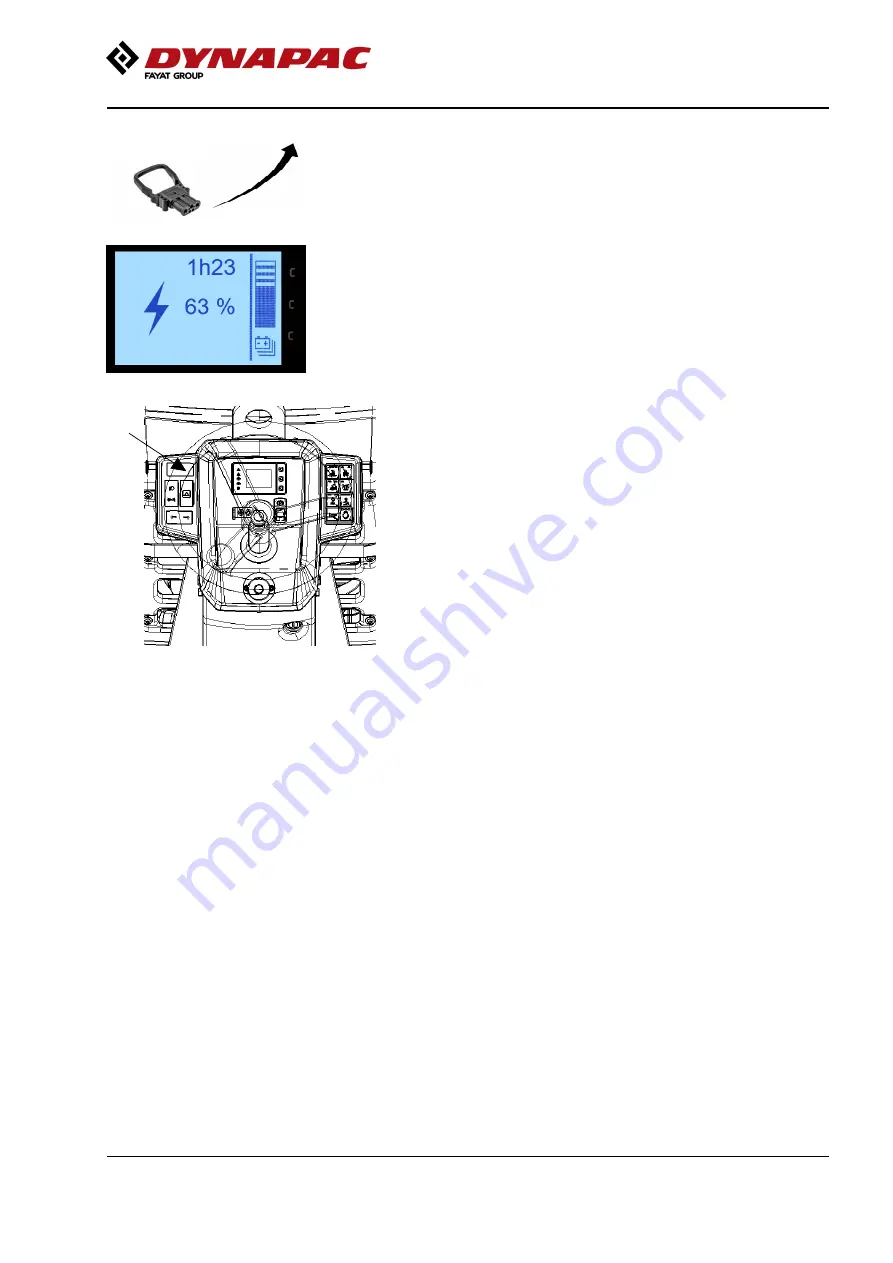
Operation
4812164901_A.pdf
2022-11-14
Incorrect disconnection during charging
(1-phase charger).
If the charger socket on the machine side is
disconnected from the machine whilest charging is in
progress the machine/battery system will still have the
"anti-drive-away" function active and the machine will
not be driveable.
Also the machine display will have an appearance
which indicates that the charger is still connected to
the machine.
Fig. Instrument panel
1. Battery ON/OFF
1
To escape this situation/status you need to re-start the
battery by turning off and then activate it again by
using the battery ON/OFF switch (1) on instrument
panel.
59
Summary of Contents for CC1000 e
Page 2: ......
Page 10: ...e 4812164901_A pdf 2022 11 14...
Page 28: ...Technical specifications 4812164901_A pdf 2022 11 14 18...
Page 66: ...Machine description 4812164901_A pdf 2022 11 14 56...
Page 82: ...Operation 4812164901_A pdf 2022 11 14 72...
Page 92: ...Operating instructions Summary 4812164901_A pdf 2022 11 14 82...
Page 94: ...Operating instructions Summary 4812164901_A pdf 2022 11 14 84...
Page 96: ...Preventive maintenance 4812164901_A pdf 2022 11 14 86...
Page 108: ...Maintenance 50h 4812164901_A pdf 2022 11 14 98...
Page 112: ...Maintenance measures every other month 4812164901_A pdf 2022 11 14 102...
Page 118: ...Maintenance measures 500 h 4812164901_A pdf 2022 11 14 108...
Page 129: ......
Page 130: ...Dynapac Compaction Equipment AB Box 504 SE 371 23 Karlskrona Sweden www dynapac com...