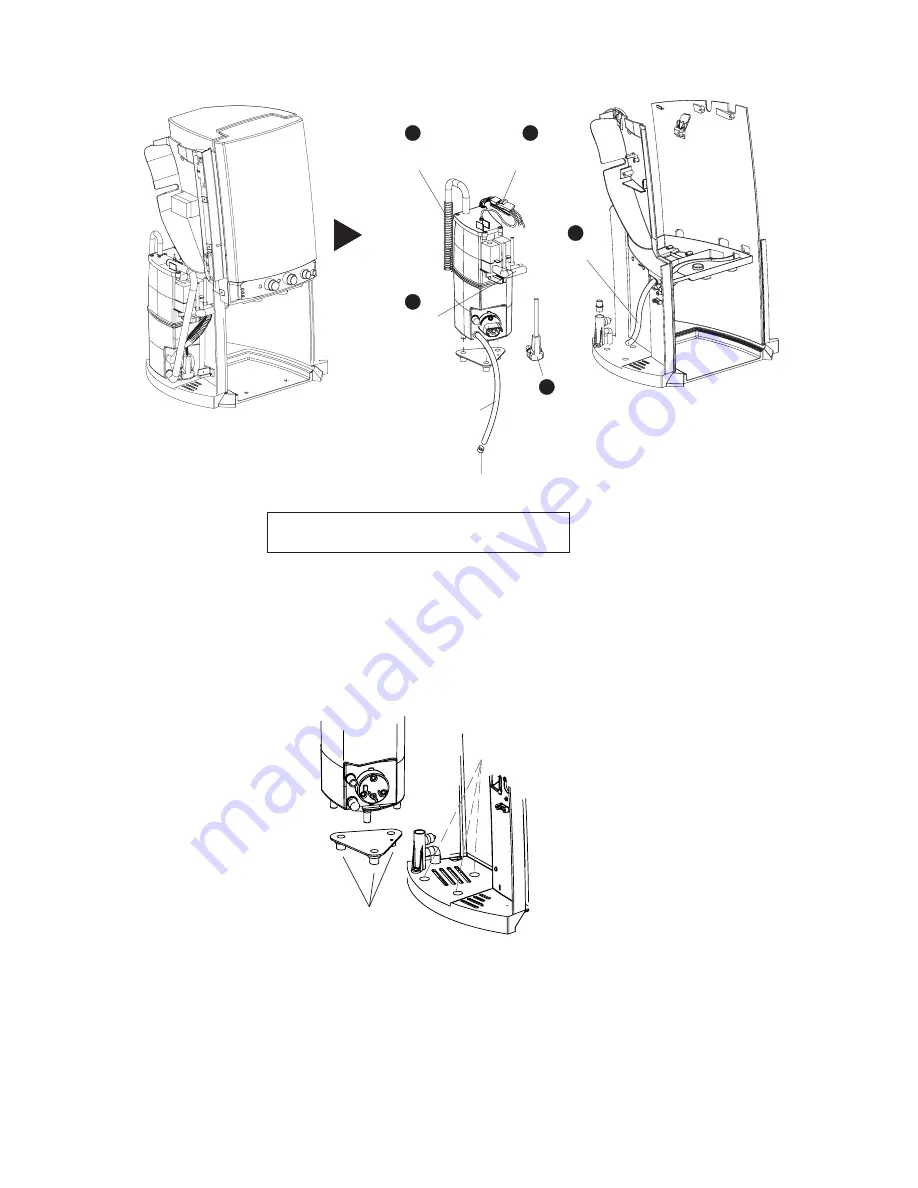
Functions (water) - 2
Version 1.36
02/2004
4. Lift the boiler out of the machine (tilt the boiler a little towards you and lift it out).
5. Take the replacement boiler and place the positioning pins under the boiler in the
corresponding holes in the machine frame.
Overflow
hose
Connector,
boiler wiring
Water inlet
hose
Drain hose
Heater
connector
Hose Plug
A
Outlet
tubes
C
E
D
B
Boiler disassembly
(machine with fixed water connection)
Positioning pins
Positioning holes
6. Connect the water outlet tubes to outlet spout on the machine frame. Make sure that the
tubes are correctly installed.
Summary of Contents for Cafitesse 50
Page 4: ...Version 1 36 02 2004 ...
Page 20: ...Version 1 36 02 2004 ...
Page 30: ...Version 1 36 02 2004 ...
Page 38: ...Programming 8 Version 1 36 02 2004 4 3 Programming flow chart service device ...
Page 56: ...Version 1 36 02 2004 ...
Page 64: ...Version 1 36 02 2004 ...
Page 78: ...Version 1 36 02 2004 ...
Page 80: ......
Page 94: ...Version 1 36 02 2004 ...
Page 95: ...Version 1 36 02 2004 6 Preventive Maintenance Contents 02 2004 Not available ...
Page 96: ...Version 1 36 02 2004 ...
Page 102: ...Version 1 36 02 2004 ...
Page 103: ...Version 1 36 02 2004 8 Service Information Bulletins Contents 02 2004 Not available ...
Page 104: ...Version 1 36 02 2004 ...
Page 105: ...Version 1 36 02 2004 9 Modification Instructions Contents 02 2004 Not available ...
Page 106: ...Version 1 36 02 2004 ...