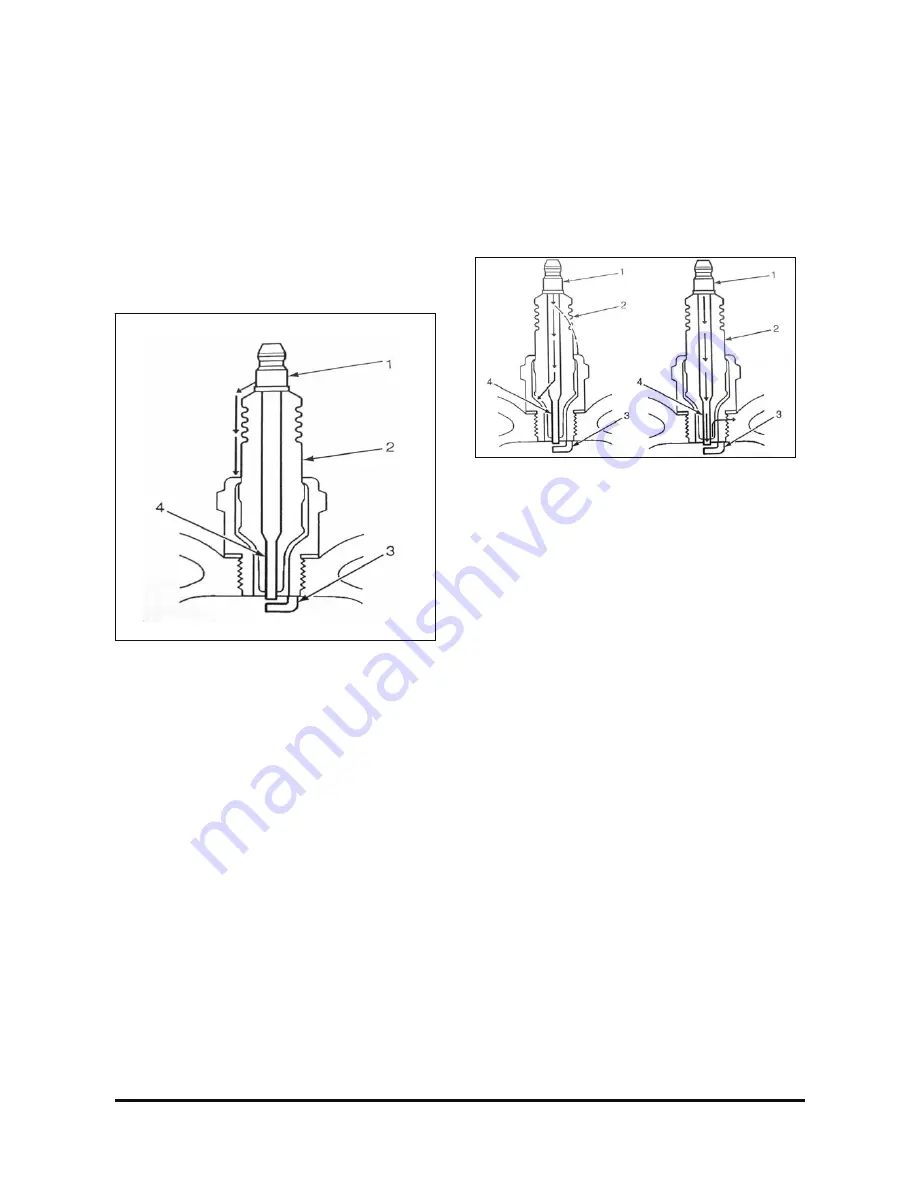
G424F(FE) Service Manual
Chapter 4. Engine Electrical System
106
b.
Best for a loose terminal post by twisting and
pulling the post. The terminal post should NOT
move.
2.
Inspect the insulator for flashover or carbon
tracking soot. See Figure 84. This is caused by
the electrical charge traveling across the insulator
between the terminal post and ground. Inspect for
the following conditions:
a.
Inspect the spark plug boot for damage.
b.
Inspect the spark plug recess area of the
cylinder head for moisture, such as oil, coolant,
or water. A spark plug boot that is saturated
causes arcing to ground.
3.
Inspect the cylinder for cracks. All or part of the
electrical charge may arc through the crack
instead of the electrodes. See Figure 85.
4.
Inspect for evidence of improper arcing. See
Figure 86.
a.
Measure the gap between the center electrode
(4) and the side electrode (3) terminals. An
excessively wide electrode gap can prevent
correct spark plug operation. Refer to Engine
Speculations for the proper gap. Adjust as
necessary.
b.
Inspect for the correct spark plug torque. The
correct torque is 20 N•m (15 lbf ft). Insufficient
torque can prevent correct spark plug
operation. An over-torqued spark plug causes
the insulator to crack.
c.
Inspect for sign of tracking that occurred near
the insulator tip instead of the center electrode
(4).
d.
Inspect for a broken or worn side electrode (3).
e.
Inspect for a broken, worm, or loose center
electrode (4) by shaking the spark plug.
(1) A rattling sound indicates internal damage.
(2) A loose center electrode (4) reduces the spark intensity.
f.
Inspect for bridged electrodes (3, 4). Despites
in the electrode (3, 4) reduce or eliminate the
gap.
g.
Inspect for worn of missing platinum pads on
the electrodes (3, 4), if equipped.
h.
Inspect for excessive fouling.
5.
Inspect the spark plug recess area of the cylinder
head for debris. Dirty or damaged threads can
cause the spark plug not to seat correctly during
installation.
Visual Inspection
1.
Normal operation – Brown to grayish-tan with
small amounts of white powdery deposits are
normal combustion by-products from fuels with
additives.
2.
Carbon fouled – Dry, fluffy, black carbon or soot
caused by the following conditions:
•
Rich fuel injectiors
- Leaking fuel injectiors
- Excessive fuel pressure
- Restricted air filter element
- Incorrect combustion
Summary of Contents for D20G
Page 2: ......
Page 5: ...Specifications TORQUE SPECIFICATIONS SB2004E00 D e c 1 9 9 8 ...
Page 14: ......
Page 16: ......
Page 138: ...Diesel Engine Engine System 124 NOTE The crankshaft must rotate freely by hand 02900058 ...
Page 254: ......
Page 256: ......
Page 260: ......
Page 341: ...4TNV98 4TNE98 Diesel Engine Section 3 Engine 87 4TNE98 Engine Figure 6 1 ...
Page 423: ...4TNV98 4TNE98 Diesel Engine Section 4 Fuel System 169 Fuel System Components Figure 7 1 ...
Page 477: ...4TNV98 4TNE98 Diesel Engine Section 7 Starter Motor 223 Starter Motor Troubleshooting ...
Page 494: ...4TNV98 4TNE98 Diesel Engine Section 8 Troubleshooting 240 Troubleshooting Charts ...
Page 495: ...4TNV98 4TNE98 Diesel Engine Section 8 Troubleshooting 241 ...
Page 496: ...4TNV98 4TNE98 Diesel Engine Section 8 Troubleshooting 242 ...
Page 498: ...4TNV98 4TNE98 Diesel Engine Section 8 Troubleshooting 244 4TNE98 Engine ...
Page 499: ...Service Manual G424FE LP Engine G424F LP Gasoline Engine G20G G25G G30G SB4320E00 Jan 2008 ...
Page 500: ......
Page 502: ......
Page 529: ...G424F FE Service Manual Chapter 2 Recommended Maintenance 29 ...
Page 534: ...G424F FE Service Manual Chapter 3 Engine Mechanical System 34 MAIN BEARINGS 0 50 UNDERSIZE ...
Page 584: ...G424F FE Service Manual Chapter 3 Engine Mechanical System 84 ...
Page 729: ...G424F FE Service Manual 229 Chapter 8 Basic Troubleshooting ...
Page 731: ...G424F FE Service Manual 231 Chapter 8 Basic Troubleshooting ...
Page 806: ......
Page 808: ......
Page 810: ......
Page 820: ...Power Train System Operation 14 Hydraulic System ...
Page 822: ...Power Train System Operation 16 Hydraulic System ...
Page 824: ...Power Train System Operation 18 Hydraulic System ...
Page 826: ...Power Train System Operation 20 Hydraulic System ...
Page 856: ......
Page 858: ......
Page 860: ......
Page 930: ......
Page 932: ......
Page 934: ......
Page 936: ......
Page 1018: ......
Page 1023: ...A374081 01 ELECTRIC SCHEMATIC MODEL D20 25 30G EM0K2 EM0K3 Cummins B3 3 ...
Page 1024: ...A654030 00 ELECTRIC SCHEMATIC MODEL D20 25 30G EM0QM EM0QN Yanmar 4TNE98 Tier 3 ...
Page 1025: ...A604500 00 ELECTRIC SCHEMATIC MODEL G20 25 30G EM0QF EM0QG GM G424F Non Certi LP ...
Page 1026: ...A604510 00 ELECTRIC SCHEMATIC MODEL G20 25 30G EM0QH EM0QJ GM G424F Non Certi GAS ...
Page 1027: ...A604516 00 ELECTRIC SCHEMATIC MODEL G20 25 30G EM0QY EM0QZ GM G424FE Tier 3 LP ...
Page 1028: ......
Page 1030: ......
Page 1059: ...Safety Section 29 Lean away from the direction of fall Lean forward ...
Page 1071: ...General Section 41 Typical Example Side Shifter Serial Number If Equipped ...