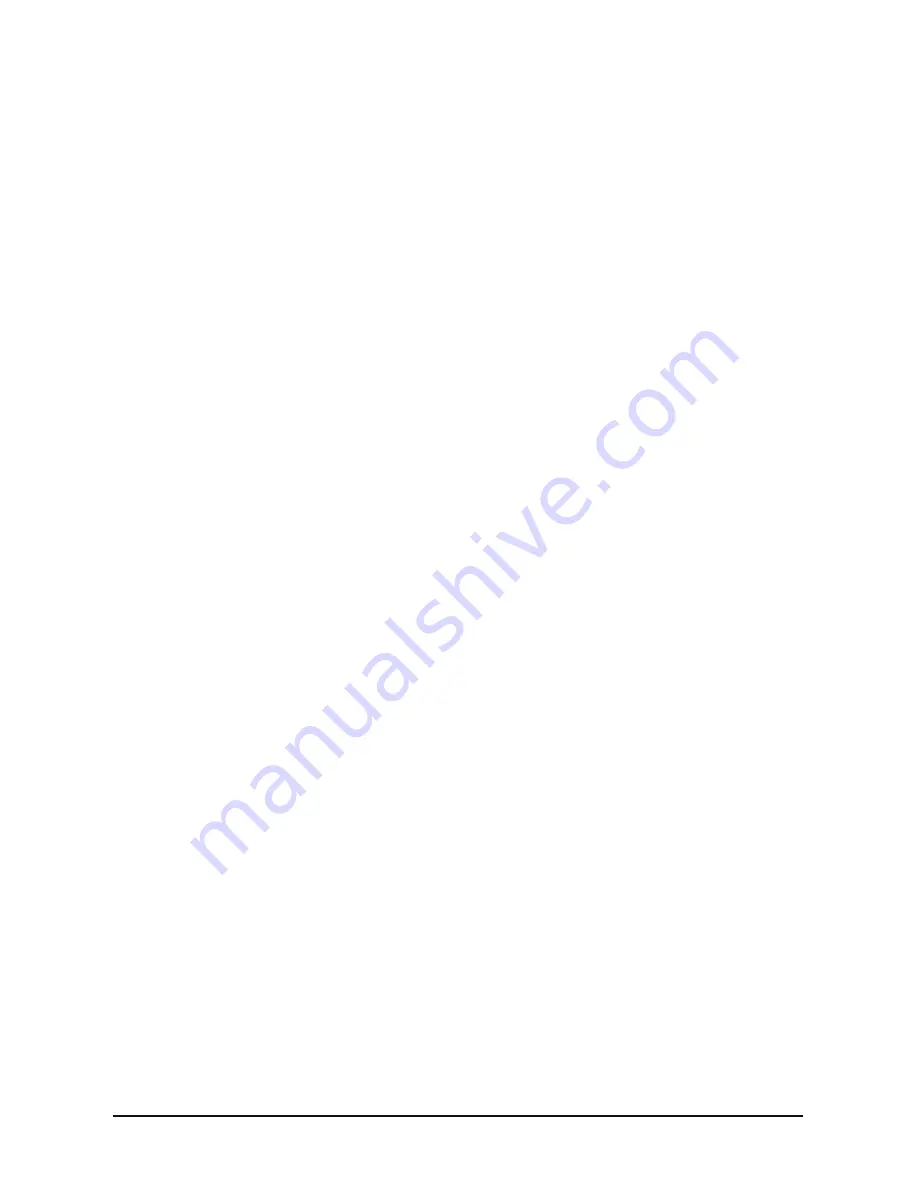
Maintenance Section
- 106 -
Inspection, Maintenance and Repair of Lift Truck Forks
The following section gives practical guidelines for
inspection, maintenance and repair of lift truck forks.
It also provides general information on the design
and application of forks and the common cause of
fork failures.
Lift truck forks can be dangerously weakened by
improper repair or modification. They can also be
damaged by the cumulative effects of age, abrasion,
corrosion, overloading and misuse.
A fork failure during use can cause damage to the
equipment and the load. A fork failure can also
cause serious injury.
A good fork inspection and maintenance program
along with the proper application can be very
effective in preventing sudden failures on the job.
Repairs and modifications should be done only by
the fork manufacturer or a qualified technician who
knows the material used and the required welding
and heat treatment process.
Users should evaluate the economics of returning
the forks to the manufacturer for repairs or
purchasing new forks. This will vary depending on
many factors including the size and type of fork.
Forks should be properly sized to the weight and
length of the loads, and to the size of the machine on
which they are used. The general practice is to use a
fork size such that the combined rated capacity of
the number of forks used is equal to or greater than
the “Standard (or rated) Capacity” of the lift truck.
The individual load rating, in most cases, will be
stamped on the fork in a readily visible area. This is
generally on the top or side of the fork shank.
y
A fork rated at 1500 pounds at 24 inch load
center will be stamped 1500x24.
y
A fork rated at 2000 kg at 600 mm load center
will be stamped 2000x600.
The manufacturer identification and year and date of
manufacture are also usually shown.
Some countries have standards or regulations which
apply specifically to the inspection and repair of
forks.
Users may also refer to the International
Organization For Standardization-ISO Technical
Report 5057- Inspection and Repair of Fork Arms
and ISO Standard 2330 - Fork Arms - Technical
Characteristics and Testing.
While there are no specific standards or regulations
in the United States, users should be familiar with
the requirements for inspection and maintenance of
lift trucks as provided by the 29 Code Federal
Register 1910.178 Powered Industrial Truck, and
ANSI/ASME Safety Standard(s) B56.1, B56.5 or
B56.6 as applicable to the type of machine(s) in use.
Environment Protection
When servicing this lift truck, use an authorized
servicing area and an approved container to collect
coolant, oil, fuel, grease, electrolyte and any other
potential environmental pollutant before any lines,
fittings or related items are disconnected or removed.
After servicing, dispose of those materials in an
authorized place and container. When cleaning the
lift truck, be sure to use an authorized area.
Summary of Contents for D20G
Page 2: ......
Page 5: ...Specifications TORQUE SPECIFICATIONS SB2004E00 D e c 1 9 9 8 ...
Page 14: ......
Page 16: ......
Page 138: ...Diesel Engine Engine System 124 NOTE The crankshaft must rotate freely by hand 02900058 ...
Page 254: ......
Page 256: ......
Page 260: ......
Page 341: ...4TNV98 4TNE98 Diesel Engine Section 3 Engine 87 4TNE98 Engine Figure 6 1 ...
Page 423: ...4TNV98 4TNE98 Diesel Engine Section 4 Fuel System 169 Fuel System Components Figure 7 1 ...
Page 477: ...4TNV98 4TNE98 Diesel Engine Section 7 Starter Motor 223 Starter Motor Troubleshooting ...
Page 494: ...4TNV98 4TNE98 Diesel Engine Section 8 Troubleshooting 240 Troubleshooting Charts ...
Page 495: ...4TNV98 4TNE98 Diesel Engine Section 8 Troubleshooting 241 ...
Page 496: ...4TNV98 4TNE98 Diesel Engine Section 8 Troubleshooting 242 ...
Page 498: ...4TNV98 4TNE98 Diesel Engine Section 8 Troubleshooting 244 4TNE98 Engine ...
Page 499: ...Service Manual G424FE LP Engine G424F LP Gasoline Engine G20G G25G G30G SB4320E00 Jan 2008 ...
Page 500: ......
Page 502: ......
Page 529: ...G424F FE Service Manual Chapter 2 Recommended Maintenance 29 ...
Page 534: ...G424F FE Service Manual Chapter 3 Engine Mechanical System 34 MAIN BEARINGS 0 50 UNDERSIZE ...
Page 584: ...G424F FE Service Manual Chapter 3 Engine Mechanical System 84 ...
Page 729: ...G424F FE Service Manual 229 Chapter 8 Basic Troubleshooting ...
Page 731: ...G424F FE Service Manual 231 Chapter 8 Basic Troubleshooting ...
Page 806: ......
Page 808: ......
Page 810: ......
Page 820: ...Power Train System Operation 14 Hydraulic System ...
Page 822: ...Power Train System Operation 16 Hydraulic System ...
Page 824: ...Power Train System Operation 18 Hydraulic System ...
Page 826: ...Power Train System Operation 20 Hydraulic System ...
Page 856: ......
Page 858: ......
Page 860: ......
Page 930: ......
Page 932: ......
Page 934: ......
Page 936: ......
Page 1018: ......
Page 1023: ...A374081 01 ELECTRIC SCHEMATIC MODEL D20 25 30G EM0K2 EM0K3 Cummins B3 3 ...
Page 1024: ...A654030 00 ELECTRIC SCHEMATIC MODEL D20 25 30G EM0QM EM0QN Yanmar 4TNE98 Tier 3 ...
Page 1025: ...A604500 00 ELECTRIC SCHEMATIC MODEL G20 25 30G EM0QF EM0QG GM G424F Non Certi LP ...
Page 1026: ...A604510 00 ELECTRIC SCHEMATIC MODEL G20 25 30G EM0QH EM0QJ GM G424F Non Certi GAS ...
Page 1027: ...A604516 00 ELECTRIC SCHEMATIC MODEL G20 25 30G EM0QY EM0QZ GM G424FE Tier 3 LP ...
Page 1028: ......
Page 1030: ......
Page 1059: ...Safety Section 29 Lean away from the direction of fall Lean forward ...
Page 1071: ...General Section 41 Typical Example Side Shifter Serial Number If Equipped ...