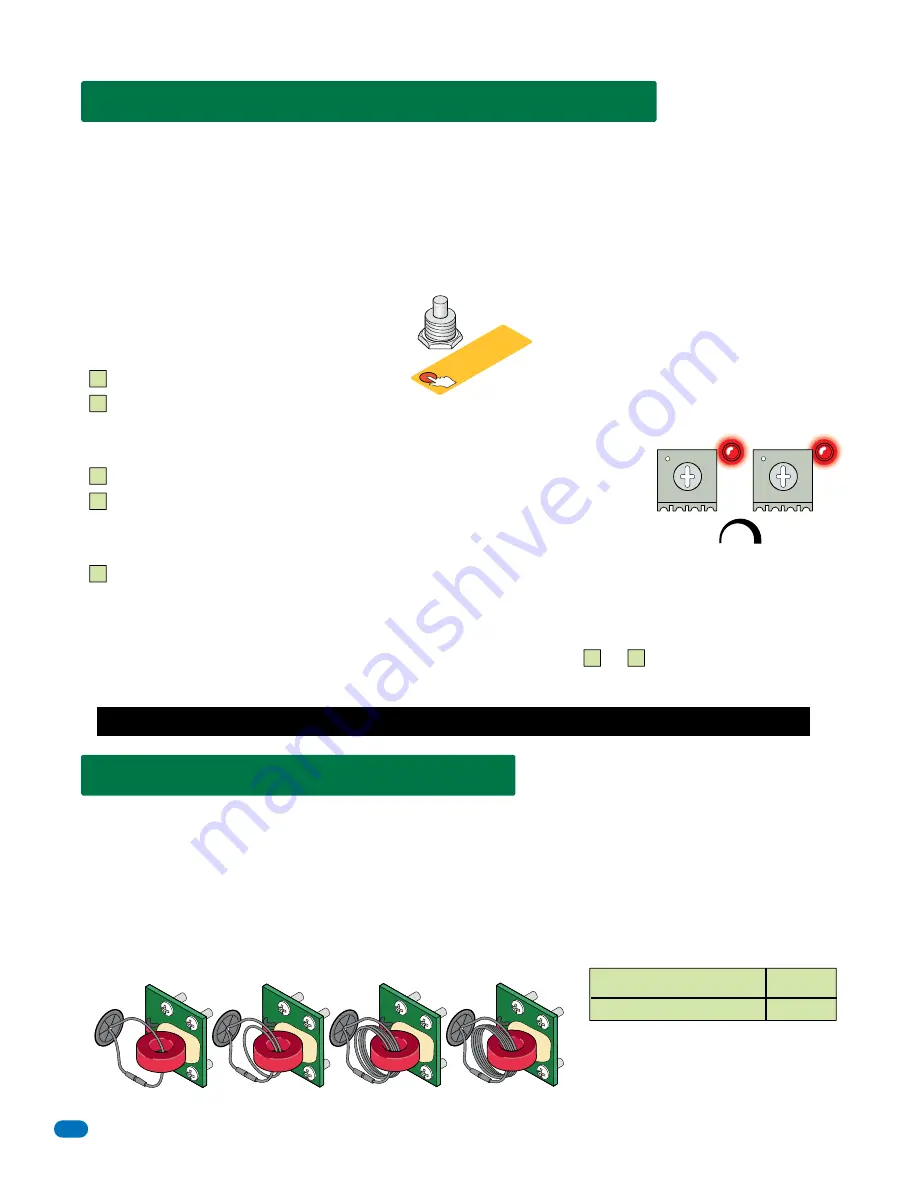
6555-065-A-12-18
20
3.4 Inherent Reverse Sensors Adjustment
PUSH T
O OPER
AT
E
technician use only
CAUTION:
Keep pedestrians and vehicles clear of the gate while adjusting and testing sensors!
Test the operator reversing sensitivity:
Press the “
Push to Operate
” button to
OPEN
the gate.
After opening gate reaches full speed, slowly rotate the OPEN reverse sensor clockwise until the LED
lights up and gate reverses direction. Rotate the OPEN reverse sensor back counter-clockwise
approximately 1/8 turn to decrease the sensitivity (LED will turn off). The gate will assume a soft
shutdown so press the “
Push to Operate
” button to cycle the operator.
Press the “
Push to Operate
” button to
CLOSE
the gate.
After closing gate reaches full speed, slowly rotate the CLOSE reverse sensor clockwise until the LED
lights up and the gate reverses direction. Rotate the CLOSE reverse sensor back counter-clockwise
approximately 1/8 turn to decrease the sensitivity (LED will turn off). The gate will assume a soft
shutdown so press the “
Push to Operate
” button to cycle the operator.
Cycle the gate a few times to be sure that it cycles completely. The current sensor may
need to be adjusted if gate will not reverse properly (See 3.5 below)
1
2
Place an immobile object along the gate path, allowing the gate to strike it while in the
open
and
close
cycles. The gate must reverse direction
after striking the object. If it does not, increase the OPEN and CLOSE reverse sensitivity (steps and ) and repeat this testing until the
correct sensitivity has been achieved in
BOTH
directions. The operator will assume a soft shutdown after striking and reversing the gate which
will require a momentary jumper wire across terminals 1 and 4 to cycle the operator again.
2
4
3
4
5
3.5 Current Sensor Adjustment
This vehicular gate operator uses a current sensing device to detect any obstructions in the path of the opening or closing gate. The current
sensor uses a sensing coil with a given number of turns through it to monitor the current flow into the operator. Each time the wire passes
through the coil, it is considered a turn. The number of turns through the sensing coil is dependant on the operating voltage of the operator,
the speed of the gate and the weight of the gate.
In general, light weight gates may require additional turns of wire through the current sensor, while heavier gates may require less turns. In
addition, the speed of the gate can affect how the current sensor works. Gates running at a higher speed may require less turns of wire
through the sensor.
CAUTION – HIGH VOLTAGE:
Be sure
power is turned OFF before changing the number of wire turns to the current
sensor.
If you are setting the reverse sensors (section 3.4 above) and reach the full sensitive position without activating the reversing
function, add an additional turn of wire through the current sensor. If you are decreasing the sensitivity and the gate will not run properly,
reduce the number of turns through the current sensor.
Reverse Sensors
Min Max
CLOSE
Sensitivity
OPEN
Voltage and Phase Turns
230 Single Phase
2
This vehicular gate operator is equipped with an inherent adjustable reversing sensor (Type A) used as entrapment protection according to UL
325 standards.
The gate will reverse direction after “physically” encountering an obstruction in either the opening or closing gate cycle
.
If the Auto-Close Timer (DIP-switch SW 1, switch 2) is ON and the gate physically encounters an obstruction during the
CLOSING
cycle, it
will reverse to the open position and
HOLD
the gate at this position (Soft shutdown condition). Another input command is needed before the
gate will reset and close again.
If the Partial Open Feature is being used and the gate physically encounters an obstruction during the
CLOSING
cycle, the gate will only
reverse to the
FULL
open limit switch setting and
NOT
the partial open setting.
For the reverse system to function correctly, the gate must be properly installed and work freely in both directions and the limit switches must
be properly adjusted before adjusting these sensors. The ideal adjustment will allow the operator to move the gate through its entire travel
cycle without reversing, but will reverse upon contact with an obstruction with no more than 40 Lbs of force. This force can be measured with
a gate scale.
LED
LED
1 Turn
2 Turns
5 Turns
6 Turns
Sample
Turns