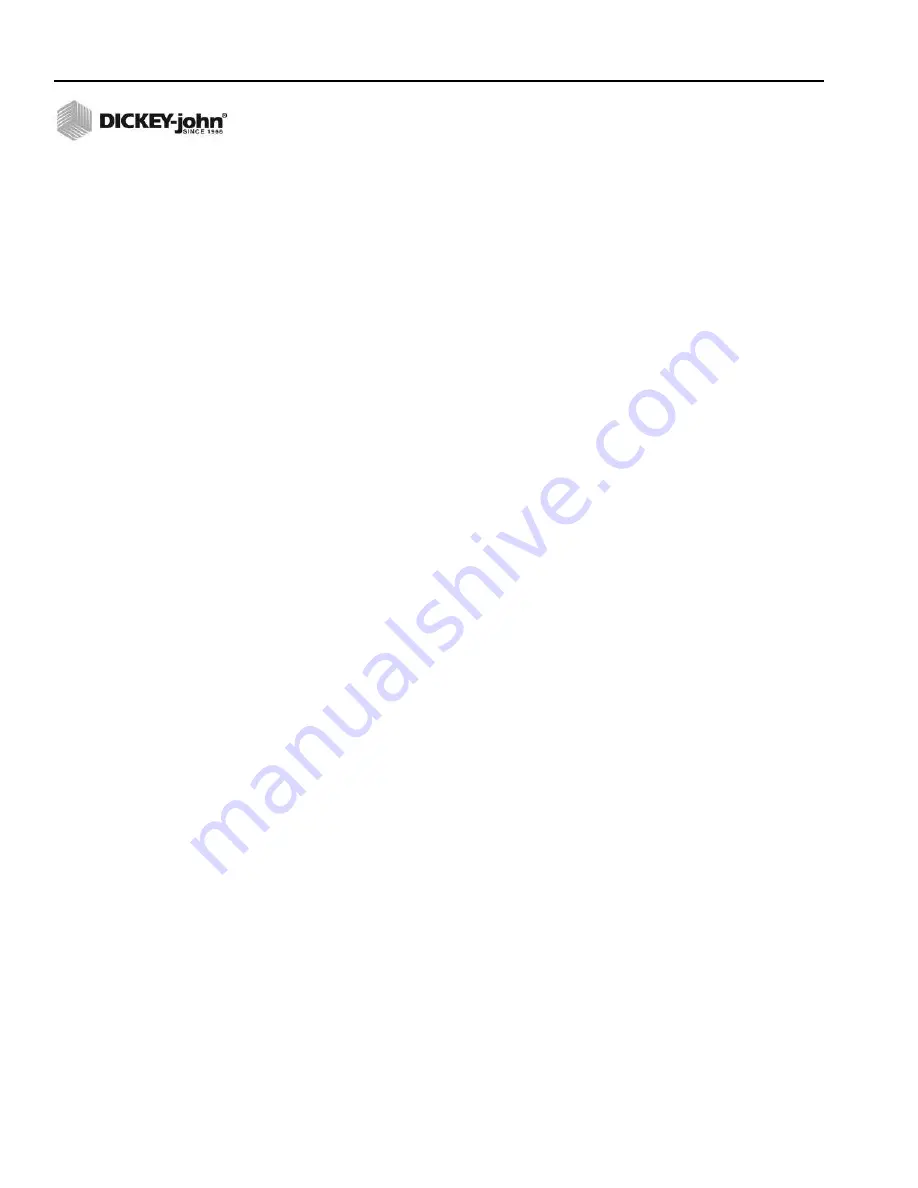
OPERATOR’S MANUAL
Control Point
®
11001-1489-201702 Rev B
52 / KEYBOARD PROGRAMMING
automatically calculates and enters during a LIQUID SYSTEM
RESPONSE routine (F11-2 and F11-3) or can be keyboard entered.
Anti-icing boom liquids may have a different offset constant than
pre-wet bar liquids because of different plumbing components.
–
PWM SAT
(Proportional valve only) - Represents the end point of
the valve operating range (maximum flowmeter pulse frequency).
The value calculates automatically during the LIQUID SYSTEM
RESPONSE routines or can be keyboard entered. Liquids
dispensed from the anti-icing boom may have different constants
than those from the pre-wet bar because of different plumbing
components.
–
SYS RSPNS
(System Response) - Adjusts the control system
response time to the hydraulic and mechanical systems of the liquid
control channel for each particular spreader vehicle. The value
calculates automatically during calibration routines but can be
fine-tuned anytime for optimum performance by keyboard entry.
–
VALV BOOST
(Valve Boost) - Increases the amount of system
response initially applied to reach final operating speed as quickly
as possible.
–
AFILT
(A Filter) - Filters the feedback signal to minimize effects of
electrical noise and mechanical vibrations. The smaller the number
the greater degree of filtering.
–
TANK LEVEL SENSOR
- Monitors the liquid level for the pre-wet or
anti-ice systems.
–
VALVE LOCK
- When Valve Lock is set to Yes, the valve is locked
in the last operating position when only the boom sections are
turned off and the master switch is left on. Valve Locking maintains
constant pressure so a quick spray pattern can resume when the
boom solenoids are turned back on.
4. Press F5 to return to the LIQUID CONFIGURATION screen. If other
liquid materials require programming, repeat the above procedures for
those materials. All pre-wet liquids should be programmed first to avoid
confusion.
TANK LEVEL SENSOR CONFIGURATION
5. The Tank Level Sensor monitors the liquid level for pre-wet or anti-ice
systems.
The sensor connects to the main harness with the lead labeled Tank or
to an adapter harness (466492040) that ties the tank level signal to pin
13 of the 16-pin granular valve connector on earlier versions of Control
Point
®
main harnesses. The tank level sensor feature must be
enabled in the Control Point
®
console before it is activated. It can be
enabled for one of the four liquid materials.The tank level will display
only when enabled and the selected material that it was enabled under
is active. (If liquid 1 is set for prewet (Yes) with tank level enabled and
liquid 2 is anti-ice (prewet No), the tank level will only display when
liquid 1 prewet is active.
If the Control Point
®
has been configured for use with anti-ice/prewet
switch input on Boom 5 to automatically switch between liquid 1 preset
Summary of Contents for Control Point
Page 1: ...CONTROL POINT CONTROL SYSTEM Operator s Manual SINCE 1966 ...
Page 5: ...OPERATOR S MANUAL Control Point 11001 1489 201702 Rev B IV ...
Page 7: ...OPERATOR S MANUAL Control Point 11001 1489 201702 Rev B 2 SAFETY NOTICES ...
Page 13: ...OPERATOR S MANUAL Control Point 11001 1489 201702 Rev B 8 INTRODUCTION ...
Page 29: ...OPERATOR S MANUAL Control Point 11001 1489 201702 Rev B 24 START UP AND FAMILIARIZATION ...
Page 77: ...OPERATOR S MANUAL Control Point 11001 1489 201702 Rev B 72 KEYBOARD PROGRAMMING ...
Page 79: ...OPERATOR S MANUAL Control Point 11001 1489 201702 Rev B 74 SYSTEM CALIBRATION ...
Page 91: ...OPERATOR S MANUAL Control Point 11001 1489 201702 Rev B 86 SYSTEM CALIBRATION ...