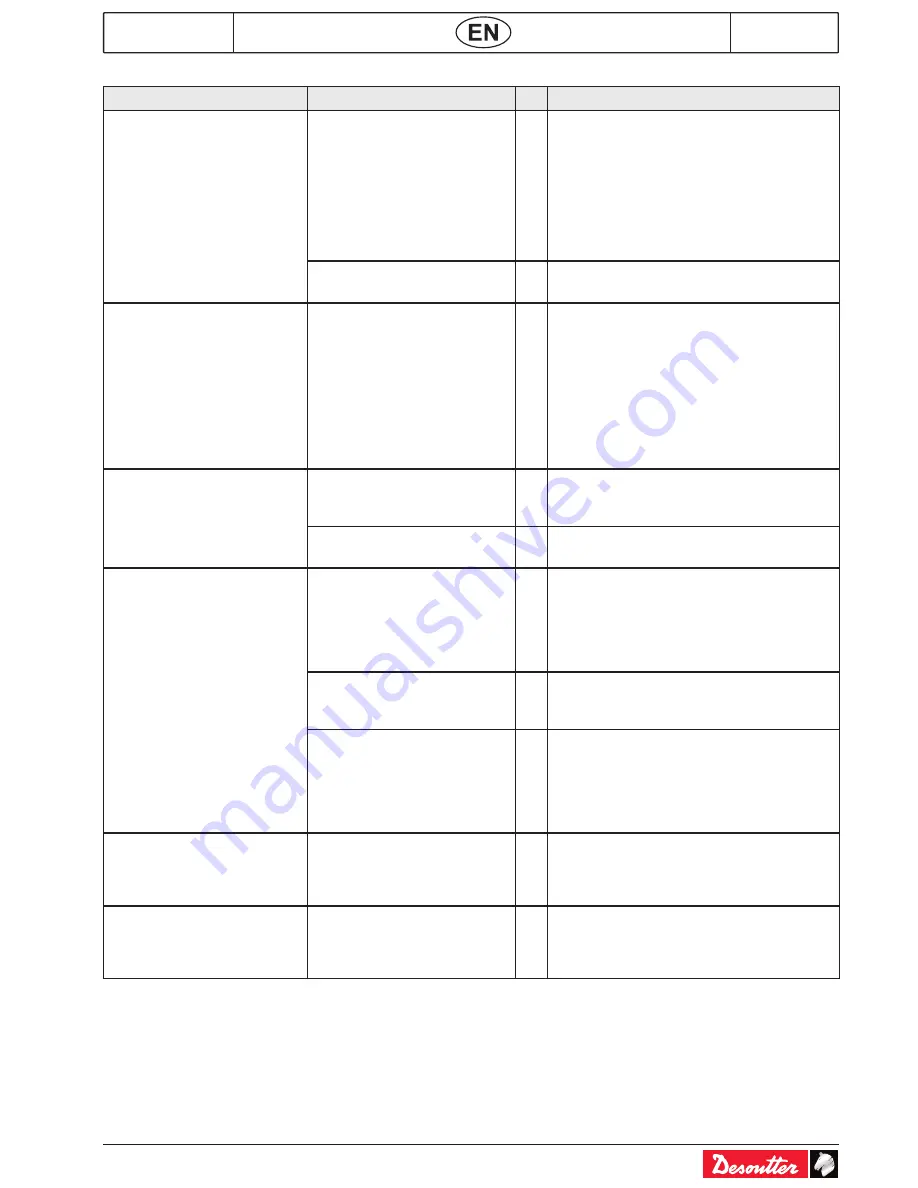
01/2018
71 / 80
6159933780
Issue no: 09
CVIL II
13.3 - Operating problems due to adjustment problems
Symptoms
Possible causes
N° Check
The tool starts then stops
immediately without running
the rundown speed cycle.
The "stall torque" instruction is
too low.
The programmed current is too
low.
The acceleration time is
too short compared to the
maximum time.
The maximum time is too short
or null.
01
Check the values programmed for the run
down and final speed sequences.
A machine part impedes the
rotation of the tool.
02
Please contact your local Customer Center.
The tool skips the rundown
sequence.
The "current" instruction is too
low.
The acceleration time is too
short.
The rundown instruction is too
low.
The maximum rundown time is
too short.
The spindle is not validated in
the sequence.
03
Check the values programmed for the run
down sequence.
Seen from the controller side,
the tool does not reach the
programmed torque or hardly
reaches it.
The power programmed during
the relevant phase is not
sufficient.
04
Check and increase the programmed value if
necessary.
The tool is not suited to the
task.
05
Check that the tool performances are
compatible with the required torque.
Dispersion or abnormal
deviation in the tightening
results.
The rundown torque is too high
as compared to the final torque.
06
Check the torque rise curves.
Reduce the speed of the tool in case of hard
joints.
Check the value of the rundown torque: The
recommended value is close to a quarter of
the final torque.
The deceleration between the
rundown phase and the final
phase is too slow.
07
Reduce the transition interval between the
rundown and tightening phases.
The tightening speed is too
high; the consequence of inertia
is the significant overstepping
of the set value.
08
Reduce the speed of the tightening phase.
The technology of electric motors equipped
with a "resolver" allows the speed reduction
up to 1 % of the maximum speed of the tool.
In most case, a rotation of 20rpm will be the
best compromise.
The torque displayed by the
controller is far from the actual
torque.
The coefficient of the tool
nominal load has been updated
by mistake.
09
This coefficient should be equal to 1, except
in the case of additional reduction gears.
Check its value in the "Parameter/Tool"
menu.
The torque value is constantly
equal to 0; there is no error
message.
The coefficient of the tool
nominal load has been set to 0
by mistake.
10
This coefficient should be equal to 1, except
in the case of additional reduction gears.
Check its value in the "Parameter/Tool"
menu.