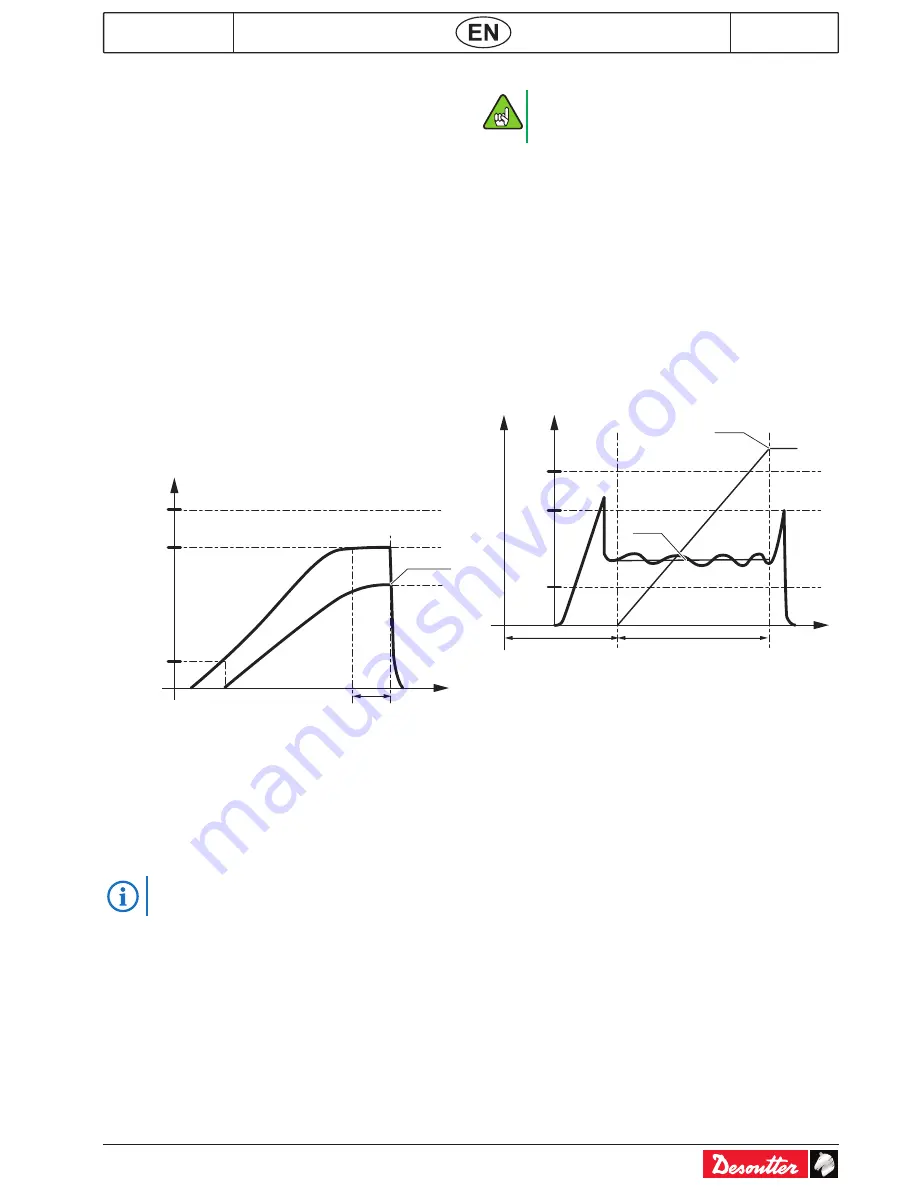
01/2018
63 / 80
6159933780
Issue no: 09
CVIL II
11.5 - Stall torque controlled tightening
This tightening strategy is used to check the tuning of
a tightening unit in static mode with the possibility of
monitoring the linearity of its torque transducer.
The stall torque tightening is also used when you want to
keep a constant torque on a joint, either to compensate
a creep in a seal, or to keep a load on a joint during a
complex operation.
During this phase, as long as the motor has not reached
its torque value, the motor is controlled on the speed
loop.
When the stall torque is reached, the torque control and
stall are performed on the current loop.
The stall time can be set between 0.1 and 10 seconds.
To avoid the overheating of the motor, in this type of
application it is recommended to oversize the tightening
unit.
The thermal contact located in the motor provides
protection in case of overheating.
The max. torque must be programmed to a value higher
than the desired stall torque.
The recorded values are the following: final torque in bolt
and final angle.
Torque
Time
Final
angle
Stall
time
Stall torque
Angle
threshold
Max.
Spindle stop
● IF stall time elapsed
● OR torque > max. torque
● OR angle > max. angle
Accept report
● IF min. torque ≤ final torque ≤ max. torque
● IF min. angle ≤ final angle ≤ max. angle
Bandwidth has to be set to 128Hz.
11.6 - Prevailing torque control
In the Pulse mode, the prevailing torque
parameter cannot be higher than the tool max
torque continuous.
This phase allows you to check the residual torque
(prevailing torque) that results, for instance from the
thread formed with tapping screws.
It is useful to know if the thread is formed correctly
during the desired number of rotations without untimely
locking or tapping deficiency.
The initial time out allows you to start the readings when
the tool speed is stabilised.
The memorised result is the mean of the torque readings
during the acquisition phase.
The system stops the acquisition of the torque and angle
when the motor stops.
The torque pulse at the motor stop is not taken into
account.
Torque
Angle
Time
Mean torque
Target angle
Max
Min
Safety
Rise delay
time or angle
Data aquisition
Spindle stop
● IF angle ≥ target angle
● OR torque> safety torque
Accept report
● IF min. torque ≤ torque ≤ max. torque