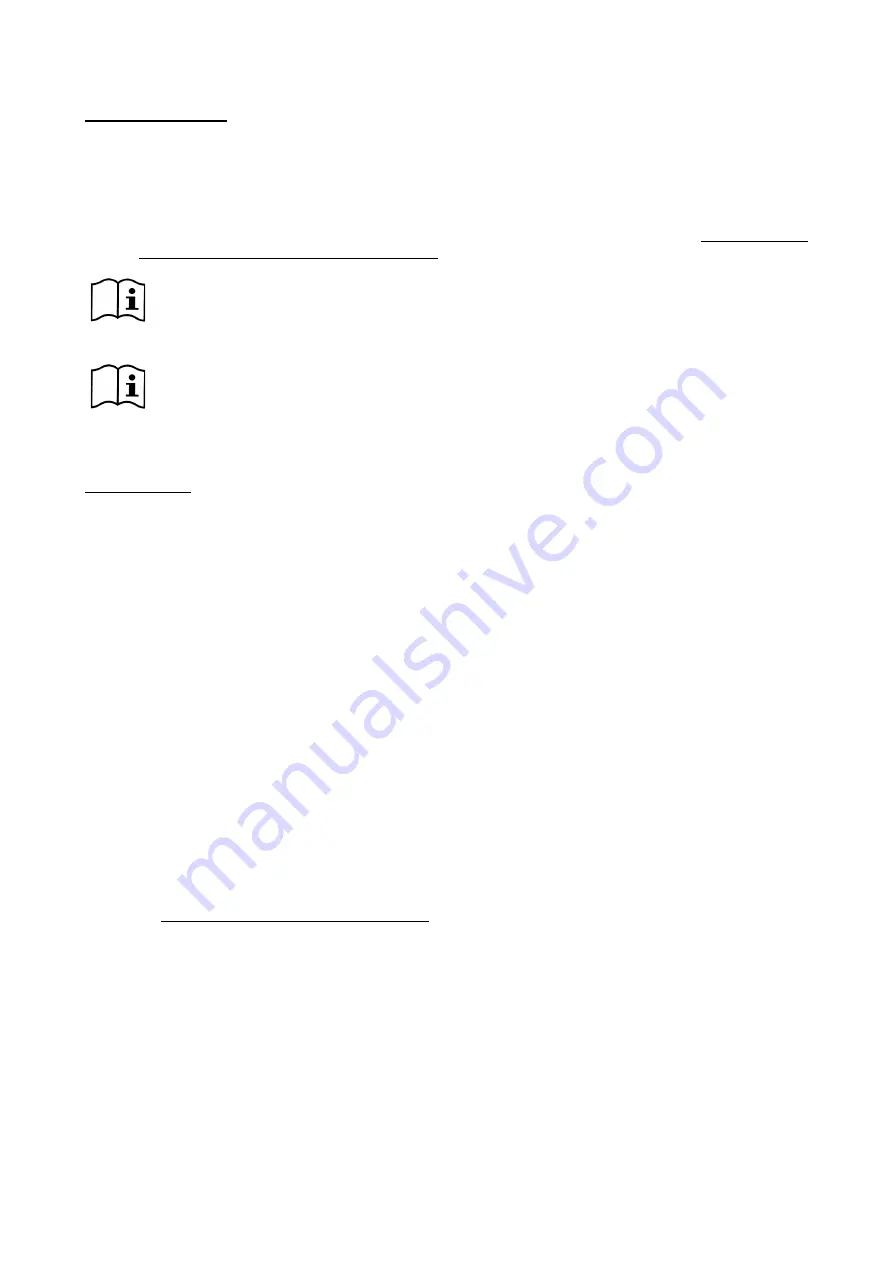
ENGLISH
106
Minimum frequency mode: this mode allows you to set the frequency (FZ) below which it is considered that there is zero flow. In this
mode the electropump stops when its rotating frequency falls below FZ for a time of T2 (see par. 6.6.3).
IMPORTANT: An incorrect setting of FZ causes:
1.
If FZ is too high, the electropump could cut out even in the presence of flow and then start again as soon as the pressure
falls below the restarting pressure (see 6.5.5). So there could be repeated episodes of switching on and off, even quite close
together.
2.
If FZ is too low, the electropump might never stop even in the absence of flow, or with very low flows. This situation could
lead to damage of the electropump due to overheating.
Since the zero flow frequency FZ may vary as the Setpoint varies, it is important that
:
.
1.
Whenever the Setpoint is changed you check that the set value of FZ is adequate for the new Setpoint.
The auxiliary set points are disabled if the flow sensor is not used (FI=0) and when FZ is used in minimum frequency
mode (FZ ≠ 0)
.
CAUTION: the minimum frequency mode is the only operating mode without flow sensor admitted for multiple inverter systems.
Self-adaptive mode: this mode consists of a particular and efficient self-adaptive algorithm which allows operation in nearly all cases
without any problem. The algorithm acquires information and updates the relative parameters during operation.
To ensure optimal
operation, there should not be any substantial periodic variations on the hydraulic system, which cause significant differences between
values (such as solenoid valves that exchange hydraulic sectors with very different characteristics), as the algorithm adapts only to
one of these and cannot provide the expected results as soon as switching is performed. On the other hand, if the system remains
with similar characteristics (elasticity length and minimum required flow rate) there are no problems.
On each restart or reset of the unit, the self-learnt values are reset, and therefore a specific time interval is required to self-adapt.
The algorithm used, measures the various sensitive parameters and analyses the unit status to detect the presence and entity of the
flow. For this reason, and to avoid false errors, correct parameter settings are fundamental, and in particular:
•
Ensure that there are no system oscillations during regulation (if this occurs, adjust parameters GP and GI section 6.6.4
and
6.6.5)
•
Enter the correct rated current setting RC
•
Set an adequate minimum flow FT
•
Set the correct minimum frequency FL
•
Set the correct direction of rotation
WARNING: the self-adaptive mode is not allowed on multi-inverter systems.
IMPORTANT: In both operating modes the system is able to detect the lack of water by measuring the current absorbed by the pump
and comparing it with the parameter RC (see 6.5.1). If the maximum operating frequency FS is set with a value that does not enable
absorption of a value close to the current under full load of the pump, false water failure errors (BL) may occur. In this case, remedy
the situation as follows: turn on the utilities to reach the frequency FS and at this value, check pump absorption (easily seen on phase
current parameter C1 in the User menu), then set the current value reading on RC.
6.5.9.1.1
Fast self-learning method for auto-adaptive mode
The self-learning algorithm is adaptable to various systems automatically on acquisition of information on the type of system.
The system set-up process can be shortened by using the quick learning the procedure:
1)
Turn on the unit or, if already powered, press MODE SET + - simultaneously for 2 seconds to generate a reset.
2)
Enter the Installer menu (MODE SET -) set FI to 0 (no flow sensor) then in the same menu go to item FT.
3)
Turn on a utility and run the pump.
4)
Slowly turn off the utility to reach minimum flow (utility closed) and when this value stabilises, note the corresponding
frequency.
5)
Wait 1-2 minutes for the simulated flow reading; this is confirmed by shutdown of the motor.
6)
Turn on a utility to achieve a frequency that is 2 – 5 [Hz] greater than the previous frequency reading, and then wait 1-
2 minutes for another shutdown.
IMPORTANT: the method is only effective if, while gradually closing the utility in point 4) the frequency remains at a fixed
value through to reading of the flow VF. It should not be considered a valid procedure if, after closure, frequency reaches 0
Summary of Contents for MCE-150/P
Page 308: ...306 IEC 60634 1...
Page 309: ...307 1 6 1 1...
Page 312: ...310 1 2 1 1 1 1 2 5 2 1 2 1 2...
Page 313: ...311 2 1 1 2 1 2 L L L 2 2 4 2 15 2 2 1 1a...
Page 314: ...312 2a 3a 4b 1b 127 240 240 480...
Page 318: ...316 GP GI 6 6 4 6 6 5 7 A B C D...
Page 323: ...321 50 60 7 DC AC 50 60 8 6 2 1 5 36 36 12 3 3 3 3 2 13 9 10 8...
Page 325: ...323 I1 F1 I1 6 6 13 2 I2 P2 6 6 13 3 I3 F3 6 6 13 4 I4 1 F4 6 6 13 5 10 GND 7 I1 I2 I3 I4...
Page 326: ...324 3 13 64 X 128 4 MODE SET 11 SET 9 MODE 1 SET 11 3 EEprom SET 6 SET MODE 3 1 11...
Page 327: ...325 3 2 1 2 3 2 1 MODE SET MODE 10 2 2 5 5 5 2 2 12...
Page 329: ...327 12 SET 14 15 13 15 3 3...
Page 331: ...329 15 14 3 4 PW 6 6 16 GO SB...
Page 332: ...330 4 4 1 Link 8 4 2 4 2 1 Link Link 15...
Page 333: ...331 17 Link 4 2 2 0 5V 4 20 A 0 4 2 2 1 FI FI 4 2 2 2 FZ 6 5 9 1 4 2 2 3 0 5 4 20 A 0 5 0...
Page 336: ...334 4 4 2 2 4 2 5 4 5 ET 6 6 9 FL 4 5 1 4 5 1 1 ET ET ET ET 0 ET 6 6 9 4 5 1 2 23 23...
Page 339: ...337 FZ FZ 2 35 FZ 37 FZ FZ FZ FZ FI 0 FZ FZ 0 5 1 7 6 GI GP FL TB...
Page 362: ...360 OC 10 6 OF 10 6 33 8 8 1 PMW 4 2 8 2 8 3 8 3 SET EE EEprom FLASH...
Page 548: ...546 IEC 364 1 inverter...
Page 549: ...547 1 Inverter inverter inverter 6 inverter 1 1...
Page 552: ...550 1 2 1 1 inverter inverter 1 1 2 5 inverter inverter 2 1 inverter inverter 2 1 2 C...
Page 554: ...552 2a 3a 4b...
Page 558: ...556 GP GI 6 6 4 6 6 5 inverter 7 A B C D...
Page 567: ...565 3 2 1 2 3 2 1 MODE SET Setpoint MODE 10 ONOMA TOY MENOY 2 Setpoint 2 5 5 5 2 2 12...
Page 571: ...569 15 15 14 3 4 Password inverter password password inverter password PW 6 6 16 GO SB FAULT...
Page 728: ...726 IEC 364 1 1...
Page 729: ...727 1 1...
Page 732: ...730 1 2 1 1 1 2 5 2 1 2 1 2 C...
Page 733: ...731 2 1 1 0 2 1 2 L L L 2 2 4 2 15 2 2 1 1...
Page 734: ...732 2a 3a 4b...
Page 738: ...736 GP GI 6 6 4 6 6 5 7 2 2 3 2 Press Flow 6 A B C D...
Page 743: ...741 DC AC 50 60 Hz 7 DC V AC 50 60 Hz Vrms V 8 6 V 2 1 5 V 36 36 12V A 3 3 3 3 2 13 8 10 8...
Page 744: ...742 12 J5 I1 11 17 16 18 16 17 I2 11 15 16 18 15 16 I3 11 14 13 18 13 14 I4 11 12 13 8 12 13 9...
Page 746: ...744 3 13 Oled 64 X 128 4 MODE SET 11 SET or 9 MODE 1 SET 10 3 EEprom SET SET or MODE...
Page 751: ...749 14 14 3 4 PW 6 6 16 GO SB FAULT...
Page 752: ...750 4 4 1 Link 8 4 2 4 2 1 Link Link 15...
Page 966: ...964 IEC 60634 1...
Page 967: ...965 1 6 1 1...
Page 970: ...968 1 2 5 2 1 2 1 2 2 1 1...
Page 971: ...969 2 1 2 L L L 2 2 4 2 15 2 2 1 1a 1a...
Page 976: ...974 3 2 2 3 2 Press Flow 6 A B C D...
Page 981: ...979 50 60 7 DC AC 50 60 8 6 2 1 5 36 36 12 3 3 3 3 2 13 2 10 8...
Page 982: ...980 5 J5 I1 11 17 16 18 16 17 I2 11 15 16 18 15 16 I3 11 14 13 18 13 14 I4 11 12 13 8 12 13 8...
Page 984: ...982 SET 9 3 EEprom SET 6 SET MODE 3 1 11 3 2 1 2 3 2 1 MODE SET MODE 10 2 2 5 5...
Page 986: ...984 4 3 2 2 12 SET 7 15 13...
Page 987: ...985 8 3 3 psi 12 GO SB BL LP HP EC...
Page 989: ...987 PW 6 6 16 4 4 1 Link 8 4 2 4 2 1 Link Link 15...
Page 993: ...991 4 4 2 2 4 2 5 4 5 ET 6 6 9 FL 4 5 1 4 5 1 1 ET ET ET ET 0 ET 6 6 9 4 5 1 2 23 23...
Page 1020: ......
Page 1021: ......
Page 1022: ......
Page 1023: ......