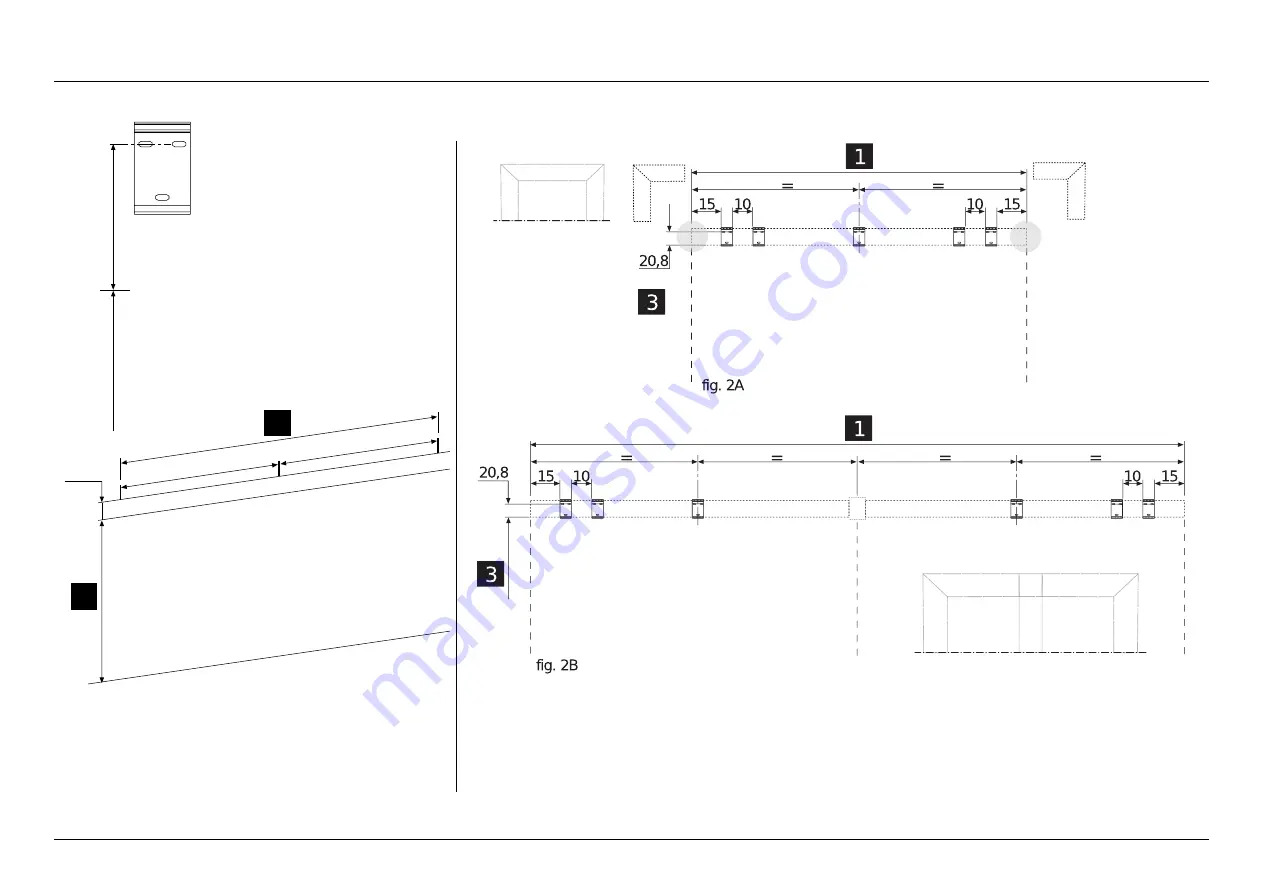
8 of 64
CORRADI S.R.L.
- INSTALLATION MANUAL - PERGOTENDA ® MAESTRO
REV.1 - 11.2019
1 WALL INSTALLATION
fig. 1
- Trace on the wall
- the slot fixing lin
e at the height indicated in the project drawing
(
3
) + 20.8 cm;
- the external line of the total width (
1
);
- in case of side-by-side structures, trace the intermediate fixing
measures of the central brackets.
FLOOR
HEIGHT UNDER BEA
M
fig. 2A
- Plate-to-wall fixing drawing for single module.
fig. 2B
- Plate-to-wall fixing drawing for side-by-side module.
Ex
ter
nal side
Ex
ter
nal side
Ex
ter
nal side
Ex
ter
nal side
Central
pillar
HEIGHT UNDER BEA
M