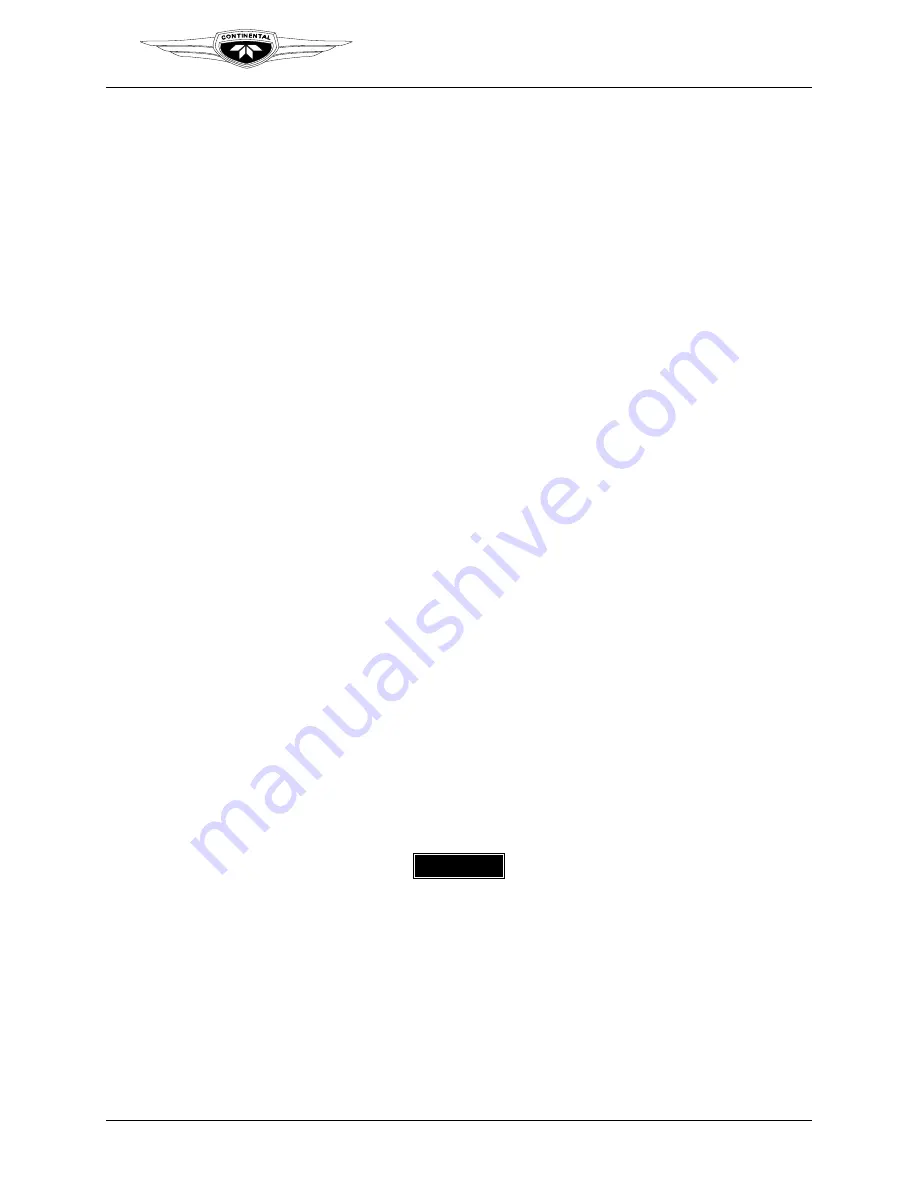
Teledyne Continental Motors, Inc.
TM
Non-Overhaul Removal and Replacement
IOF-240 Series Engine Maintenance Manual
10-13
31 August 2007
Change 1
9.
Remove the spacer (11).
10.
Using a blind oil seal puller, remove and discard the oil seal (9).
11.
Remove and discard the O-ring (10).
12.
Return the alternator core for credit.
10-4.2. New Alternator Preparation
Procedure
1.
Install the spacer (11) (Figure 10-4).
2.
Install a new Woodruff key (8).
3.
Install the hub assembly (5) on the alternator shaft.
4.
Install a new oil seal (9) in the alternator (4) using an arbor press and an Oil Seal
Installation Tool (See Chapter 3, Special Tools and Supplies).
5.
Lubricate a new O-ring (10) (Figure 10-4) with clean 50 weight aviation engine oil
and install the O-ring on the alternator shaft.
6.
Place the toothed portion of drive hub gear in shielded vise jaws and tighten vise just
enough to prevent rotation during torquing of the nut (6).
7.
Using a currently calibrated torque wrench, torque the nut to the lower limit specified
in Appendix B. If the cotter pin does not align, gradually increase torque to align the
castellated nut with the cotter pin hole. If alignment cannot be achieved within the
torque limits, replace the nut (6). Do not over torque!
8.
Install a new cotter pin (7) and secure it in accordance with Appendix C instructions.
9.
Install a new gasket (1).
10-4.3. Direct Drive Alternator Installation
Procedure
1.
Perform a “Gear Tooth Inspection” on the face gear according to instructions in
Section 9.3.1. of the Overhaul Manual (OH-22).
2.
Install the drive hub assembly according to instructions in section 10-4.2, “New
Alternator Preparation.”
3.
Install the alternator (4) (Figure 10-4) on accessory case studs with a new gasket (1).
WARNING
Forceful alternator installation can cause mount lug failure. If
interference exists, inspect the mounting studs for bending;
replace bent studs.
4.
Verify the alternator enters the crankcase without binding and the mounting flange is
properly seated against the crankcase. Do not use force the alternator in the cavity. Do
not attempt to tighten the alternator mounting fasteners if the flange does not seat
against the crankcase. If the mounting studs do not align with the mounting lug holes,
inspect the studs with a tool maker’s square.