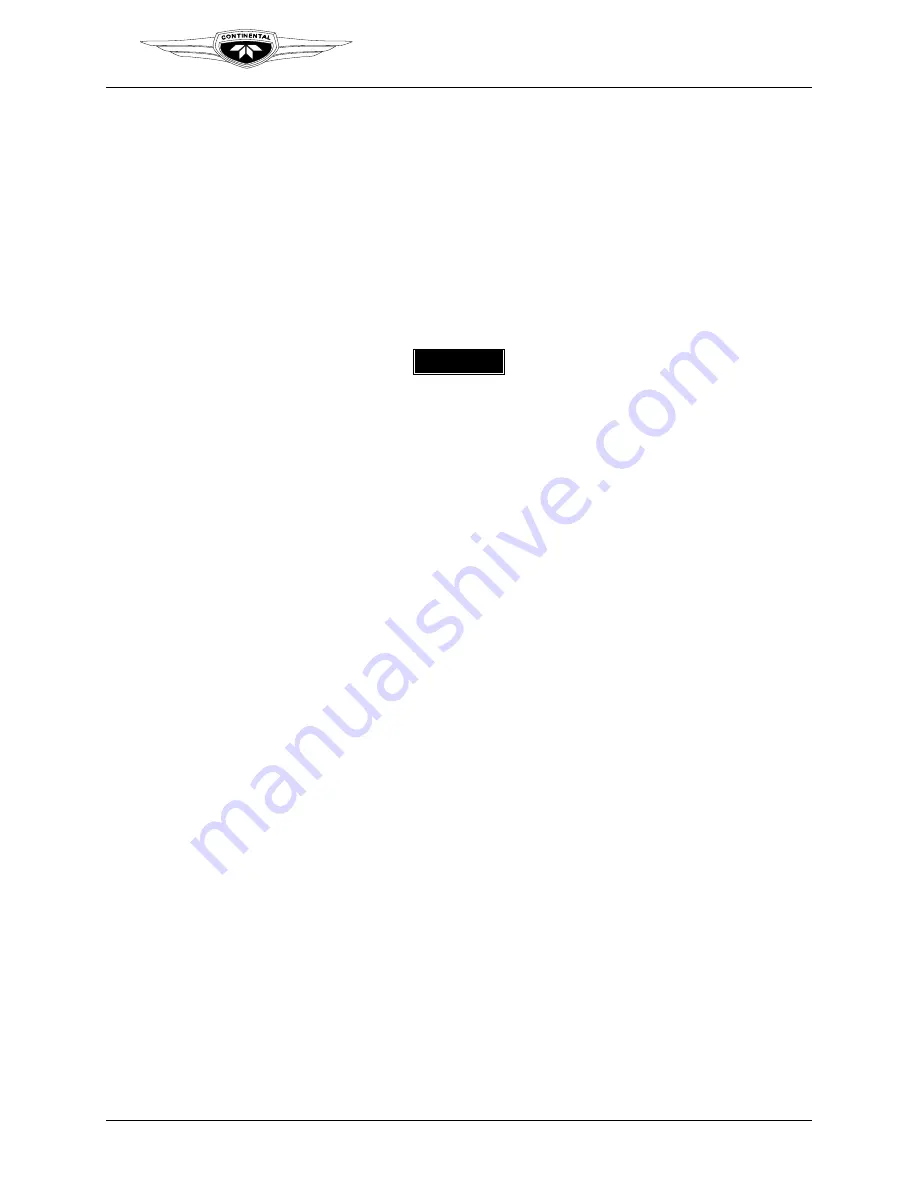
Teledyne Continental Motors, Inc.
TM
Maintenance
Inspections
IOF-240 Series Engine Maintenance Manual
7-23
31 August 2007
Change 1
6)
Rotate the propeller again before rechecking leakage to reset the valves in the
normal manner.
7)
If leakage around the valve cannot be corrected by staking, remove and repair
the cylinder. Refer to Table 7-4 “Summary of Seal Checks and Corrective
Actions” for corrective action guidelines.
3.
Each piston ring has a gap and the rings are assembled on the piston in a staggered
fashion to prevent dynamic seal pressure loss. A low pressure reading during
Differential Pressure Testing may be attributed to alignment of the piston ring gaps.
To check for this occurrence:
a.
Reduce the pressure in the cylinder to 20 psi.
WARNING
Do not stand or place equipment within the arc of the
propeller.
b.
Rotate the crankshaft several times to work the piston through top dead center
several times to cause the piston rings to reseat to the piston land and possibly re-
sealing.
c.
Re-pressurize the cylinder to 80 psi.
d.
Check the cylinder pressure gauge reading.
e.
Refer to Figure 7-7. Rotate the propeller backward to move the piston over the
ring gap when checking the compression if the gap happens to be right at the top
or bottom of the cylinder barrel.
1)
If the cylinder pressure gauge reading is
higher
than the minimum acceptable
cylinder pressure leakage limit and has no valve leakage, then the cylinder is
acceptable, and does not require a static seal leak check. Proceed to the next
cylinder to be tested.
2)
If the cylinder pressure gauge reading is
lower
than the minimum acceptable
cylinder pressure leakage limit, run up the engine according to the engine
operating procedures in TCM’s Installation and Operation Manual (OI-22).
Repeat the Cylinder Differential Pressure Test after shutting down the engine.
If the cylinder pressure gauge reading still remains
lower
than the minimum
acceptable cylinder pressure leakage limit, check the static seals as described
in step 4.